01.04.2013
Механическое оборудование по переработке плодов и овощей
В плодоовощной консервной промышленности применяется различное оборудование, предназначенное для механической обработки плодов и овощей. К нему относятся машины, выполняющие процессы транспортирования, мойки и измельчения сырья, очистки и осветления жидких полуфабрикатов, а также наполнительные, дозировочные и укупорочные машины.
Оборудование для доставки и транспортировки сырья.
Плоды, ягоды, овощи, корнеплоды, виноград и другое свежее растительное сырье перевозят на заводы в ящиках или на специально оборудованных машинах и тележках без тары — навалом.
Автомобиль-овощевоз Д4-КТО-53-12. Он предназначен для бестарной транспортировки плодово-ягодного сырья в шести-ящичных поддонах. По требованию заказчика предусматривается выпуск овощевоза со сменным оборудованием: цистерной для перевозки овощей в воде Д4-КТЦ и емкостью для перевозки винограда Д4-КТЛ (кузов типа «лодочка»).
Техническая характеристика автомобиля-овощевоза Д4-КТО-53-12 |
Грузоподъемность, кг
в том числе:
полезная
установочного крана |
3000
2500
500
|
Габариты, мм
|
6575x2380x3050 |
Масса, кг
|
4630 |
Полная масса (автомобиля с нагрузкой, водителя и пассажира), кг
|
7300 |
Параметры и размеры сменного оборудования |
|
Ящичный поддон |
Цистерна Д4— КТЦ |
Емкость Д4— КТЛ |
Объем, м3 |
0,87 |
3,6 |
2,5 |
Масса, кг |
80
|
600
|
600
|
Габариты, мм |
12x835x110 |
3440x2315x1155 |
4295x2320x965 |
Автомобиль-овощевоз представляет собой базу — грузовой автомобиль ГА8-53-12 с укороченной платформой, гидрокраном 4030Ц и установленными шестью ящичными поддонами (рис. 16).
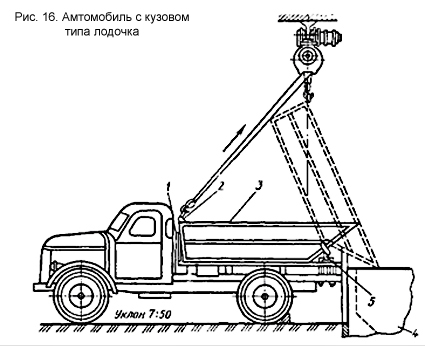
Поворотный консольного типа гидравлический подъемный кран расположен за кабиной 1 автомобиля. Привод крана осуществляется от двигателя автомобиля через коробку отбора мощности и гидронасос.
Поддон изготовлен из листового проката и уголков.
Цистерна выполнена из нержавеющей стали, установлена на лонжероны автомобиля и прикреплена к опорам, приваренным в нижней части цистерны. Кузов также установлен на лонжероны, при этом передняя часть его опирается на опору, а задняя имеет шарнирный узел 5. При поставке овощевоза с цистерной или кузовом гидравлический подъемный кран с поддоном снимают.
Овощевоз обслуживают два человека. Все погрузочно-разгрузочные работы с поддоном производят гидравлическим краном. Загрузка машины начинается от кабины.
После работы стрела крана складывается в транспортное положение и помещается в пространство между контейнерами 3 вдоль платформы, захватывается крюком за скобу 2 на платформе и натягивается с помощью гидросистемы.
Загружают цистерны через верхние люки, разгружают на пункте или заводе путем слива воды через малый люк и удаления овощей — через большой.
Кузов типа «лодочка» опорожняют с помощью стационарного подъемного устройства. Кузов захватывается краном и поднимается до полного опорожнения, после чего кузов устанавливается на опору, закрепляется и фиксируется. Таким образом перевозят яблоки, виноград. Разгружают их в приемный бункер 4 технологической линии. При приемке яблок в бункер наливают воду.
Для разгрузки ящиков и поддонов применяют различные устройства.
Опрокидыватель ящичных поддонов А9-КРЖ. Он предназначен для опорожнения ящичных инвентарных поддонов и равномерной подачи сырья с твердой структурой на дальнейшую обработку.
Техническая характеристика опрокидывателя ящичных поддонов А9-КРЖ |
Производительность, поддонов в час |
18
|
Скорость конвейера выгрузки, м/с |
0,17
|
Время поворота рамы на полный угол 150° при непрерывном вращении, с |
