01.04.2013
Детали машин и механизмов
Машины в зависимости от сложности состоят из узлов и деталей. При этом узлы могут быть разъемными и неразъемными.
Деталь — элементарная часть машины, изготавливаемая без процесса сборки, узел — сборочная единица, включающая отдельные детали. Детали машины могут быть общего и специального назначения.
К деталям общего назначения относятся детали, входящие в состав машин различных конструкций и выполняющих разные задачи: элементы разъемных и неразъемных соединений (гайки, болты, винты и т. п.), части механизма преобразования движения одного направления в другое, валы и оси, муфты, подшипники и т. д.
К деталям специального назначения относятся такие детали, которые выполняют специфические функции в определенных машинах, например, поршни, специальные валы, копиры, рычаги и т. п.
Детали первой группы изучают в курсе «Детали машин»; второй группы — в специальных дисциплинах: «Подъемно-транспортные механизмы», «Станки и инструмент» и т. д.
Основные понятия и определения.
Детали общего назначения делятся на следующие три основные группы:
- механические передачи (зубчатые, винтовые, ременные и т. д.);
- детали и узлы передач (валы, подшипники, муфты, шестерни и т. д.);
- детали соединений (болты, гайки, шпильки, винты, шплинты, заклепки и т. д.).
Машина — это механическое устройство, предназначенное для выполнения определенной задачи, связанной с процессом переработки сырья или полуфабрикатов в готовую продукцию, преобразованием одного вида энергии в другой.
Из деталей составляются механизмы, представляющие собой систему подвижно соединенных деталей или тел, обеспечивающих возможность преобразования движения одного или нескольких тел в другое целесообразное движение одного или нескольких тел.
Основной особенностью деталей является их работоспособность, то есть состояние детали, при котором она способна выполнять заданные функции. Критериями работоспособности деталей машин являются прочность, жесткость, износостойкость, теплостойкость.
Под прочностью понимается свойство материалов детали в определенных условиях, не разрушаясь, воспринимать те или иные нагрузки.
Жесткостью называется способность деталей сопротивляться изменению их формы под действием приложенных нагрузок.
Износостойкость — это сопротивление деталей машин и других трущихся изделий изнашиванию — процессу разрушения поверхностного слоя детали.
Под теплостойкостью понимают способность детали осуществлять свое назначение в заданном интервале температур, определенном технологическим процессом производства продукции.
Механизмы, преобразующие вид передаваемого движения.
Для приведения в движение машин — орудий необходима механическая энергия. Чаще всего механическая энергия, получаемая в машинах — двигателях, представляет собой энергию вращательного движения.
В современных условиях передача энергии может осуществляться механическими, гидравлическими, пневматическими и другими устройствами.
Передача — это устройство, предназначенное для передачи энергии от двигателя к исполнительному механизму. Механическими передачами, или просто передачами, называются механизмы для передачи энергии, как правило, с преобразованием скоростей, моментов, а иногда и видов движения. Для последних характерными являются механизмы для передачи возвратно-поступательного движения во вращательное (двигатель внутреннего сгорания) или наоборот (привод строгального станка).
Передачи винт-гайка предназначены для преобразования вращательного движения в поступательное, в редких случаях (при несамотормозящей винтовой паре) — поступательного во вращательное. Передачи нашли широкое применение в натяжных, нажимных и грузовых устройствах, в механизмах перемещения, подачи и настройки и т. п.
Достоинствами передачи винт-гайка являются простота, компактность и технологичность конструкции; высокая нагрузочная способность и надежность; высокая степень редукции (изменения передаваемых усилий); возможность обеспечения точных плавных перемещений; выполнение самоторможения. К недостаткам передач этого типа следует отнести повышенный износ резьбы, низкий коэффициент полезного действия (для несамотормозящих 0,6...0,8, для самотормозящих менее 0,5).
В зависимости от компоновки передача винт-гайка может быть выполнена по следующим кинематическим схемам:
- винт вращается, гайка перемещается поступательно (натяжное устройство транспортера);
- гайка вращается, винт перемещается поступательно (стопорное устройство, настроечный механизм);
- гайка неподвижна, винт вращается и перемещается поступательно (винтовой пресс для отжима сока, домкрат);
- винт неподвижен, гайка вращается и перемещается поступательно (стол одношпиндельной закаточной машины).
По числу заходов резьбы различают передачи с одно, двух- и многозаходной резьбой. Однозаходные механизмы применяются в домкратах и точных настроечных механизмах. Многозаходные механизмы используются в тех случаях, когда необходимо иметь высокоскоростные перемещения.
Кривошипно-шатунные механизмы предназначаются для преобразования вращательного движения в возвратно-поступательное. Эти механизмы получили широкое распространение — от первых паровых двигателей до современных двигателей внутреннего сгорания.
Механизм копиршток также довольно часто используется для преобразования вращательного движения в поступательное. Достоинством этого механизма является возможность получить от одного вращающегося копира поступательное движение нескольких штоков. Этот механизм является основным узлом закаточных и наполнительных машин в консервной промышленности. В этих же машинах вращательное движение шнека (винта) преобразуется в поступательное движение банок с заданным шагом.
Кривошипно-кулисные механизмы предназначаются для преобразования вращательного движения в колебательное. Частота колебаний и их амплитуда зависят от частоты вращения кривошипа и его геометрических размеров.
Кулачковые передачи или копиры часто используются в машинах, в которых возвратно-поступательное движение рабочего органа должно зависеть от вращения ведущего органа. Закон движения толкателя, задаваемый передаточной функцией, определяется профилем кулачка или копира. Наиболее типичным графиком зависимости между перемещением толкателя и углом поворота кулачка является кривая, которую можно разделить на четыре фазы и соответствующие им фазовые углы поворота кулачка или копира: угол удаления, угол дальнего стояния, угол сближения и угол ближнего стояния.
При силовом замыкании контакта движение толкателя на фазе сближения происходит под действием приложенной силы пружины (или силы тяжести и т. п.), а на фазе удаления — под действием профиля кулачка. На фазе удаления в контакте возникает сила, направленная по нормали к профилю кулачка. Угол между нормалью и направлением движения толкателя называют углом давления. Этот угол является переменной величиной, определяемой профилем кулачка и имеющей знак «плюс» или «минус» в зависимости от расположения нормали относительно вектора скорости толкателя. Его величина определяется размерами механизма, передаточной функцией, равной отношению линейной скорости кулачка к скорости перемещения толкателя.
Проектирование кулачкового механизма разделяется на ряд этапов: выбор закона движения толкателя, разработка структурной схемы механизма, определение основных габаритных размеров, расчет координат профиля кулачков, ориентировочный и уточненный расчет кулачка на контактную прочность, расчет толкателя на контактную прочность и изгиб.
В пищевом машиностроении используются механизмы, которые позволяют в пределах рабочего цикла иметь остановки ведомого звена заданной продолжительности при непрерывном вращении ведущего звена. Такие механизмы называют механизмами с остановками или механизмами с прерывным движением ведомого звена.
Для осуществления такого движения применяются разные механизмы: храповые, мальтийские и др.
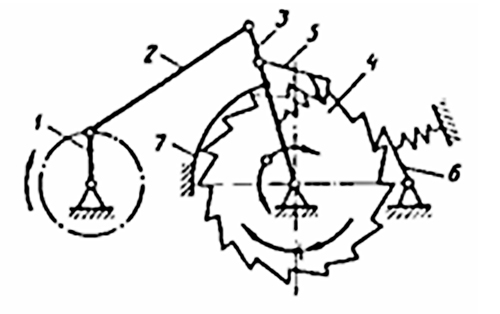
Рис.1. Храповой механизм
Храповой механизм (рис. 1) состоит из храпового колеса 4, с зубьями, в рабочие поверхности которых упираются элементы рабочей 5 и стопорной 6 собачек. Рабочая собачка шарнирно связана с коромыслом 3 четырехзвенного механизма, имеющего кривошип 1 и шатун 2. Плавность хода храпового колеса обеспечивается прижимным щитком 7.
При полном обороте кривошипа шатун и коромысло совершают возвратно-поступательные или качательные движения, вследствие чего рабочая собачка захватывает один или более зубьев храпового колеса и поворачивает его на определенный угол. При возвратном движении рабочей собачки храповое колесо удерживается в неподвижном положении стопорной собачкой.
Основным размерным параметром храповых колес является стандартный модуль по окружности вершин зубьев.
Угол головки рабочей собачки и угол впадины храпового колеса отличаются один от другого на 5°. Конструктивно механизм выполняется таким образом, чтобы наружная поверхность головки рабочей собачки совпадала с плоскостью впадины. Это осуществляется с той целью, чтобы нагрузка при рабочем ходе коромысла равномерно распределялась по площади зуба.
Основным прочностным расчетом храпового механизма является расчет на изгиб зубчатого колеса, осуществляемый по известным формулам расчета зубьев.
Храповые механизмы редко применяют в быстроходных машинах из-за большого уровня шума при их работе и необходимости создания тормозной системы для надежной остановки храпового колеса.
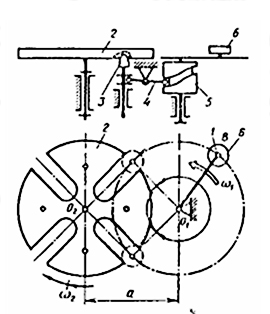
Рис. 2. Мальтийский механизм.
Мальтийский механизм (рис.2) получил широкое распространение благодаря хорошим кинематическим характеристикам и надежному обеспечению заданного времени покоя. Ведомое звено 2 этой передачи выполняется в виде диска или стола, на котором расположено несколько пазов (наиболее часто четыре или шесть). В паз может входить палец-ролик 6, расположенный на ведущем кривошипе 1. Палец входит в паз по касательной к окружности вращения пальца, совпадающей с осью паза. Это осуществляется с целью исключения жесткого удара. В момент входа и выхода пальца из паза положение диска должно фиксироваться. Конструкции фиксаторов могут быть различными. На приведенном рисунке фиксатор 3 получает движение от копира 5 посредством рычага 4.
Коэффициент времени движения мальтийского механизма: .
Коэффициент времени остановки : .
Для двухзаходного диска (z = 2) Кд = 0 и Kо = 1, т. е. такой механизм является неработоспособным, поэтому наименьшее число пазов должно быть равно трем. При увеличении числа пазов эти коэффициенты имеют следующие значения:
Z
|
2
|
3
|
4
|
5
|
6
|
8
|
10
|
Kд
|
0
|
0,167
|
0,25
|
0,3
|
0,33
|
0,375
|
0,4
|
Kо
|
1
|
0,833
|
0,75
|
0,7
|
0,67
|
0,625
|
0,6
|
Эти данные показывают, что если рабочий процесс в машине осуществляется в момент остановки диска, то используется мальтийский механизм с меньшим количеством пазов, что обеспечивает сокращение времени на холостой ход в момент поворота диска. Однако это не является определяющим для выбора числа пазов и связано с тем, что поворот диска происходит неравномерно.
Кинематическим расчетом данного механизма установлено, что кинематическая передаточная функция ε 2/ω 21, равная отношению углового ускорения ведомого звена (диска) к квадрату угловой скорости пальца (кривошипа), достигает максимального значения при наименьшем количестве пазов, где ε 2 определяется из значения угловой скорости ведомого звена ω 2. Если имеется 3 паза, значение этой функции равно 31,44, если, например, 8 пазов, то значение равно 0,7. Это значит, что при малом числе пазов ведомое звено мальтийского механизма имеет плохие динамические характеристики.
При трехпазовом диске значение углового ускорения в 45 раз больше, чем у восьмипазового диска при одинаковой частоте вращения кривошипа. Соответственно возрастают и динамические нагрузки в кинематических пазах.
Оптимальное сочетание требуемого коэффициента времени остановки, коэффициента времени движения и динамических нагрузок выбирают на основе анализа конкретных условий работы передачи. Если нет жестких ограничений коэффициента времени движения, то можно использовать мальтийский механизм с внутренним зацеплением, при котором максимальные ускорения ведомого звена (диска) значительно меньше, чем при наружном, но при этом продолжительность поворота диска всегда больше продолжительности остановки, так как К д > 0,5.
Механизмы передачи вращательного движения.
По принципу действия передачи вращательного движения делятся на передачи трением и передачи зацеплением. К первым относятся ременные (плоскоременные и клиноременные) и фрикционные передачи, ко вторым — цепные, зубчатые, зубчато— ременные и червячные.
Плоскоременные передачи. Ременная передача по сравнению с другими имеет следующие преимущества:
- простота конструкции и меньшая начальная стоимость;
- эластичность привода, смягчающая колебания контура;
- плавность хода и бесшумность работы;
- способность выполнять роль предохранительного звена вследствие проскальзывания при перегрузках;
- несколько пониженная требовательность к точности монтажа (для тихоходных передач);
- простота ухода и обслуживания. Недостатки ременных передач следующие: значительные габариты;
- непостоянство передаточного числа из— за проскальзывания ремня;
- необходимость создания больших сил нормального давления для обеспечения требуемых сил трения между поверхностями ремня и шкива;
- необходимость предупреждения попадания масел на ремни; неприменимость передач во взрывоопасных помещениях вследствие электризации ремней.
По форме поперечного сечения ремня различают передачи: плоскоременные, клиноременные, круглоременные и зубчато-ременные.
Для обычной открытой ременной пары угол обхвата на малом шкиве α10=180°-(D2-D1)/A, где D2 и D1 — диаметры малого и большого шкифов, м; А —межцентровое расстояние, м.
Геометрическая длина ремня (без учета натяга, провисания, соединения концов) L=2A+πm+Δ/A, где m=(D2+D1)/2, Δ=(D2-D1)/2.
Межцентровое расстояние , где λ=L-πm.
В машиностроении применяются в основном четыре вида плоских приводных ремней: кожаные, прорезиненные, хлопчатобумажные и шерстяные.
Кожаные ремни изготовляют из кожи животных, они обладают высокой тяговой способностью, эластичностью и износостойкостью, но и высокой стоимостью.
Прорезиненные ремни представляют собой прочную кордовую провулканизированную техническую ткань в несколько слоев. Резина делает ткань износостойкой. К этому же типу ремней относятся синтетические тканевые ремни из капрона или найлона, пропитанных полиамидными смолами. Эти ремни применяют в быстроходных передачах.
Хлопчатобумажные ремни изготовляют на ткацких станках из хлопчатобумажной ткани с последующей пропиткой азокеритом или битумом.
Шерстяные ремни выполняют из шерстяной пряжи, переплетенной и прошитой хлопчатобумажной пряжей, пропитанной составом из олифы, мела и железного сурика. Нагрузочная способность этих ремней больше, чем хлопчатобумажных, они более стойки к влаге, парам кислот и щелочей, вследствие чего их применяют в химической и пищевой промышленности.
Расчет обыкновенных плоскоременных передач приведен ниже.
Удельное окружное усилие (кг/см), передаваемое единицей ширины ремня: P0=Р0/b, где Р0 — передаваемое окружное усилие, кг; b — ширина ремня, см.
Удельная мощность (л.с./см или кВт/см), передаваемая единицей ширины ремня: N0=P0V/75 или N0=P0V/102, где V — линейная скорость ремня, м/с.
Мощность, передаваемая плоскоременной передачей: N = NоbC, где N0— удельная передаваемая мощность, выбираемая по таблицам в зависимости от типа ремня, его конструктивных особенностей, диаметра меньшего шкива, напряжения ремня и линейной скорости ремня; С — поправочный коэффициент, учитывающий влияние условий работы (вида передачи, скорости ремня, угла обхвата малого шкива и т. д.).
Передаточное число определяется с учетом упругого скольжения. Соотношение между скоростями ремня на ведущем и ведомом шкивах зависит от коэффициента скольжения ремня, поэтому V1 > V2. Отсюда передаточное число , где ω1 — угловая скорость ведущего шкифа; ω2 — угловая скорость ведомого шкифа, D1 и D2 — диаметры ведущего и ведомого шкифов; ε — коэффициент скольжения.
Коэффициент полезного действия (КПД) учитывает неизбежные потери при работе. В ременной передаче происходят потери КПД из-за следующих факторов:
- скольжения ремня на шкивах;
- упругого внутреннего трения между частицами ремня при переменных изгибе, растяжении, сжатии;
- сопротивления воздуха движению ремня, шкивов; трения в опорах.
Для плоскоременных передач среднее значение коэффициента полезного действия обычно принимается равным 0,96-0,98.
Клиноременные передачи. В этих передачах ремни трапецеидального типа работают на шкивах с канавками того же профиля. Благодаря клиновой форме сила сцепления ремня со шкивом при этом же натяжении значительно выше, чем плоского ремня. Это позволяет в клиноременных передачах снизить натяжение ремня и уменьшить нагрузки на опоры при передаче одинаковой мощности.
Клиновые ремни изготовляют преимущественно бесконечными. Для удобства надевания ремней и их смены клиноременные шкивы следует располагать консольно, на концах валов.
Длина клиновых ремней стандартизирована, вследствие чего межцентровое расстояние определяют расчетным путем, исходя из диаметров шкивов и требуемого передаточного отношения. Обычно конструкция клиноременной передачи обеспечивает возможность регулирования межцентрового расстояния с целью изменения натяжения ремней. Шкивы клиноременных передач выполняют из серого чугуна или алюминиевых сплавов.
Геометрические параметры клиноременной передачи определяют по тем же формулам, что и плоскоременной.
Расчет тяговой способности клиноременной передачи заключается в определении числа клиновых ремней z для обеспечения нормальной работоспособности передачи.
, где F1 — передаваемая окружная сила, Н; А0 — площадь поперечного сечения клинового ремня, мм2; [k]n — допускаемое напряжение в ремне, Н/мм2, k2 — коэффициент числа ремней (для двух-трех ремней kz=0,95; четырех-шести ремней kz=0,9; для более чем шести ремней kz=0,85); [z]=8 — наибольшее число клиновых ремней, обеспечивающее равномерность их нагружения в передаче.
При получении по расчету z>[z] необходимо увеличить площадь поперечного сечения ремня, выбрать следующий больший профиль ремня и таким образом снизить число ремней.
При расчете на долговечность действительное число пробегов ремня за 1 с : u=V/L<[u], где V —скорость ремня, м/c; L — расчетная длина, м; [u] — допускаемое число пробегов ремня, меньшее или равное 10.
Мощность, которую может передать клиновой ремень данного сечения: N1=N0С, где С=C1C2 — поправочный коэффициент, учитывающий коэффициент угла обхвата (С1) и коэффициент режима работы (С2); N0 — мощность, передаваемая стандартным ремнем при определенных условиях.
При многоременной клиноременной передаче N = zN1.
При выполнении многоручьевых передач необходимо принимать все меры для обеспечения возможно более равномерного распределения нагрузки между ремнями. С этой целью, надо при обработке в шкивах канавок для ремней следить за тем, чтобы расчетные диаметры всех канавок различались как можно меньше, применяя для этого специальные методы контроля; тщательно подбирать ремни в комплект по длине и по поперечному сечению; при одевании ремней обеспечить равномерное их натяжение.
Фрикционные передачи. Простейшие передачи этого вида состоят из двух колес (ведущего и ведомого), которые прижимаются своими рабочими поверхностями друг к другу с таким усилием, чтобы сила трения, развившаяся в результате этого нажатия, была равна величине передаваемого окружного усилия. Фрикционные передачи применяются для передачи движения между валами с параллельными и пересекающимися осями, превращения вращательного движения в поступательное или наоборот, преобразования вращательного движения в винтовое.
Достоинства этих передач заключаются в простоте тел качения, равномерности передачи движения и бесшумности работы, удобстве регулирования передаточного отношения; недостатки — в больших нагрузках на валы, необходимости прижимных устройств, опасности повреждений при буксовании и неравномерном износе.
Необходимая сила нажатия может быть по величине постоянной или переменной, изменяющейся автоматически в зависимости от величины передаваемого момента.
Классификация фрикционных передач показана на рис. 3. Фрикционные передачи с переменным передаточным числом называются вариаторами.
Основными элементами фрикционных передач являются фрикционные колеса, конструкция которых определяется в основном материалами рабочих поверхностей.
К материалам рабочих органов предъявляются следующие требования:
- высокое значение модуля упругости — для уменьшения упругого скольжения и потерь на перекатывание;
- высокое значение коэффициента трения — для уменьшения требуемой силы нажатия;
- высокая контактная прочность и износостойкость — для обеспечения необходимой долговечности передачи.
Чаще всего в этих передачах используют следующие пары материалов:
- закаленная сталь по закаленной стали;
- чугун по чугуну;
- текстолит или фибра по стали;
- кожа, дерево, резина по стали или чугуну.
Возникающее во фрикционной передаче скольжение вызывает потерю скорости ведомого колеса, а также нагрев и изнашивание рабочих поверхностей. Геометрическое скольжение возникает по длине площадки контакта, вдоль образующих колес и зависит от формы последних. Положение точки, в которой нет скольжения, изменяется с изменением величины передаваемой нагрузки. Поэтому в передачах, работающих с геометрическим скольжением, передаточное число непостоянно. Для того чтобы не происходило геометрического скольжения, в передачах с параллельными валами линия контакта должна быть параллельна валам, а в передачах с пересекающимися валами она должна быть направлена в точку пересечения осей валов. На рис. 3 все передачи, кроме имеющих гладкий обод, работают с геометрическим скольжением в большей или меньшей мере.
Упругое скольжение сопутствует фрикционным передачам с любой формой колес. При передаче момента фрикционной парой элементы поверхности ведущего колеса подходят к начальной точке контакта сжатыми и уходят от конечной точки контакта растянутыми, а ведомого колеса — наоборот. Растяжение элементов поверхности на одном колесе и сжатие их на другом приводят к упругому скольжению. В результате упругого скольжения происходит отставание ведомого колеса от ведущего.
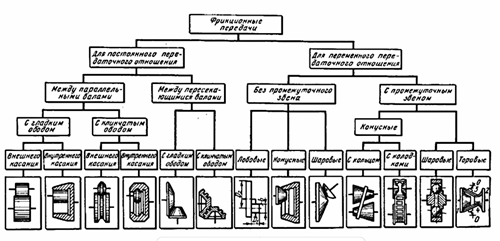
Рис. 3. Классификация фрикционных передач.
Расчет на прочность колес фрикционных передач сводится к определению размеров колес при условии ограничения величины контактных напряжений сжатия.
Контактные напряжения при начальном касании по линии (тела качения — цилиндры, конусы, тела вращения с образующими по форме дуг окружностей одного радиуса)
,
где Q —сила нажатия тел качения, Н; Е — модуль продольной упругости материала при изготовлении тел качения из разных материалов, МПа; E=2E1E2/(E1+E2); b- длина контакта, мм; 1/p — приведенная кривизна, 1/см.
При касании цилиндра с плоскостью 1/ρ=1/R1, при внешнем касании цилиндров 1/ρ = 1/R1 + 1/R2, при внешнем касании конусов и торов 1/ρ = 1/ρ1 + 1/ρ2, при внутреннем касании конусов 1/ρ = 1/ρ1 = 1/ρ2, где Rl и R2 — радиус соприкасаемых цилиндров.
Проверочный расчет цилиндрической фрикционной передачи с металлическими катками проводится по формуле: , где a — межосевое расстояние, мм; Е — модуль упругости, МПа; f — коэффициент трения; M1 —момент на ведущем валу, Н*мм; k — коэффициент запаса сцепления, вводится без предупреждения пробуксовки от перегрузок в период пуска передачи; i>1 — передаточное число; b — рабочая ширина обода катка, мм; [v]k — допускаемое контактное напряжение для менее прочного материала, МПа.
Для конической передачи формула приобретает вид: , где R — среднее, мм.
Расчет фрикционных передач с неметаллическими катками (текстолит, фибра, резина и т. п.) по критерию работоспособности — износостойкости, определяемой нормальной нагрузкой на единицу длины контактных линий:
- для цилиндрических передач
;
- для конических передач
где Dm — средний диаметр ведущего катка, мм.
Значения допускаемой нагрузки (Н/мм) на единицу длины контактной линии [q] для некоторых материалов контактирующих пар (один материал — сталь или чугун) следующие: для фибры 34-39, резины 10-30, кожи 14,5-24,5, для дерева 2,4-4,9.
Общие потери передаваемой мощности во фрикционных передачах складываются из потерь: на трение качения, от проскальзывания, обусловленного масляной пленкой на рабочих поверхностях, от скольжения вследствие неодинакового изменения скоростей по линии контакта.
Потери на трение качения при больших модулях упругости материалов невелики, и в расчетах ими часто пренебрегают. Потери от проскальзывания составляют долю передаваемой мощности, не превышающую относительного скольжения, и составляют 2-3%.
Коэффициент полезного действия передач колеблется в пределах 0,70-0,95.
Цепные передачи. Они состоят из двух колес— звездочек, соединенных цепью. Вращение ведущей звездочки преобразуется во вращение ведомой благодаря сцеплению цепи с зубьями звездочек. Достоинствами цепной передачи по сравнению с ременной являются отсутствие проскальзывания, компактность, меньшие нагрузки на валы и подшипники, постоянство передаточного отношения; недостатками — удлинение цепи вследствие износа ее шарниров и растяжения пластин, шум при работе из-за того, что цепь располагается на звездочке не по окружности, а по многограннику.
Современные цепные передачи могут передавать большие мощности при сравнительно высоких скоростях (до 25-30 м/с). Этот вид передачи выбирают, если применение зубчатой или другой передачи нецелесообразно из-за слишком большого межосевого расстояния. Цепные передачи широко распространены в транспортирующих устройствах (конвейерах, элеваторах, мотоциклах, велосипедах), в приводах машин для производства пищевых продуктов и т. д.
По конструкции приводные цепи делятся на роликовые, втулочные и зубчатые и их размеры стандартизированы.
Роликовые цепи с прямыми пластинами (однорядные и многорядные) изготовляют с диапазоном шагов от 12 до 65 мм.
Многорядные цепи (до шести рядов) способны передавать нагрузку, пропорциональную числу рядов.
Втулочные цепи не имеют ролика. В зацепление с зубьями звездочки входит втулка. Втулочные цепи с шагом 15 мм и больше рекомендуется применять для легких конвейерных и транспортирующих устройств в качестве тяговых цепей. Цепи с шагом менее 10 мм применяют в быстроходных передачах.
Зубчатые (бесшумные) цепи отличаются от приводных цепей других типов более тихой и плавной работой. Звенья зубчатых цепей состоят из набора пластин зубообразной формы, шарнирно соединенных валиками, опирающимися на вкладыши.
Цепи изготовляют на специализированных заводах. Прочностной характеристикой цепей является разрушающее усилие Q. Величина его устанавливается опытным путем на заводе-изготовителе и регламентируется стандартом.
Основными геометрическими параметрами являются ширина цепи и ее шаг. Передаточное число определяется отношением числа зубьев ведущей и ведомой звездочек i=zб/zм, где z — число зубьев звездочки (большой и малой).
Максимальное рекомендуемое передаточное число равно 7. Если i > 7, но не более 10, цепную передачу можно осуществить при условии малой скорости (v ≤ 3 м/с) и постоянства рабочей нагрузки.
Наименьшее допускаемое межцентровое расстояние Amin (мм) определяется в зависимости от передаточного отношения i и диаметров звездочек.
При i ≤ 4 Amin=0,6(Dб+Dм)+(30-50).