20±1 |
Установленная мощность, кВт |
1,3
|
Высота, мм
установки поддона
выгрузки продукта |
1800
1075
|
Габариты, мм
|
2230x1950x3250 |
Масса, кг
|
1338 |
Опрокидыватель А9-КРЖ состоит из станины, поворотной рамы, привода поворота, бункера выгрузки и электрооборудования, в состав которого входят выключатель ПКВ-25-20-12, двигатель 4А71В6У3 (0,55 кВт, 1000 об/мин) и двигатель 4А80А643 (0,75 Вт, 1000 об/мин).
После установки поддона на поворотную раму оператор включает привод поворота и рама вместе с поддоном поворачивается до тех пор, пока кнопка остается нажатой. До поворота на угол 90° сырье из поддона практически не разгружается — этому препятствует защитный лист, а затем сырье поступает в бункер загрузки. По окончании поворота (наибольший угол 150°) оператор, нажав кнопку, возвращает поворотную раму в исходное положение.
В начале поворота стопорные планки на поворотной раме освобождаются от контакта с упорами, расположенными на станине, и под действием собственного веса поворачиваются, предупреждая выпадение поддона из рамы. При возвращении порожней рамы в исходное положение стопорные планки своими рычагами вновь касаются упоров и поворачиваются до горизонтального положения, не препятствуя удалению разгруженного и установке очередного поддона.
Выгруженное сырье размещается в бункере выгрузки на полотне конвейера, который имеет два режима работы: непрерывный и с остановками.
Гидравлический транспортер. В консервном производстве широко применяют гидравлическое транспортирование. Оно используется для подачи томатов и яблок с сырьевых площадок. Одновременно осуществляется первичная мойка плодов. Гидравлический транспортер представляет собой желоб, имеющий в поперечном сечении форму полукруга с вертикальными стенками. Уклон транспортера должен составлять 8-12 мм на 1 пог. м его длины. Для нормальной работы гидравлических транспортеров радиусы закруглений в плане должны быть не менее 2,5-3,0 м.
Гидравлический транспортер рассчитывают на основании известных законов движения жидкости:
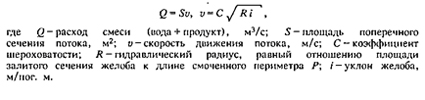
Для скорости движения смеси 0,7-0,8 м/с при кратности расхода воды по отношению к транспортируемому продукту равной 3-5 кг/кг производительность гидравлического транспортера (т/ч)
Элеватор «гусиная шея». Он предназначен для транспортирования насыпью на определенную высоту и длину овощей, фруктов и других продуктов (рис. 17).
Техническая характеристика элеватора «гусиная шея» |
Производительность техническая, т/ч |
по гороху
по овощам
по фруктам |
13,5
9,0
5,85
|
Установленная мощность, кВт |
0,8
|
Элеватор «гусиная шея» выпускают в четырех модификациях: Р9-КТ2-Э, Р9-КТ2-Э-01, Р9-КТ2-Э-02, Р9-КТ2-Э-03.
Различаются они количеством встроенных прямых коротких секций, определяющих высоту подъема продукта.
Приводная 8 и натяжная 1 станции соединены между собой с помощью прямых 7 и дугообразных 3 секций. Ковшовый транспортер состоит из двух втулочно-роликовых тяговых цепей с полыми валиками (осями) и ковшей 4. Ковши сварные из нержавеющего листового проката, корпус выполнен перфорированным или по желанию заказчика — без перфорации.
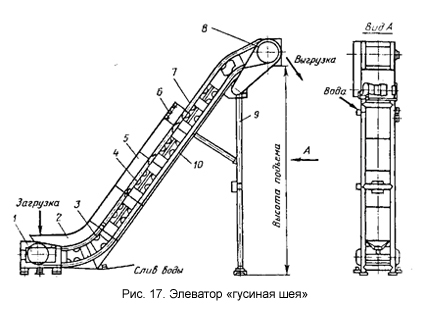
Стойка 9 сварена из труб с перемычками. Душевое устройство 6 состоит из двух труб с соплами, поперечной трубы и штуцера с резьбой для подсоединения к водопроводной сети. Набор поддонов образует желоб 10 коробчатого сечения. Транспортируемое сырье подается в бункер 2. Для предупреждения рассыпания его элеватор имеет боковые ограждения 5.
Производительность элеватора (кг/ч)