Межцентровое расстояние, обеспечивающее благоприятные условия работы, принимается равным А = (30...50)t
Наибольшее расстояние рекомендуется принимать Amax ≤ 80t.
Скорость набегания цепи на звездочку, или средняя окружная скорость звездочки (м/с), v=znt/(60*1000), где z — число зубьев; n — частота вращения; t — шаг цепи, мм.
Допускаемая частота вращения звездочки в зависимости от шага установлена экспериментально. Если принять предельное значение частоты вращения звездочки, то скорость цепи имеет следующие значения: для роликовых цепей vmах ≤ 18 м/с, для зубчатых цепей vmах ≤ 22 м/с.
На работоспособность цепи сильно влияет частота ударов ее звеньев в секунду u=4zn/60L, где L — число звеньев цепи.
Общепринятым методом расчета цепей является подбор их по наибольшему натяжению ведущей ветви (с учетом центробежных сил) с последующей проверкой на износ.
Общее натяжение ведущей ветви цепи (кг)
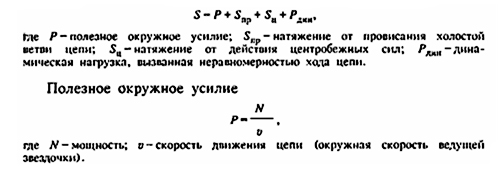
В отличие от ременной в цепной передаче при холостом ходе натяжение в ветвях цепи обусловлено лишь ее провисанием под действием собственной массы.
Величина этого натяжения может быть приближенно определена из условия равновесия цепи:

Величина стрелы провисания f при горизонтальном расположении новой цепи принимается 2-3% от межцентрового расстояния. Натяжение цепи от действия центробежных сил.
Динамическая нагрузка, возникшая вследствие неравномерности движения цепи:
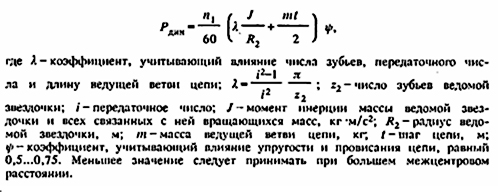
Динамическую нагрузку следует вводить в общее уравнение при скоростях движения цепи более 5 м/с.
Нормальная работа цепной передачи возможна лишь только при наличии смазки в шарнирах цепи и на зубьях звездочек. Периодическое смазывание цепи допускается при скорости ее движения до 4 м/с. При скорости 4-6 м/с рекомендуется через определенные промежутки времени всю цепь погружать в слегка подогретое масло. При скорости 6-8 м/с передача должна быть снабжена кожухом, наполненным маслом. Нижняя ветвь при этом должна быть погружена в масло не более чем на высоту пластины. При скорости более 8 м/с следует непрерывно подавать масло насосом или с помощью специальных разбрызгивающих колес и отражательных щитков.
Приближенное значение коэффициента полезного действия передачи при передаваемой мощности N: η=N/(N+П), где П — потери мощности.
Потери мощности в цепной передаче слагаются из потерь на преодоление жесткости цепи (трение в шарнирах, между пластинами смежных звеньев), на трение между цепью и зубьями звездочек, в опорах валков и сопротивления движению цепи в масле.
Среднее значение коэффициента полезного действия хорошо выполненных передач колеблется от 0,96 до 0,98.
Зубчатые передачи. Эти передачи представляют собой механизмы, которые посредством зубчатого зацепления преобразуют или передают движение, связывают вал с валом или вал с рейкой.
Широкому распространению зубчатых передач способствуют высокий коэффициент полезного действия, компактность, надежность в работе, простота эксплуатации, постоянство передаточного числа. К недостаткам зубчатых передач относятся необходимость специального оборудования для изготовления элементов передачи, шум, возникающий при неточном изготовлении передачи, и значительные потери передаваемой мощности.
По расположению осей зубчатые передачи подразделяются на передачи с параллельными, с пересекающимися, со скрещивающимися осями.
Разновидностью зубчатой передачи является реечная передача, состоящая из сцепляющихся между собой шестерни и рейки и служащая для преобразования вращательного движения в возвратно-поступательное или наоборот.
Работу пары цилиндрических зубчатых колес можно представить как качение без скольжения одного по другому двух снабженных зубьями цилиндров, имеющих общие с зубчатыми колесами оси. Такие воображаемые цилиндры называются начальными цилиндрами, а их основания — начальными окружностями.
Расстояние между одноименными профилями смежных зубьев, измеренное по дуге делительной окружности, называется шагом зацепления.
Длина делительной окружности зубчатого колеса πd=zt, откуда d=zt/π=zm.
Модуль зацепления m является основным параметром зубчатых колес. Величина модуля стандартизирована.
Для обеспечения нормальной работы пары зубчатых колес с постоянным передаточным числом профили зубьев должны быть очерчены по кривым, подчиняющимся определенным законам. Эти, законы вытекают из основной теоремы зацепления, которую можно сформулировать так: общая нормаль к профилям зубьев в точке их касания пересекает межосевую линию в точке, называемой полюсом зацепления и делящей межосевое расстояние на отрезки обратно пропорционально угловым скоростям.
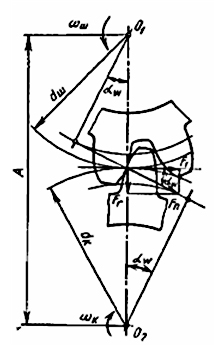
Рис. 4. Элементы зубчатого эволъвентного зацепления и силы, действующие в зацеплении.
Расчет прямозубых зубчатых цилиндрических передач. Рассмотрим силы, действующие в зацеплении пары прямозубых зубчатых колес (рис. 4).
Нормальное усилие Fn (Н) разлагается на две составляющие силы:
- окружную F1— 2MK/dK;
- радиальную Fr — Fntgαw, где Мк — передаваемый крутящий момент; αw — угол зацепления.
Нормальное усилие на зубья
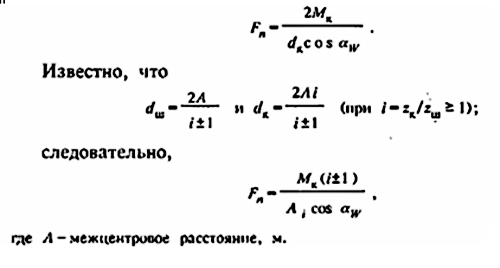
Это усилие используется при расчете зубьев на прочность.
Расчет зуба на прочность проводится при введении некоторых упрощений и допущений: зуб рассматривается как консольная балка прямоугольного сечения, работающая на изгиб и сжатие; вся нагрузка, действующая в зацеплении, передается одной парой зубьев и приложена к их вершинам; нагрузка распределена равномерно по длине зуба.
При расчете зубьев на контактную прочность можно применить результаты исследований на контактную прочность цилиндрических роликов. Это можно осуществить, сделав следующие допущения: зубья рассматривают как два находящихся в контакте цилиндра с параллельными образующими (радиусы этих цилиндров принимают равными радиусам кривизны профилей зубьев в полюсе зацепления); нагрузку считают равномерно распределенной по длине зуба; контактирующие профили предполагают неразделенными масляной пленкой.
Наибольшие нормальные контакты напряжения возникают в точках, лежащих на очень малой глубине под линией контакта:
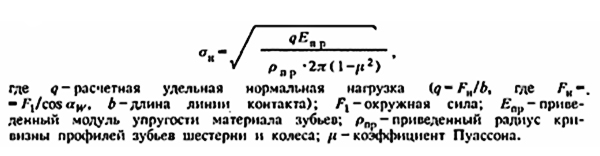
Для учета неравномерности распределения нагрузки по длине контактных линий, а также для учета динамических нагрузок вследствие погрешности изготовления и деформации деталей передачи вводят коэффициент нагрузки К, определяемый по специальным таблицам в зависимости от условий работы, конструкции и точности изготовления передачи:
Расчет косозубых зубчатых перед а ч. Косозубые зубчатые передачи, как и прямозубые, предназначены для передачи момента между параллельными валами. У косозубых колес оси зубьев располагаются не по образующей делительного цилиндра, а по винтовой линии, составляющей с образующей угол β. Угол наклона зубьев β принимают равным 8- 15°, одинаковым для обоих колес, но на одном из сопряженных колес зубья наклонены вправо, а на другом — влево. В прямозубых передачах линии контакта параллельны оси, а в косозубых расположены по диагонали на поверхности зуба. Контакт в косозубых передачах осуществляется сначала в точке, увеличивается до прямой, «диагонально» захватывающей зуб, и постепенно уменьшается до точки.
Достоинства косозубых передач по сравнению с прямозубыми следующие: снижение шума при работе; уменьшение габаритных размеров; высокая плавность зацепления; большая нагрузочная способность; значительное уменьшение дополнительных динамических нагрузок.
Шевронные зубчатые колеса имеют венец, который по ширине состоит из участков с правыми и левыми зубьями. При этом зацеплении осевые усилия, возникающие на каждой половинке венца, взаимно уничтожаются и на подшипник не передаются. Ввиду сложности изготовления шевронные колеса применяют редко, только в тех случаях, когда требуется передавать большую мощность и высокую скорость, а осевые нагрузки нежелательны.
По аналогии с расчетом прямозубых цилиндрических передач проводится расчет и косозубых передач, но при этом вводятся специальные поправочные коэффициенты, учитывающие перекрытие зубьев, угол наклона зуба, распределение нагрузки между зубьями. Расчет на контактную прочность косозубых и шевронных колес проводят аналогично расчету прямозубых колес.
Расположение зубьев в косозубом зацеплении повышает коэффициент перекрытия зубьев, так как в зацеплении находится одновременно несколько пар зубьев, что уменьшает нагрузку на один зуб, повышает контактную прочность, увеличивает прочность зуба на изгиб, уменьшает динамические нагрузки. Для учета повышения контактной прочности косых зубьев по сравнению с прямыми в формулу расчета напряжений вводят поправочные коэффициенты, учитывающие распределение нагрузки между зубьями и зависящие от степени точности передачи и окружной скорости.
Расчет конических зубчатых передач. Зубчатую передачу с пересекающимися осями, у которой начальные и делительные поверхности колес конические, называют конической. Основные исходные положения, принятые при расчете цилиндрических передач, распространяются на конические передачи.
Опытным путем установлено, что нагрузочная способность конической передачи ниже, чем цилиндрической. В соответствии с этим в расчетные формулы для зубьев конической передачи вводят коэффициент, учитывающий снижение их нагрузочной способности по сравнению с зубьями цилиндрических передач.
Прочность зубьев при изгибе рассчитывают по среднему значению модуля их. Коэффициент формы зуба выбирают по аналогии с цилиндрической прямозубой передачей, но в зависимости от числа зубьев эквивалентных колес zк = z/cosδ, где δ — угол делительного конуса.
Расчет конической передачи на контактную прочность основан на допущении, что нагрузочная способность ее равна нагрузочной способности эквивалентной цилиндрической передачи при ширине колес последней, равной ширине конических колес.
На основании этого используются формулы расчета цилиндрических колес при замене А, i и Мк соответственно на Aэ, iэ и Мкэ.
Крутящий момент между скрещивающимися валами передается с помощью винтовых, гипоидных, червячных и глобоидных передач, являющихся разновидностями зубчатой передачи. Теоретически угол скрещивания валов может быть любой, но практически чаще всего он равен 90°.
Винтовые передачи. Простейшей парой такого вида является винтовая передача. Цилиндрические винтовые колеса по своей конструкции не отличаются от косозубых цилиндрических колес. Контакт зубьев в зацеплении винтовых цилиндрических колес происходит теоретически в одной точке, тогда как у косозубых колес — по линии. Поэтому винтовые передачи следует применять при небольших окружных скоростях и малых нагрузках.
Так как винтовые передачи образуются из косозубых колес, то для нахождения размеров винтовых передач пригодны формулы, определяющие размеры цилиндрических косозубых колес.
Межосевое расстояние А, определяющее габариты передачи, приближенно будет

Для определения усилий в винтовой передаче следует пользоваться формулами, аналогичными для косозубых цилиндрических. При угле скрещивания δ = 90° радиальное усилие для обоих колес будет одинаковым, осевое усилие на шестерне будет равно окружному усилию на колесе и наоборот.
Обычно винтовые передачи рассчитывают по эмпирической формуле, определяющей максимальное усилие в нормальном к зубьям направлении по условию предупреждения заедания.
Условное напряжение, kb
|
Материалы
колес
|
при непродолжительной
притирке в паре
|
при тщательной
притирке в паре
|
Сталь - бронза
|
0,35
|
0,84 |
Сталь - сталь
|
0,4
|
1,05
|
Чугун - чугун (бронза)
|
0,55
|
1,4
|
Текстолит - чугун (сталь) |
0,7
|
1,75
|
Расчет зубьев на изгиб можно проводить по формулам для косозубых цилиндрических пар.
Гипоидные передачи. Они получили широкое распространение. Колеса таких передач конические с косыми либо криволинейными зубьями. Для правильного зацепления нормальный модуль зубьев на колесе и шестерне должен быть одинаков. Углы наклона зубьев на шестерне и колесе различны. Из-за разных углов наклона зубьев на колесе и шестерне при изменении направления вращения изменяется угол, зацепления.
Размер смещения осей Е с целью предупреждения заедания обычно регламентируется в следующих пределах: от 0,33 dк (при i=1) до 0,20 dк (при i>2,5).
Силы, действующие в гипоидной передаче, можно определить, воспользовавшись преобразованными формулами для конических передач, где вместо угла β ввести для шестерни βш, для колеса βк; вместо окружного усилия Р ввести для колеса Рк и для шестерни Рш, так как последние не равны между собой вследствие βш ≠ βк
Особенностью гипоидных передач является скольжение в зацеплении не только по высоте, но и вдоль зубьев, что способствует лучшей их приработке и уменьшению шума.
Достоинства гипоидной передачи по сравнению с конической заключаются в том, что при тех же габаритах шестерне гипоидной передачи может быть выполнена больших размеров. Недостатки заключаются в сложности изготовления и возможности заедания зубьев вследствие продольного скольжения.
Червячные передачи. Эти передачи относятся к категории зубчато-винтовых. Ведущим элементом этой пары является червяк.
Червячную передачу, у которой делительные и начальные поверхности червяка и колеса цилиндрические, называют цилиндрической червячной передачей.
В сечении главной плоскостью, проходящей через ось червяка, перпендикулярно оси колеса, зацепление можно рассматривать как зацепление эвольвентного червячного колеса с непрерывной совокупностью реек, профиль зубьев которых совпадает с профилем витка червяка.
На основании того, что червячную передачу можно представить как разновидность винтовой зубчатой передачи с углом скрещивания валов 90°, геометрические размеры червячной передачи можно найти, воспользовавшись формулами для зубчатых колес.
Осевой шаг червяка t s равен расстоянию между одноименными профильными поверхностями смежных витков, измеренному вдоль оси червяка.
Ход винтовой линии витков червяка
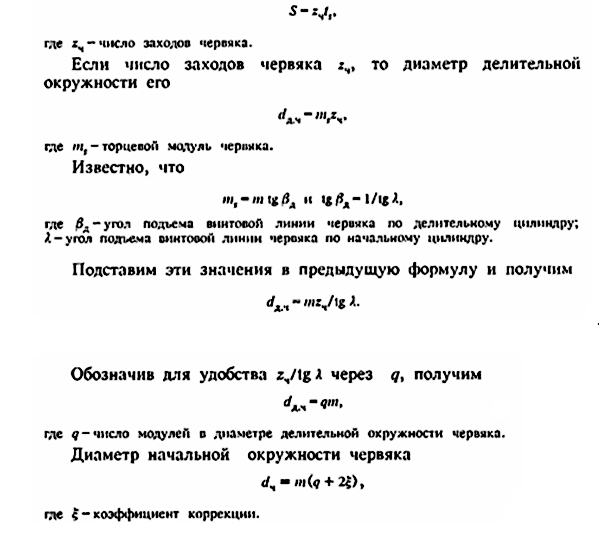
При отсутствии коррекции начальный и делительный диаметры совпадают.
Межосевое расстояние А равно сумме радиусов начальных цилиндров червяка и червячного колеса. Диаметр делительной (начальной) окружности колеса dдк = dк = zкms.
Значения коэффициента коррекции стандартизированы и могут иметь значения -1; -0,5; 0; 0,5; 1.
Силы, действующие в передаче, можно определить на основании тех же зависимостей, которые даны для зубчатых передач.
Воспользовавшись этими формулами и учитывая, что угол наклона зубьев на червячном колесе βк равен углу подъема витков на червяке λ, получим окружное усилие на колесе Рк, равное осевому усилию на червяке Ром при крутящем моменте на колесе Мк Рк=2Мк/dk=Pom.
Осевое усилие на колесе Ро.к равно окружному усилию на червяке Рч с учетом того, что скольжение вдоль зубьев вызывает силу трения.
Коэффициент полезного действия червячной передачи: η=η1η2η3 где η1,η2,η3 — коэффициенты, учитывающие потери в зацеплении, в подшипниках и на размешивание и разбрызгивание масла соответственно.
Потери в зацеплении в основном обусловлены скольжением витков червяка относительно зубьев. Коэффициент потерь η=λ-tgλ/tg(λ+p), где р — угол трения, зависящий от материалов сопряженной пары, качества поверхности, смазки и скорости скольжения.
Потери на перемешивание и разбрызгивание масла зависят от окружной скорости колеса, ширины его и условной вязкости масла.
Для приближенных расчетов полный коэффициент полезного действия червячных передач можно принять равным (с учетом КПД в подшипниках): для однозаходных червяков η = 0,7-0,75; для двухзаходных червяков η = 0,75.. .0,82; для трех-четырехзаходных червяков η = 0,82-0,92.
Глобоидные передачи. Это такие червячные передачи, начальная поверхность которых представляет собой поверхность глобоида (тора).
Для геометрического расчета зацепления глобоидной передачи исходными обычно являются величины i и A, причем i должно соответствовать техническому заданию, а A определяется расчетом.
Расчет передачи на износ производится методом последовательного приближения по эмпирической формуле, определяющей допускаемую мощность на червяке
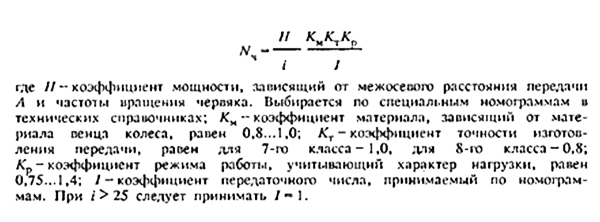
После расчета и уточнения межосевого расстояния и выбора коэффициента qч определяют модуль передачи (мм) m— 2A/(zк + qч).
Модуль глобоидных передач стандартом не установлен и может быть дробным.
Коэффициент qч = dдч/m принимают от 8 до 12 для обеспечения достаточной жесткости тела червяка, прогиб червяка под нагрузкой не должен превышать f = 0,2 ΔA (ΔА — предельное отклонение межосевого расстояния передачи).
Расчет коэффициента полезного действия глобоидных передач следует проводить так же, как и для передач с цилиндрическим червяком. Коэффициент полезного действия для глобоидных передач равен 0,82-0,9.
Направляющие вращательного движения.
Одними из основных деталей передачи являются валы и оси.
Деталь, на которую насажены вращающиеся части машины, реально осуществляющие геометрическую ось вращения, называется валом или осью.
Вал — это вращающаяся в опорах деталь, предназначенная для передачи крутящего момента, ось— деталь, поддерживающая вращающие части машины. В отличие от валов оси не передают крутящего момента.
По форме геометрической оси различают прямые и коленчатые валы. Особую группу составляют валы с криволинейной или изменяющейся формой геометрической оси — гибкие проволочные или тросовые валы. Опорные участки валов и осей называются цапфами.
Расчет валов и осей на прочность. Для расчета прежде всего составляют расчетную схему. При этом валы и оси рассматривают как балки на шарнирных опорах. В машинах наиболее часто вал нагружен одновременно крутящим Мк и изгибающим Ми моментами. Иногда валы могут быть нагружены сжимающей или растягивающей силой.
Расчет валов на кручение. При этом ориентировочном расчете обычно определяют диаметр выходного конца вала или диаметр вала под опорой, который испытывает только кручение.
Уравнение прочности на кручение вала имеет вид

Общий приближенный расчет вала. Если на вал действуют нагрузки, лежащие в различных плоскостях, их следует разложить на составляющие в двух взаимно перпендикулярных плоскостях, общих для всех нагрузок, после чего по закономерностям, известным из курса «Сопротивление материалов», определяют эпюрные реакции.
Имея эпюры изгибающих и крутящих моментов, можно определить для составляющих сечений значения эквивалентного, или приведенного, момента.
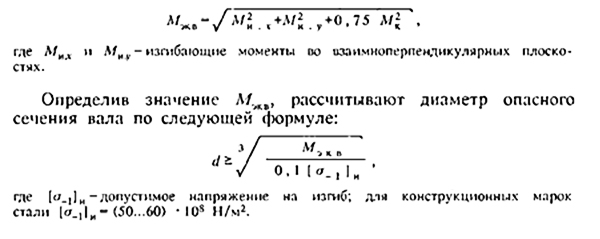
Приближенный расчет вала отнюдь не обязателен. Если в качестве завершающего этапа намечено провести уточненный расчет, то следует ограничиться ориентировочным, а после конструктивного оформления вала провести уточненный. Последний проводят как проверочный. Он служит для определения расчетного коэффициента запаса прочности для опасного сечения вала.
Общий коэффициент запаса прочности
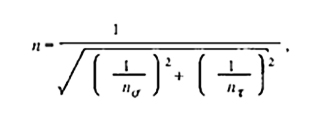
где пσ — коэффициент запаса прочности по нормальным напряжениям при изгибе вала, зависящим от предела выносливости материала вала при симметричном цикле изгиба σ — 1, эффективного коэффициента концентрации нормальных напряжений Кσ, масштабного фактора для нормальных напряжений, амплитуды цикла нормальных напряжений σv, среднего напряжения цикла нормальных напряжений σт и коэффициента ψσ, зависящего от соотношения пределов выносливости при симметричном и нулевом циклах изменения напряжения; nτ — коэффициент запаса прочности по касательным напряжениям, зависящим от аналогичных коэффициентов при кручении вала.
Допускаемый общий запас прочности в опасных сечениях вала, вычисленный по вышеприведенному уравнению, обычно находится в пределах 1,3-2,5.
Учитывая повышенные требования к жесткости валов, рекомендуется иметь значения коэффициента запаса прочности 2,5-3,0. Если по расчету получены такие значения n, то дополнительного расчета вала на жесткость не требуется.
Во многих случаях при конструировании вала не очевидно, какое сечение является опасным, поэтому коэффициент запаса прочности определяют для нескольких сечений. Опасным является то сечение, для которого коэффициент запаса прочности имеет наименьшее значение, при этом оно не может совпадать с сечением, где возникают максимальный изгибающий и крутящий моменты.
Оси (так как они не испытывают кручения) рассчитывают только на изгиб.
По конструкции проектируемого узла с осью составляют расчетную схему, определяют силы, действующие на ось, строят эпюры изгибающих моментов. Диаметр оси
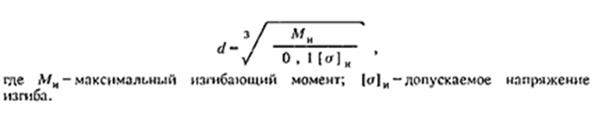
Односторонние закрепленные оси рассчитывают как балки, защемленные одним концом. Короткие оси часто выполняют постоянного сечения по всей длине. Длинным осям стараются придать форму, близкую к форме тела равного сопротивления изгибу. Вследствие того, что диаметры сечений тела равного сопротивления изгибу изменяются по параболическому закону, а тело имеет вид параболоида вращения, то ось конструируют так, чтобы она вписывалась в это тело, т. е. ось выполняется конусом с диаметром, уменьшающимся от центра к опорам (в случае симметричной оси, защемленной в двух опорах).
Расчет цапф (шипов, шеек, пят). Участки вала или оси, охватываемые опорами, называются цапфами. Концевые цапфы, передающие радиальные нагрузки, называются шипами, а промежуточные — шейками; цапфы, передающие осевые нагрузки,— пятами.
Шипы и шейки рассчитывают на прочность, на износостойкость по величине удельного давления и на нагрев. Для упрощения расчетов удельное давление по опорной поверхности шипа принимают равномерно распределенным.
При расчете на прочность шип рассматривают как консольную балку, закрепленную в теле вала и нагруженную сплошной равномерной нагрузкой, равной реакции опоры на вал.
Уравнение прочности цилиндрического шипа имеет вид

Допускаемое напряжение изгиба для шипа выбирают так же, как и для валов. Расчет шипов и шеек на удельное давление производят по уравнению P = [p]ld, где [р] — допускаемое удельное давление, Н/м2. Величину [p] выбирают в зависимости от условий работы, материала вкладышей и степени чистоты поверхности трения.
Из расчетных уравнений шипов на изгиб и по удельному давлению получим .
Обычно ψ = 0,6-1,5. При значениях ψ >1,5 применяют самоустанавливающиеся опоры.
Расчет шипов и шеек на нагрев производят при окружной скорости v > 0,5 м/с по уравнению
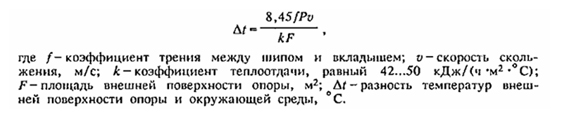
Пяты рассчитывают на прочность, на удельное давление и на нагрев.
Сплошная плоская пята опирается на подпятник плоской торцевой поверхностью, имеющей форму сплошного круга.
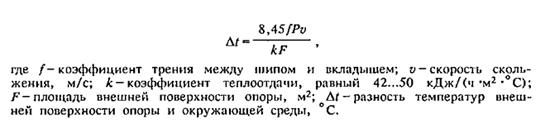
Экспериментальные данные показали, что давление распре¬делено по площади пяты неравномерно, причем в центральной части оно наибольшее, что приводит к выдавливанию смазки. По этой причине удаляют центральную зону и получают кольцевую пяту. Она изнашивается более равномерно вследствие меньшей разности скоростей разноудаленных от оси участков поверхности.
Сплошную плоскую и кольцевую пяты, нагруженные только осевыми нагрузками, рассчитывать на прочность не следует, так как допускаемое напряжение на сжатие [σ]сж значительно больше, чем величина допускаемого удельного давления.
Другим видом кольцевой пяты является гребенчатая, имеющая ряд кольцевых выступов — гребней, которыми она передает осевую нагрузку вала на соответствующие поверхности подпятника.
Применение гребней позволяет получать небольшие удельные давления при значительных осевых нагрузках, однако распре¬деление усилия между гребнями крайне неравномерно, что объясняется неточностью изготовления, деформацией самих гребней и участков пяты и подпятника между ними, влиянием температурных факторов.
У гребенчатой пяты рассчитывают на прочность гребень. Для расчетов обычно принимают h = b, где hub соответственно толщина и высота гребня.
Гребень рассматривают как балку с защемленным концом, нагруженную равномерно распределенной нагрузкой P/z, где z — число гребней.
Уравнение прочности гребня будет Pb/2z=πd1h2[σ]n/6, где d — диаметр вала в метрах.
Принимая, что b = (0,1 ±0,3) d1, из приведенного уравнения можно определить число гребней пяты.
Расстояние между гребнями пяты определяют из аналогичного расчета на прочность выступов подпятника, входящих во впадины между гребнями пяты.
Расчет пяты по удельному давлению проводят из предположения равномерного распределения нагрузки на опорной поверхности.
Диаметр сплошной пяты находят из уравнения P=πd2[p]ψ/4, где ψ — коэффициент, учитывающий уменьшение рабочей поверхности за счет смазочных канавок.
Диаметр кольцевой пяты определяется из аналогичного уравнения
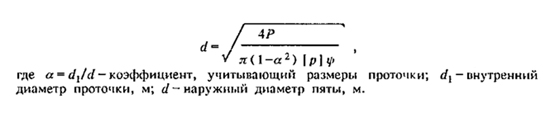
Обычно принимают α = 0,4-0,6.
Число гребней гребенчатой пяты из условия ограничения удельного давления можно получить
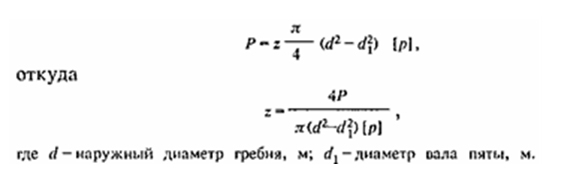
Расчет и выбор опор валов. При проектировании узла вал-подшипник перед конструктором стоит задача выбора опоры: скольжения или качения.
Опоры валов или осей, в которых поверхность цапфы скользит по охватывающей ее поверхности опоры, называются подшипниками скольжения.
Подшипники скольжения имеют следующие достоинства: простота конструкции, возможность применения их при любой частоте вращения; относительно небольшие радиальные размеры; возможность разъема, обеспечивающего легкую сборку и пригонку трущихся поверхностей. Недостатками этих подшипников являются увеличение сопротивления трения в периоды пуска и остановки; большой расход смазки; трудность защиты трущихся поверхностей от загрязнений; сравнительно большие размеры в осевом направлении.
Основные элементы подшипника скольжения — корпус, вкладыш, крышка, смазочное приспособление.
При недостаточной смазке, малой скорости скольжения и большой удельной нагрузке подшипники скольжения работают в области граничного и сухого трения, при этом коэффициент трения наибольший, величина его постоянная.
Основными критериями работоспособности подшипника скольжения являются:
- среднее давление ρ = P/F, где F — проекция опорной поверхности на плоскость, перпендикулярную к вектору нагрузки Р;
- произведение pv, где v — окружная скорость шипа.
Таким образом, при элементарном расчете опор скольжения должны быть удовлетворены два условия:
- ограничение среднего давления во избежание интенсивного износа p = P/F≤ [р];
- ограничение произведения pv во избежание интенсивного нагрева pv ≤ [pv].
Значения допускаемых величин [р] и [pv] приведены в табл. 2.
Значения допускаемых величин [р] и [pv]
|
Тип машины |
[р], Н/мм2 |
[pv],Н•м/ (мм2 •с) |
Редукторы общего назначения
|
2-6 |
4-8 |
Редукторы тяжелого типа |
6-12 |
6-20 |
Трансмиссии |
1-4 |
3-8 |
Конвейеры ленточные и цепные
|
2-5 |
2-8 |
Обычно при конструировании опор задаются диаметром d и, принимая ширину вкладыша, равную (0,5-1) d, производят поверочный расчет с определением значений р и pv. Если в результате получено р > [p] или pv > [pv], то соответственно изменяют р и d.
Удлинение срока службы опор скольжения достигается конструктивными, технологическими и эксплуатационными мероприятиями.
Специальные конструктивные меры изыскиваются в каждом конкретном случае. Например, необходимо учесть те факторы, которые не учитываются расчетными формулами, но оказывают существенное влияние на работу опор при любом виде трения скольжения. К числу этих факторов относятся: правильное расположение и необходимые размеры смазочных канавок; рациональный выбор смазочного устройства; хорошие условия тепло— отвода; высокая жесткость всего опорного узла. Недостаточная жесткость узла приводит к искажению форм и размеров опоры, а соответственно к ухудшению условий смазки.
Технологические меры удлинения срока службы опорного узла сводятся в основном к точному выполнению заданных чертежами конструктивных форм и размеров деталей, чистоте обработки, точности сборки.
К эксплуатационным мерам относится строгое соблюдение условий работы, заданных технологическим регламентом; необходимо правильно осуществить процесс приработки опоры, а также следить за надежностью смазки или при жидком масле контролировать тщательность его фильтрации.
Подшипники качения по сравнению с опорами скольжения обладают ряда преимуществ, обеспечивающих их широкое применение: незначительные потери от трения, малый расход смазочных материалов, небольшие габариты по длине. В связи с тем что у этих подшипников практически отсутствует зависимость потерь от скорости вращения, коэффициент полезного действия узла на всех режимах практически одинаков, что обусловливает меньшую затрату мощности двигателя в период разгона рабочего органа.
К недостаткам подшипников качения относятся сравнительно большие габариты по диаметру, отсутствие разъема, что усложняет монтаж подшипникового узла.
В зависимости от формы тел качения подшипники делятся на шариковые, роликовые и игольчатые; в зависимости от направления воспринимаемой нагрузки — на радиальные, упорные и радиально-упорные.
При проектировании подшипники качения не рассчитывают, а подбирают по каталогу в зависимости от диаметра цапфы вала, величины, направления и характера нагрузки, угловой скорости вращающегося кольца, требуемой долговечности.
В зависимости от частоты вращения колес подшипников их подбирают либо по статической, либо по динамической грузоподъемности. Если подшипник воспринимает нагрузку в неподвижном состоянии или его вращающееся кольцо имеет частоту вращения не более 1 об/мин, то подшипник выбирают по статической грузоподъемности без проверки его на долговечность.
Динамической грузоподъемностью называется нагрузка (радиальная для радиальных и радиально-упорных подшипников, осевая для упорных), которую подшипник может выдержать в течение миллиона оборотов без усталостного разрушения поверхностей тел качения или беговых дорожек колец.
Условие для выбора подшипников качения: С<[C], где С — требуемая динамическая грузоподъемность, Н; [С] — табличное значение грузоподъемности подшипника выбранного размера.
Выбирают подшипники качения по приведенной нагрузке Р и расчетному ресурсу L (млн об.):
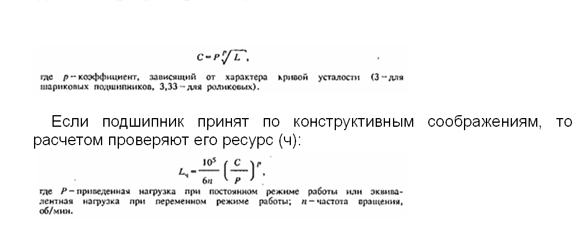
Подшипники качения выходят из строя по разным причинам. Часто в них повреждаются сепараторы, реже — рабочие поверхности колец и тел качения.
При отсутствии смазки и большом давлении тел качения на сепаратор, а также при неправильной сборке может произойти заедание тел качения, что приведет к их поломке. Очень часто подшипники качения выходят из строя вследствие усталостного выкрашивания рабочих поверхностей.
С целью увеличения надежности подшипникового узла тела качения в нем не должны подвергаться защемлению при радиальном нагружении, при этом следует предусматривать достаточный тепловой зазор между торцом подшипника и упорной крышкой.
К числу эксплуатационных мер, способствующих увеличению срока службы подшипников, относятся обеспечение надежной защиты от попадания пыли, влаги, кислот, щелочей, своевременное их смазывание; соблюдение скоростного и силового режимов работы подшипников; обеспечение условий правильной сборки подшипникового узла.
Кольца подшипников должны быть смонтированы на валу и в корпусе с определенными посадками. Посадочные места на валу под внутренние кольца обрабатывают по системе отверстия, обработку корпуса под наружное кольцо осуществляют по системе вала.
При выборе посадок необходимо обеспечить неподвижное соединение того кольца подшипника, которое последовательно воспринимает нагрузку по всей окружности дорожки качения (вращающееся); второе же кольцо, подвергающееся местному нагружению, устанавливают по скользящей посадке.
Краткие сведения о редукторах.
Редуктором называется механизм, обеспечивающий передачу энергии от двигателя к рабочему или промежуточному органу машины с понижением угловой скорости (частоты вращения) валов с повышением крутящего момента. Аналогичные конструкции, предназначенные для повышения частоты вращения, называются мультипликаторами.
Редуктор состоит из литого или сварного корпуса, в котором размещены элементы передачи — зубчатые колеса, валы, подшипники и т. д. Разновидностей редуктора чрезвычайно много.
В основу классификации положены следующие признаки:
- тип передачи:
- зубчатые;
- червячные;
- смешанные;
- планетарные;
- число ступеней;
- тип зубчатых колес:
- цилиндрические;
- конические;
- смешанные;
- другие;
- относительное расположение валов в пространстве:
- вертикальные;
- горизонтальные;
- особенность кинематической схемы
- соосное расположение валов;
- раздвоенная ступень;
- другое.
Одноступенчатые цилиндрические редукторы. Передаточное число одноступенчатого редуктора обычно меньше или равно 5. Наиболее простым, редко встречающимся, предназначенным для изменения только направления вращения валов является редуктор с передаточным отношением, равным 1. Он применяется в тех случаях, когда нельзя использовать открытые передачи.
Вид зубьев цилиндрической передачи может быть любой (прямой, косой, шевронный), выбирают его в зависимости от передаваемых усилий и возможных габаритов редуктора.
Выбор горизонтальной или вертикальной схемы расположения валов определяется конструктивной компоновкой привода. Валы могут монтироваться как на подшипниках качения, так и на подшипниках скольжения. Последние используются в тяжелых редукторах при малых скоростях вращения валов.
Одноступенчатые конические редукторы. Передаточное число редуктора при использовании прямозубых конических колес обычно не превышает 3,0, при использовании колес с косыми или криволинейными зубьями — не более 5,0. Валы в конических редукторах монтируют на подшипниках качения.
Конические редукторы можно выполнить с различным пространственным расположением тихоходного и быстроходного валов. При вертикальном расположении быстроходного вала привод должен осуществляться от фланцевого электродвигателя.
Двухступенчатые и трехступенчатые цилиндрические редукторы. Они являются наиболее распространенными. Применение соосной схемы быстроходного и тихоходного валов позволяет сократить габариты редуктора. Вид зубьев передачи может быть разнообразным, при этом с целью снятия осевых усилий при использовании косозубых колес обычно направления зубьев на первой и второй ступенях различны.
Соосное расположение вала при указанном выше достоинстве имеет и недостатки: необходимость одинакового межосевого расстояния для первой и второй ступени, что приводит к недогруженное™ быстроходной ступени; затруднена смазка подшипников, находящихся в средней части корпуса; большое расстояние между опорами промежуточного вала, возможность только одного входного и выходного концов вала. Последний недостаток можно исключить, использовав раздвоенную схему по быстроходной или тихоходной ступени.
В редукторах с раздвоенной быстроходной или тихоходной ступенью зубчатые колеса расположены симметрично относительно опор. Кроме того, следует иметь в виду, что в опасном сечении промежуточного вала возникает крутящий момент, соответствующий половине передаваемой мощности. Это обстоятельство относится к достоинствам редукторов с раздвоенной ступенью.
Двухступенчатые редукторы обычно имеют передаточное число 8-30, трехступенчатые — до 400.
Коническо-цилиндрические редукторы. Обычно коническо-цилиндрические редукторы выпускают с вертикальным расположением ведущего вала первой конической ступени. Такая конструкция удобна для привода от фланцевого электродвигателя, устанавливаемого непосредственно на корпусе редуктора.
Коническая ступень может иметь прямые, косые или криволинейные зубья.
Нормальный диапазон передаточных чисел для этого типа редукторов 8- 15.
Трехступенчатые редукторы с одной конической и двумя цилиндрическими передачами могут иметь l=25-75, при этом цилиндрические ступени могут быть развернутыми либо соосными.
Червячные редукторы. Они различаются по относительному расположению червяка: с верхним, нижним и боковым расположением.
В редукторах с нижним расположением червяка улучшаются условия смазки червячной пары, однако имеется большая вероятность попаданаия в зацепление металлических частиц — продуктов износа венца колеса и зубьев червяка. При верхнем расположении червяка этот недостаток может быть исключен.
Передаточное число червячных редукторов 8-80.
Зубчато-червячные, червячно-зубчатые и двухступенчатые червячные редукторы. Их применяют для получения больших передаточных чисел (до 150), особенно при конструировании подъемно-транспортных машин. В отдельных случаях передаточное число может быть 250.
Передаточное число двухступенчатых червячных редукторов 80-2500, наиболее часто 400.
Мотор-редуктор представляет собой отдельный агрегат, состоящий из электродвигателя и редуктора того или иного вида. Встроенные зубчатые передачи могут быть с одной или двумя ступенями. Обычно применяются передачи в виде цилиндрических зубчатых пар, реже используются червячные.
Планетарные редукторы. Они предназначены для получения больших передаточных чисел при малых габаритах передачи.
В общем виде редуктор имеет:
- сателлиты, т. е. колеса, совершающие сложные движения и имеющие подвижную ось вращения;
- водило — подвижное звено, на котором укреплены оси сателлитов;
- сателлиты находятся обычно в зацеплении с центральными колесами, вращающимися вокруг оси механизма или закрепленными неподвижно.
Число сателлитов зависит от возможности их размещения в редукторе, но с целью равномерного распределения нагрузок предпочтительно иметь три сателлита.
Передаточное отношение планетарной передачи обозначается буквой i с двумя индексами: внизу двойной индекс, определяющий отношение угловых скоростей рассматриваемых звеньев, вверху индекс, указывающий, какое звено механизма принято неподвижным.
На рис. 5 показана дифференциальная планетарная передача.
Угловые скорости зубчатых колес 1 (А), 2, 3 (п) и водила Я обозначают соответственно o)v w2, и wH. Относительное движение не изменяется, если всей передаче сообщить дополнительное вращение со скоростью равной по величине, но противоположной по направлению вращения водила.
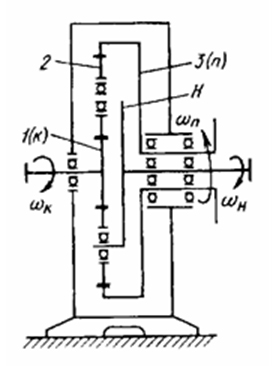
Рис. 5. Дифференциальная планетарная передача (планетарный редуктор).
Если в этой же передаче жестко закрепить колесо 3, то получим простую планетарную передачу, где w3 = 0. При проектировании планетарных редукторов следует соблюдать три условия:
- В передачах, выполненных без смещения исходного контура, число зубьев сателлита выбирают из условия соосности валов центральных колес: z2 — среднее между z1и z3. В передачах со смещением исходного контура условие соосности проверяют равенством межосевых расстояний колес, составляющих передачу: Лх_2 = Л2_3, где Л2_3 — межосевое расстояние между сателлитом 2 и корончатым колесом 3; межосевое расстояние между солнечным колесом 1 и сателлитом 2.
- Из условия возможности сборки передачи сумма чисел зубьев колес 3 (корончатого) и 1 (солнечного) должна быть кратна числу сателлитов: (z3+z1)/u=y, где u - число сателитов.
- Чтобы соседние сателлиты не задевали зубьями друг друга, должно соблюдаться условие соседства
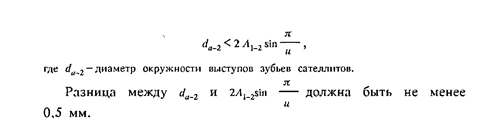
Неизбежные неточности при изготовлении передач приводят к неравномерному распределению нагрузки между сателлитами, что снижает нагрузочную способность редуктора. Для выравнивания нагрузки по сателлитам применяют три принципиально различных способа:
- первый — жесткое крепление всех деталей, высокая точность выполнения всех размеров, очень тщательный монтаж, подбор сателлитов по зазору в зацеплениях с центральными колесами;
- второй — одно из установленных центральных колес или во¬дило плавающее;
- третий — установка центральных колес с гибким ободом или ввод упругой связи между венцами сдвоенных сателлитов.
Наибольшее распространение получили конструкции с плавающими центральными колесами.
Муфты.
Передача вращательного движения и крутящего момента с одного вала на другой при их соосном положении осуществляется посредством муфт. Кроме того, муфты приводов выполняют и другие важные функции: компенсацию небольших монтажных отклонений, разъединение валов при перегрузках, автоматическое управление, бесступенчатое регулирование пере даточного отношения, предохранение машин от поломок при аварийном режиме.
Различные способы передачи вращательного момента, различные функции, выполняемые муфтами, обусловили большой типаж конструкций современных муфт.
Передача момента в муфте может осуществляться механической связью между деталями, выполненными в виде неподвижных соединений или кинематических пар (муфты с геометрическим замыканием; силами трения или магнитного притяжения (муфты с силовым замыканием); силами инерции или индуктивным взаимодействием электромагнитных полей (муфты с динамическим замыканием).
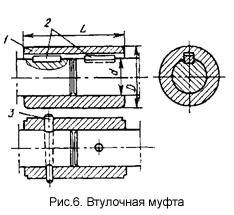
По характеру работы и основному назначению муфты могут быть различных типов.
Постоянные соединительные муфты. Они выполняются с геометрическим замыканием. Жесткие некомпенсирующие (или глухие) муфты соединяют валы без возможности относительного их перемещения.
Однако в реальных условиях не всегда удается обеспечить соосность: под действием тепловых и силовых факторов возникают определенные деформации, приводящие к смещению валов — осевому, радиальному и угловому. Для устранения вредных последствий таких смещений выбирают жесткие компенсирующие муфты.
Простейшей жесткой муфтой является втулочная муфта (рис. 6). Она представляет собой втулку 1, посаженную с помощью шпонок 2, штифтов 3 или шлицев на выходные концы валов. Другим видом жестких муфт являются фланцевые, их иногда называют поперечно-свертными. Фланцевые муфты могут передавать значительные вращающие моменты.
Продольно-свертная муфта (рис. 7) отличается от фланцевой тем, что линия разъема полумуфт, выполненных в виде разрезной втулки, располагается вдоль оси валов.
Вращающий момент передается с помощью шпоночных соединений, а также сил трения, возникающих в результате затяжки болтов.
Компенсирующие муфты несколько сложнее, но в них допускается некоторое смещение осей валов. Эти муфты бывают двух типов: жесткие подвижные и упругие.
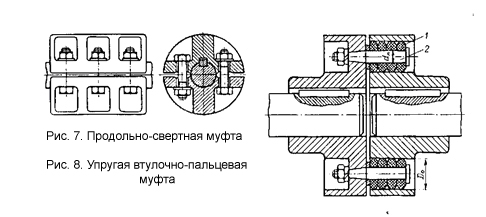
К жестким подвижным муфтам относится кулачково-дисковая муфта, состоящая из двух полумуфт с диаметральными пазами на торцах и промежуточного плавающего диска с взаимно перпендикулярными выступами. Эта муфта используется для соединения тихоходных валов с частотой вращения до 250 мин-1. Допускается радиальное смещение до 0,04 d, угловое — до 30'. Недостаток этих муфт — повышенная чувствительность к перекосам валов.
К компенсирующим муфтам относится также зубчатая муфта. Она состоит из четырех деталей — двух полумуфт с наружными зубьями и двух обойм с внутреними зубьями. Этими муфтами компенсируются радиальные, угловые (до 0,5°) и комбинированные смещения валов.
Упругая втулочно-пальцевая муфта (рис. 8) по конструкции аналогична фланцевой муфте, однако вместо соединительных болтов у упругой муфты имеются стальные пальцы 7, на которые насажены упругие резиновые или кожаные втулки 2. Эти элементы позволяют компенсировать радиальные (0,2-0,6 мм), осевые (1-5 мм) и угловые (1°) смещения валов.
Муфты с упругой звездочкой допускают большие смещения, чем втулочно-пальцевые: радиальные — до 0,01d, осевые — в пределах монтажного зазора, угловые — 1°30'.
Упругие муфты с резиновой оболочкой выполняются в различных модификациях — с оболочками цельными, разрезными или наборными, со стыкованными из двух симметричных частей.
К упругим муфтам относятся муфты, имеющие рабочий элемент в виде пружин — винтовых и плоских: первые с постоянной жесткостью, вторые с постоянной или переменной жесткостью. Во втором случае при повороте полумуфты пакет плоских пружин, вставленный в паз трапециевидной формы, деформируется так, что точка приложения окружного усилия перемещается, изгибающий момент и прогиб пружин изменяются нелинейно; происходящее при этом скольжение пластин с трением способствует демпфированию колебаний.
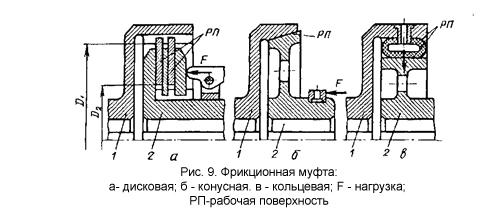
Сцепные муфты предназначены для соединения и разъединения валов. В приводных устройствах, например, закаточных машин и наполнителей устанавливают управляемые сцепные муфты.
Наиболее простая сцепная муфта — кулачковая. Основным требованием, предъявляемым к ней, является необходимость строгого центрирования полумуфт на валах, для чего служит втулка на одной из полумуфт. Эти муфты применяют для передачи значительных моментов, однако включение муфты необходимо осуществлять при весьма малой относительной угловой скорости (около 1 рад/с) или при полной остановке.
Фрикционные муфты (рис. 9) в отличие от кулачковых допускают включение под нагрузкой F на ходу. Они передают вращающий момент от левой полумуфты 1 к правой 2 за счет сил трения. В результате проскальзывания достигается плавность включения.
Фрикционные муфты работают без смазки (сухие) и со смазкой (масляные). Последние применяют в ответственных конструкциях при передаче больших моментов. Фрикционные материалы, используемые для изготовления муфт, следующие: прессованная асбесто-проволочная ткань — ферродо, фрикционная пластмасса, порошковые материалы и т. п. Их применяют в виде накладок.
Самоуправляемые муфты. Эти муфты обеспечивают автоматическое соединение или разъединение валов при изменении заданного режима работы.
Муфты свободного хода (рис. 10) предназначены для передачи вращающего момента только в одном направлении. Элементом сцепления являются ролики 3, находящиеся в клинообразном пазу, образованном внутренней 1 и наружной 2 полумуфтами. При уменьшении скорости вращения внутренней полумуфты вследствие обгона ролики выкатываются в широкие участки пазов и муфта автоматически размыкается. Муфты свободного хода работают бесшумно.
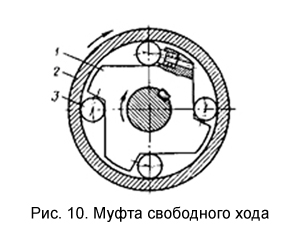
Центробежные самоуправляемые муфты служат для включения и выключения вращения валов при заданных значениях угловой скорости. Центробежная муфта состоит из ведущей и ведомой полумуфт, в пазы которых устанавливаются фрикционные грузы — колодки.
При достижении заданной угловой скорости ведущей полумуфты прижатие колодок к ведомой полумуфте центробежной силой обеспечивает такую силу трения, которая увлекает за ведущей полумуфтой ведомую, и муфта включается. При снижении угловой скорости муфта выключается. Этот тип муфты позволяет осуществить частые и плавные включения.
Предохранительные муфты. Они предназначены для предохранения деталей приводов от перегрузок. Выключение муфты осуществляется при достижении предельно заданного вращающего момента.
Наиболее простая муфта — это муфта со срезным штифтом. При достижении максимального значения момента происходит срезание штифта и осуществляется размыкание муфты. Муфта со срезным штифтом неудобна в приводах с резкими колебаниями нагрузок. Вследствие частого срабатывания приходится часто заменять штифты, поэтому эти муфты устанавливают в приводах в качестве аварийного звена.
Кулачковые муфты с трапецеидальным профилем кулачков. Последние расположены на торцевых поверхностях полумуфт, прижимаемых друг к другу одной центральной пружиной или несколькими, расположенными по окружности. Предварительное сжатие пружин обеспечивает передачу заданного вращающего момента. При достижении усилий, превышающих расчетные, возникающие осевые нагрузки сжимают пружины и кулачки одной полумуфты выходят из пазов другой. При этом муфта размыкается с характерным щелкающим звуком, предохраняя детали машины от опасных нагрузок. Кулачковые предохранительные муфты отличаются от сцепных отсутствием механизма включения. Эти муфты постоянно замкнуты. Аналогично работает шариковая предохранительная муфта, однако ее редко используют из-за трудности центровки.
Широко применяют в технике фрикционные предохранительные муфты. При перегрузке в результате проскальзывания происходит пробуксовывание этой муфты (останавливается ведомый вал). По форме рабочих поверхностей они носят названия конусных или дисковых.
Конусные муфты конструктивно несложны. При изготовлении и эксплуатации таких муфт необходимо обеспечить строгую соосность валов, равномерный контакт трущихся поверхностей, притирку рабочих поверхностей. Каждая, из полумуфт выполнена в виде конусов: один с наружной рабочей поверхностью, другой с внутренней. Передача крутящего момента осуществляется за счет сил трения, возникающих вследствие прижатия конусов друг к другу, центральной или расположенными по окружности пружинами.
По четкости срабатывания (чувствительности) и плавности включения дисковые предохранительные муфты превосходят все ранее описанные. По конструкции и принципу действия эти муфты, сходны со сцепными фрикционными дисковыми муфтами, отличаются от них отсутствием механизма управления. Возможность изменения размеров дисков и их количества позволяют применять их в широком диапазоне передаваемых моментов.
Выбор и расчет муфт. Применяемые в пищевом машиностроении муфты в основном стандартизированы. Выбирают муфты по передаваемому расчетному моменту, при этом вид муфты определяется условиями работы и ее назначением.
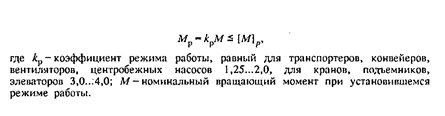
Определив расчетный момент, по таблицам находят требуемую муфту в соответствии с конструктивными особенностями проектируемого узла.
Расчет на прочность жестких (глухих) муфт проводится по основному уравнению прочности на кручение
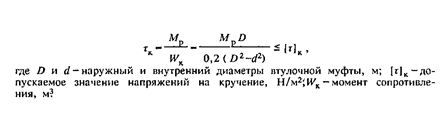
Проверочный расчет на прочность (износостойкость) кулачково-дисковых компенсирующих муфт проводят по формуле
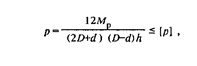
где р — максимальное давление, возникающее на рабочей поверхности сопряженных деталей муфты; D, d, h — размеры элементов муфты; [р] — допускаемое давление (для муфт с закаленными поверхностями [р] — 15-30 МПа).
С учетом радиального Дг и осевого S смещений проверочная формула имеет вид
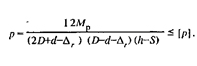
Проверочный расчет губчатых компенсирующих муфт не проводится. Их подбирают по справочным таблицам по расчетному моменту и заданным посадочным размерам.
Для упругих втулочно-пальцевых муфт проверочный расчет для пальцев проводят на изгиб по формуле
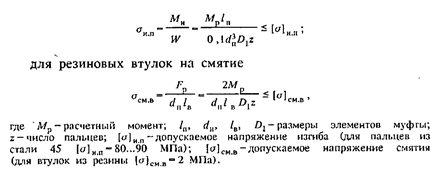
Кулачковую сцепную муфту проверяют путем расчета кулачков на износостойкость по давлению на рабочих поверхностях и на прочность по напряжению изгиба у основания кулачка.
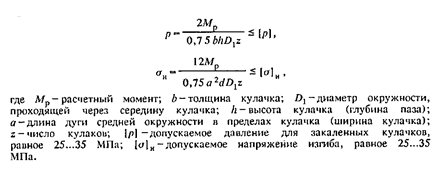
Наиболее распространенные многодисковые фрикционные муфты рассчитывают на отсутствие проскальзывания при передаче рабочего момента и на износостойкость рабочих поверхностей рабочих дисков.
Для передачи рабочего момента без относительного проскальзывания необходимо, чтобы момент сил трения был не меньше рабочего момента, создаваемого на рабочем валу:
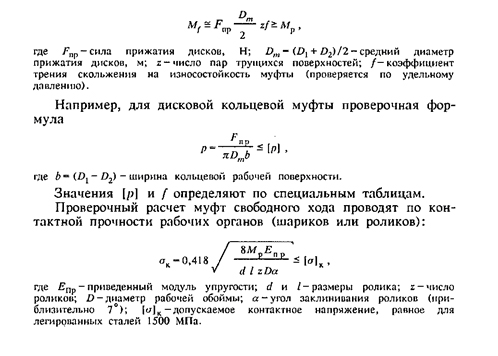
Пружины.
В машинах пружины выполняют роль упругих элементов — амортизаторов, воспринимающих толчки и удары, и аммумуляторов энергии для приведения в движение механизмов и деталей машины. Воспринимая работу внешних сил, они преобразуют ее в работу упругой деформации материала. При снятии нагрузки по мере исчезновения деформации ранее затраченная работа почти полностью возвращается.
В зависимости от напряжений, возникающих в пружинах под нагрузкой, они делятся на пружины, работающие на скручивание, работающие на изгиб и работающие на растяжение — сжатие.
На рис. 11 приведена классификация пружин.
К пружинам, материал которых работает на скручивание, относятся винтовые пружины сжатия и растяжения. Пружины сжатия должны иметь плоское основание, перпендикулярное оси пружины, для обеспечения равномерного распределения осевой нагрузки по диаметру витка. Навивка пружины производится с предварительным зазором δ между витками. Пружины растяжения имеют закрытые витки, плотно прилегающие друг к другу. Чтобы создать плотное прилегание витков, проволоку перед навивкой подвергают некоторому растяжению. После навивки происходит упругая отдача материала, пружина раздается в диаметре и витки плотно прилегают друг к другу с предварительным натяжением.
Пружины сжатия и растяжения рассчитывают на прочность по одним и тем же формулам.
Цилиндрическая винтовая пружина представляет собой винтовой стержень. Основными параметрами пружины являются: D — средний диаметр, п — число рабочих витков, t — шаг витков и а — угол подъема средней винтовой линии витков. Эти парамет¬ры связаны выражением t = πDtg а. При приложении осевой статистической нагрузки Р в поперечных сечениях витков возникают:
крутящий момент (Н • м)
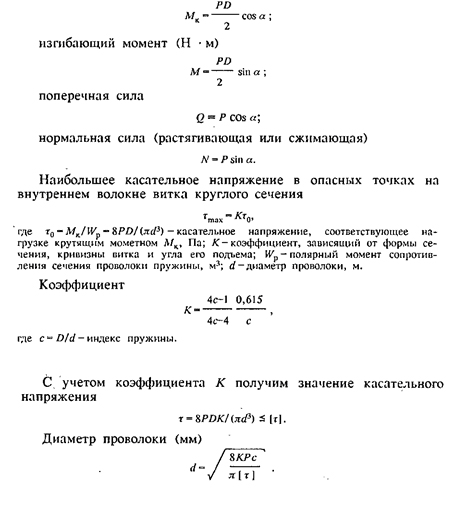
К пружинам, материал которых работает на изгиб, относятся пружины кручения, спиральные пружины, тарельчатые и плоские.
Винтовые пружины кручения воспринимают нагрузки в виде крутящего момента М— Ра.
Для получения расчетных зависимостей, так же, как и для пружин растяжения-сжатия, влияния дополнительных факторов, связанных с углом подъёма и. кривизной витков, учитываются с помощью коэффициента К, который для пружины с витками круглого сечения равен (4с— l)/(4c— 4).
Нагружающий момент вызывает в сечении витка напряжение изгиба.
Ленточная спиральная пружина также нагружается крутящим моментом. При жестком креплении концов пружины приложенный момент М будет вызывать чистый изгиб ее.
Тарельчатые пружины имеют форму усеченного конуса с углом 2-6°, изготовлены из специальной пружинной стали.
Диаметр основания D тарельчатой пружины колеблется в довольно широких пределах (28-300 мм), а высота конуса h = 0,6-9 мм. Уменьшение высоты конуса под воздействием рабочей нагрузки не должно превышать 0,8 h. Расчет тарельчатых пружин довольно сложен, поэтому пружины подбирают по специальным таблицам.
Плоские пружины предназначены обычно для усилий, действующих в пределах небольшого хода. Плоская пружина может быть защемлена обоими концами, при этом сила приложена в середине пружины, либо один конец защемлен, а сила приложена к другому.
Напряжение в консольно закрепленной пружине
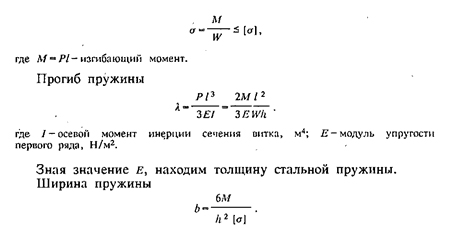
Кольцевая, или клинчатая, пружина, работающая на растяжение-сжатие, состоит из набора колец специального профиля. При нагружении крайних колец по периметру наружные кольца надвигаются на внутренние, в результате чего первые растягиваются, а вторые сжимаются. Преодолевая силы трения, кольца частично входят одно в другое, давая пружине осадку,
При конструировании пружин необходимо иметь в виду, что угол р всегда должен быть больше угла трения μ.
Соединения деталей.
Машина состоит из большого числа деталей. Для того чтобы она выполняла свои функции, эти детали должны быть соединены между собой.
Соединения деталей могут быть подвижными и неподвижными. В подвижных соединениях детали в процессе работы могут изменять положение относительно друг друга по заданному закону. Введение неподвижных соединений предусматривает расчленение машины на отдельные узлы и агрегаты, а узлы — на детали и элементы, чтобы сделать возможной сборку машины.
Неподвижные соединения бывают разъемными и неразъемными.
Разъемные соединения (резьбовые, клиновые, штифтовые, шпоночные, шлицевые) характеризуются тем, что их разборка возможна без разрушения деталей.
Неразъемные соединения можно осуществить склепыванием, вальцеванием, сваркой, пайкой, склеиванием.
Условно разъемными являются соединения, при которых в результате разборки нарушаются геометрические размеры одной из деталей, например посадка ступицы на вал посредством посадок с натягом, соединения гайка-болт с фиксирующей деталью и т. п.
Наряду с общими требованиями экономичности к соединениям предъявляются в зависимости от их назначения требования прочности, плотности (герметичности) и жесткости.
Прочность соединений оценивается величиной допускаемых предельных напряжений, при которых соединение может выполнить свои функции.
Плотность (герметичность) соединений является обязательным показателем соединений частей трубопроводов, сосудов, содержащих жидкости и газы. Герметичными неразъемными соединениями являются сварные и склеенные. Их качество зависит от квалификации рабочего. Герметичность разъемных соединений достигается сильным сжатием сопряженных поверхностей, достаточно хорошо обработанных, и применением уплотнительных прокладок.
Жесткость соединений характеризуется предельными нагрузками, при которых соединение существует. Жесткостью с системы называют отношение деформирующей силы Р к величине деформации Л[с = Р/Л для случаев линейной зависимости и с = Д/7ДА в случае нелинейной зависимости Л = /(/>)].
Резьбовые соединения. Наиболее широко распространенными разъемными соединениями являются резьбовые. Они осуществляются при помощи болтов, гаек, шпилек, винтов, шурупов. Этому способствуют высокая надежность соединений, удобство сборки и разборки, наличие большой номенклатуры элементов соединения, обеспечивающей использование данного вида соединения в любых условиях, относительно малая стоимость элементов соединений.
К главным недостаткам резьбовых соединений следует отнести:
- наличие значительного количества концентраторов напряжения;
- нетехнологичность некоторых специальных конструкций при, однако, их большой прочности.
Болт представляет собой стержень с головкой на одном конце и резьбой на другом. При соединении на резьбовой конец навинчивается гайка.
Шпилька снабжена резьбой на обоих концах. Одним концом она ввинчивается в тело одной из скрепляемых деталей, на другой конец навинчивают гайку.
Винт подобно болту имеет резьбу на одном конце и головку на другом. Своей нарезной частью он ввинчивается в подготовленное отверстие в одной из скрепляемых деталей и стягивает детали между собой. Применение гаек при этом исключается. Для соединения деталей из мягких материалов (древесина, пластмасса) используют шурупы, которые при завинчивании сами нарезают посадочное отверстие.
Резьбу на элементах резьбового соединения выполняют на токарно-винторезном станке накатыванием или фрезерованием. Резьбу, образованную на цилиндре, называют цилиндрической, на конусе — конической. В зависимости от направления вращения при заворачивании различают правую или левую резьбу.
Резьба, образованная одной винтовой ниткой, называется однозаходной, двумя, тремя и т. д. нитками — двухзаходной, трехзаходной, многозаходной резьбой.
Практика применения резьбовых соединений весьма разнообразна, поэтому подход к расчету различен.
Теоретически и практически показано, что распределение осевой нагрузки по виткам резьбовой пары неравномерно, что неблагоприятно сказывается на несущей способности резьбовой пары. При расчете витков резьбы на прочность исходят тем не менее из допущения равномерного распределения нaгрузки как по виткам гайки, так и по опорной поверхности каждого из витков. Основным является расчет резьбовой пары (болт — гайка), скрепляющей две детали.
Диаметр болта (шпильки) по заданному внешнему осевому
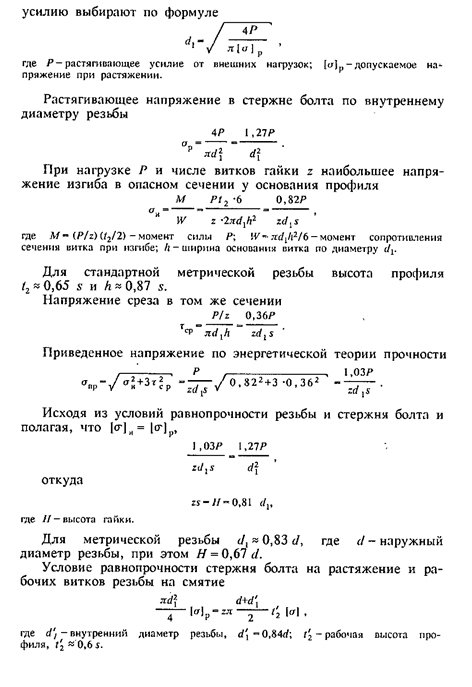
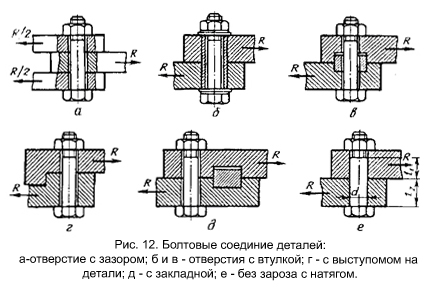
Стандартом принята нормальная длина гайки Н = 0,8 d. Расчет соединений при нагрузке резьбовых деталей поперечными силами осуществляется следующим образом. При постановке болта в отверстие с зазором (рис. 12, а) необходимо, чтобы затягивание резьбой пары обеспечивало такую предельную силу трения на стыке деталей, которая была бы равна или больше приложенной поперечной нагрузки P. Болты при этом работают ла растяжение от усилия затяжки Р0 и на кручение от момента на резьбе.
Величина усилия затяжки Р0 определяется требуемым усилием трения F, действующим в плоскостях стыка соединяемых деталей, по условию
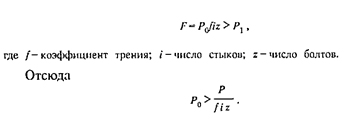
Болты рассчитывают только на растяжение по условной (расчетной) нагрузке Pp = βp0, где β — коэффициент, учитывающий влияние на прочность болта напряжений кручения.
Величина коэффициента β может быть определена путем сравнения приведенного напряжения и напряжения растяжения в сечении по внутреннему диаметру резьбы болта.
Осевое напряжение в стержне болта, как было показано выше, σp = 1,27 P0d21.
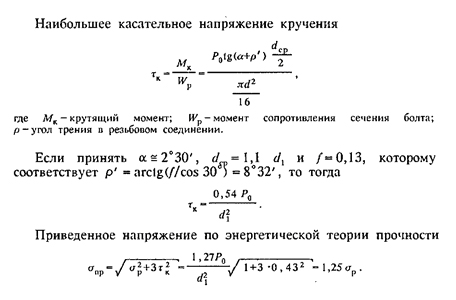
Таким образом, касательное напряжение при определении расчетной нагрузки можно учесть с помощью коэффициента /3= 1,25 при осевой силе.
В конструкциях, изображенных на рис. 12, поперечную нагрузку воспринимают втулки (рис. 12, б, в), специальные закладные детали (рис. 12, д) или выступы на соединяемых деталях (рис. 12, г). В этих случаях расчет на прочность проводится для деталей, воспринимающих поперечную нагрузку.
В случае постановки болта без зазора с натягом (рис. 12, е) поперечную нагрузку воспринимает стержень болта. Такое соединение может быть собрано без предварительной затяжки.
В некоторых конструкциях резьбовых соединений болты нагружены также изгибающими силами. Такое нагружение возникает при несимметричной головке болта либо в том случае, когда опорная поверхность соединяемой детали расположена под углом к опорной поверхности гайки или головки болта.
Для предупреждения возникновения этих напряжений при проектировании узла важно предусмотреть должную обработку опорных поверхностей или применять косые шайбы под головку болта или гайку, способные устранить влияние перекосов.
В затянутых резьбовых соединениях гайки удерживаются от отвинчивания силами трения в резьбе и на опорной поверхности гайки.
Переменные нагрузки и вибрация вызывают поперечные деформации болта и гайки. Эти поперечные деформации изменяются как по величине, так и по направлению. Вследствие наклона винтовой линии резьбы радиальное скольжение на сопряженных поверхностях ее способствует самоотвинчиванию гайки. Предупредить самоотвинчивание гайки можно применением контргайки. Ее навинчивают поверх основной гайки и затягивают так, чтобы участок болта между гайкой и контргайкой растягивался дополнительной нагрузкой, при этом верхние поверхности витков болта прижимаются к нижним поверхностям витков гайки; в контргайке — наоборот, поэтому даже при полном отсутствии нагрузки на болт или шпильку в сопряженных витках резьбы будут существовать силы трения, препятствующие самоотвинчиванию.
Широкое применение получили разрезные пружинные шайбы. В свободном состоянии концы шайбы разведены. Сжатая в соединении шайба создает одностороннюю нагрузку на гайку, тем самым предупреждая самоотвинчивание.
В качестве фиксаторов, обеспечивающих жесткую связь между деталями резьбовой пары, применяют шплинты, шайбы с усиками. Стопорные шайбы загибаются прилеганием к поверхности граней гайки и скрепляемой детали. При стопорении большой группы болтов или винтов используют проволоку, пропущенную через отверстия в головках, после чего концы ее скручивают вместе.
Шпоночные соединения. Для соединения валов с насаженными на них деталями используют шпонки. По конструкции они делятся на клиновые, призматические, сегментные и специальные.
Клиновые шпонки создают напряженное соединение, призматические и сегментные — ненапряженное.
Двумя разновидностями специальных шпонок являются круглые цилиндрические или конические шпонки. Их применяют при стопорении деталей, посаженных на конце вала. Цилиндрические шпонки создают ненапряженное соединение, конические — напряженное.
Расчет ненапряженных соединений приведен ниже. Из рассмотрения условий нагружения призматической шпонки (рис. 13) следует, что возможными повреждениями ее являются смятие боковых граней и срез.
Для того чтобы не могло быть смятия, должно выполняться

Если принять, что условный радиус приложения усилия у = d/2, то величина крутящего момента, передаваемого соединением

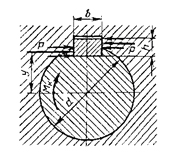
Рис.13. Соединение призматической шпонкой.
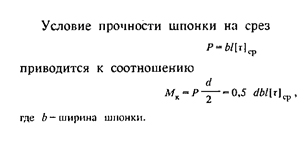
При заданном значении Мк определяют расчетную длину шпонки и из двух значений выбирают большее.
Расчет напряженных соединений следующий. Как указывалось ранее, такое соединение обеспечивается клиновой врезной шпонкой.
Величина нормального давления N, развиваемого на рабочих поверхностях шпонки, обусловлена величиной силы 5, прилагаемой к головке шпонки при запрессовке ее.
S = N[tgρ + tg (а + ρ)], где р— угол трения; а— угол скоса шпонки.
Крутящий момент, передаваемый таким соединением, Мк = 0,55 bhd [σ]см, где b— ширина шпонки; h— высота шпонки; d — диаметр вала.
Шлицевые соединения. Эти соединения служат для подвижного и неподвижного соединения с валом деталей, вращающихся вместе с ним. Для осуществления этого соединения на валу выполнены продольные выступы (зубья) прямоугольного, эвольвентного или треугольного сечения, а на ступице насаженной детали — соответствующие пазы.
По сравнению со шпоночным соединением шлицевые соединения обладают следующими преимуществами:
- обеспечивают лучшее центрирование насаженных деталей;
- значительно меньше ослабляют вал;
- позволяют уменьшить напряжения сжатия на рабочих поверхностях благодаря большой площади контакта;
- допускают более точную обработку посадочных поверхностей.
Зубья деталей шлицевых соединений работают на срез, изгиб и смятие. Решающее значение имеет прочность на смятие.
Расчетная формула при деформации смятия имеет вид
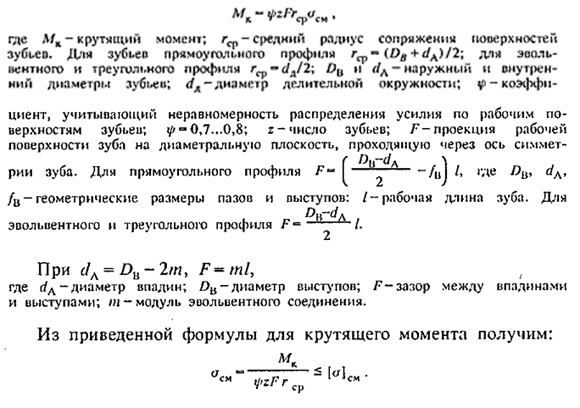
Для подвижных соединений, в которых осевое перемещение происходит без нагрузки, [σ]см = (1,5-2,0) НВ, в напряженных неподвижных соединениях [σ]см = (3-4) НВ, где НВ — твердость материала детали.
Соединения штифтами. Штифты применяются в качестве установочных, а также крепежных элементов.
Штифты бывают цилиндрическими и коническими.
Диаметр штифта d рассчитывают из условия прочности на срез. В случае нагружения соединения поперечной силой Р условие прочности
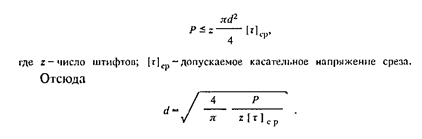
Заклепочные соединения. По назначению заклепочные соединения разделяют на прочные, плотно— прочные и плотные.
Прочные соединения — это швы, назначение которых — обеспечить прочность соединения элементов; плотно-прочные — это соединения, удовлетворяющие требованиям прочности и плотности; плотные — обеспечивают плотность.
По количеству рядов заклепок швы делятся на однорядные и многорядные. Расположение рядов может быть шахматным или параллельным.
В процессе нагружения заклепочного соединения можно наблюдать три стадии в работе соединения.
- Нагрузку передают только силы трения, действующие в плоскости стыка деталей.
- После того как нагрузка превысит максимальные значения сил трения, произойдет скольжение. Сдвиги элементов соединения компенсируют радиальный зазор между заклепкой и отверстием, и затем на второй стадии происходят упругие деформации заклепок и смятие стенок отверстий.
- Стадия упруго-пластической деформации. Начинается она с появления текучести в заклепке. В этой стадии заклепка работает на срез, смятие, изгиб и растяжение.
Расчет заклепочных соединений приведен ниже. Разрушение заклепочного шва (рис. 14) при нагружении его осевой силой Р может произойти в результате среза заклепок, разрыва детали по линии между заклепками, разрыва детали по линиям тп и m1n1 смятия заклепками стенок отверстий.
Усилие Р при количестве заклепок п в ряду равномерно распределяется:
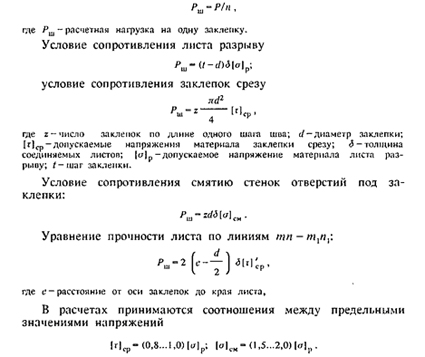
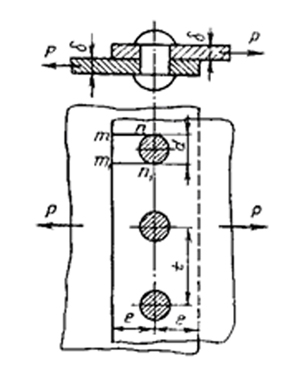
Рис. 14. Заклепочное соединение.
Для возможности размещения клепального инструмента принимают t = 3 d, для двухрядного шва t = 4 d.
Таким же образом, решая совместно уравнения прочности на срез заклепок и уравнения прочности листа по линиям тп и m1n1 и полагая, что [τ]' = 0,8 [τ] и d = 2 δ, найдем
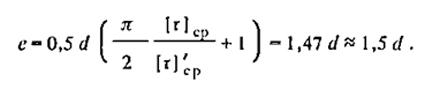
Степень использования материала деталей заклепочного соединения выражают через коэффициент прочности шва <р, представляющий собой соотношение прочности заклепочного шва к прочности неослабленного отверстиями листа.
Простыми расчетами можно определить, что для однорядного шва с двумя накладками φ = 0,71; для двухрядного шва внахлестку φ = 0,75; для двухрядного шва с двумя накладками φ = 0,83.
Решив уравнения прочности, принимая равномерное распределение приложенной нагрузки Р на каждую заклепку, получаем п заклепок в ряду. Большее значение берут в основу проектирования шва из условий его прочности.
При проектировании прочно-плотных сварных швов кроме прочности необходимо знать плотность, которая может быть обеспечена при условии отсутствия взаимного смещения листов.
Величину, характеризующую плотность, определяют экспериментально в виде так называемого коэффициента скольжения.
Этот коэффициент следует понимать как силу сопротивления проскальзывания листов, условно отнесенную к единице площади поперечного сечения заклепок,
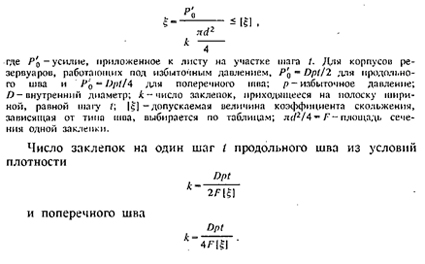
Сварные соединения. Такими соединениями называются неразъемные соединения металлических частей при помощи местного нагрева. В зависимости от источника нагрева различают следующие виды сварки: химическую (газовая, кислородная), химико-механическую (горновая и термитная), электрохимическую (атомно-водородная), электромеханическую (контактная или методом сопротивления) и электрическую (дуговая).
При сварке давлением металл свариваемых частей нагревают в местах, подлежащих соединению, до пластического состояния, после чего части сжимают и производят соединение.
При сварке плавлением металл в местах сварки нагревают до перехода его в жидкое состояние так, что расплавленный металл обеих частей образует общую ванну и при остывании дает шов.
Расчет сварных соединений производят следующим образом. Стыковой шов может быть расположен нормально к действующему усилию или под углом к внешнему усилию.
Условие прочности прямого шва при растяжении

Так, если допускаемое напряжение для наплавленного металла меньше допускаемого напряжения основного металла, пря¬мой стыковочный шов не обеспечивает одинаковой прочности по шву и по целому сечению. Вводится коэффициент прочности шва φ = [σ]ʹp/[σ]p.
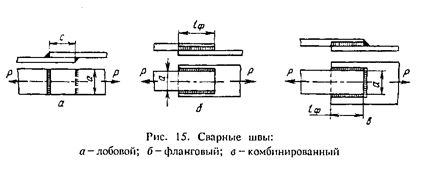
Угловые швы рассчитываются на срез. Критическое сечение совпадает с биссектрисой прямого угла. В зависимости от то¬го, какая сторона свариваемых деталей внахлестку подвергается сварке, различают лобовой шов (сварной шов соединений расположен перпендикулярно к действующей нагрузке), фланговый (параллельно) и комбинированный (сочетает оба перечисленные).
Уравнение прочности лобового шва (рис. 15, а)
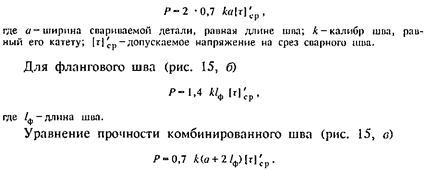
Механические свойства наплавленного металла при применении соответствующего электрода и надлежащем режиме сварки могут быть не ниже механических свойств основного металла, однако в целом прочность сварного шва ниже прочности целой детали. Это связано с особенностями строения шва и околошовной зоны.
Выбор допускаемых напряжений в сварных швах при статических нагрузках проводится в соответствии с видом сварки и применяемых электродов. Отношение допускаемого напряжения для сварных швов к допускаемому напряжению при растяжении [σ]р для основного металла будет:
- при ручной сварке при сжатии [<г] 'сж/[(г] = 0,75-0,9, при растяжении [сг]'/[сг] =0,6-0,9, при срезе М' /И0 = = 0,5-0,7;
- для автоматической сварки под слоем флюса [о1'/[сг] =0,9 и [т]'ср/Мр— 0,7:
- для полуавтоматической сварки [<г] 'сж/ [сг) = 0,9; [<г]'/Ир = 0,8 и [т]'ср/Мр— 0,6.
Ввиду отсутствия достаточного количества опытных данных рекомендуют исходить из допускаемых напряжений для статических нагрузок с учетом коэффициента при расчете стыковых швов, работающих при асимметричных циклах, при которых напряжения не меняют знака при знакопеременном цикле γ = 1/(1- 0,3 r), где r — коэффициент асимметрии цикла.
Плотность сварных швов значительно выше плотности швов заклепочных. Специальных расчетов, связанных с обеспечением плотности сварных швов, не производят.
|