Ленточный конвейер. Он предназначен для транспортирования плодоовощного сырья под углом к горизонтальной плоскости и горизонтально.
Техническая характеристика конвейера А9-КТБ |
Производительность, т/ч |
2,0
|
Установленная мощность, кВт |
0,5
|
Ширина ленты, мм |
400
|
Скорость движения ленты, м/с |
0,4
|
Высота загрузки, мм |
от 1500 до 2650
|
Габариты, мм |
3530х900х2800 |
Масса, кг |
370
|
Конвейер А9-КТБ состоит из корпуса, приводной и натяжной станций, механизма подъема, ленты и электрооборудования.
Производительность ленточного конвейера при перемещении сыпучих грузов на плоской ленте (кг/ч)

Ленточные конвейеры используются в качестве укладочных, в этом случае продукт, подлежащий укладке, подается в противнях или тазиках.
Производительность такого конвейера (кг/ч)

Длина (м) укладочного конвейера может быть определена по заданной норме выработки одного рабочего и общей производительности транспортера:

При двустороннем расположении рабочих мест требуемая длина транспортера сокращается вдвое.
Шнековый транспортер. Он предназначен для перемещения сыпучих грузов, удаления производственных отходов. Шнековый транспортер (рис. 18) состоит из желоба 4 с крышкой 2, транспортирующего шнека J, опорных и торцевых подшипников 5, подвесных промежуточных подшипников 6, привода 1 (показан условно). Шаг шнека принимается равным 0,8-1,0 D (диаметра шнека).
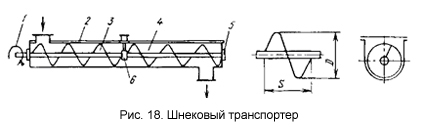
Производительность шнековых транспортеров

Насосы.
В консервной промышленности используются различные типы насосов для внутрицехового транспортирования мезги, соков, готовых жидких продуктов (сироп, повидло и т. п.). Эти продукты содержат органические кислоты, поэтому все детали, соприкасающиеся с продуктом, должны изготовляться из кислотостойких сталей или иметь защитные покрытия. Насосы должны быть герметичными и предотвращать аэрацию перекачиваемой жидкости. Основными параметрами, характеризующими работу насоса, являются производительность, напор и затрачиваемая мощность.
Производительность Q определяется объемом жидкости, подаваемой насосом в единицу времени, и рассчитывается по различным формулам, зависящим от типа насоса.
Напор (м)

При установлении насоса ниже уровня жидкости в резервуаре, т. е. подпором на стороне всасывания, высота всасывания отрицательная.
Мощность, потребляемая насосом (кВт),

Тип насоса определяется видом рабочего органа.
Поршневой насос. Он состоит (рис. 19) из привода (электродвигатель 1 с муфтой 2 и редуктором), блока цилиндров 9 с клапанами 75, воздушного колпака 11 для компенсации пульсирующего давления. Редуктор включает в себя приводной вал 3, шевронную пару шестерен 4, промежуточный вал 5 и прямозубую пару шестерен 6. Движение поршням 10 и 13 передается от коленчатого вала 7 через шток 8.
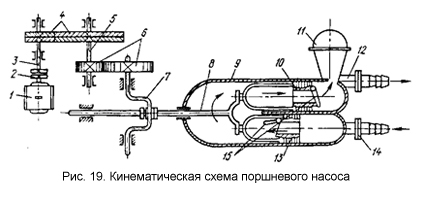
При движении поршней 10 и 13 вправо клапан 15 верхнего поршня закрывается, а нижнего открывается, жидкость выталкивается из верхнего цилиндра в нагнетательную сеть через патрубок 12 и одновременно поступает через нижний цилиндр в верхний. При обратном ходе клапан нижнего поршня закроется, и жидкость, открыв клапан верхнего поршня, будет выходить через патрубок 12 в нагнетательный трубопровод и заполнять нижний цилиндр через патрубок 14.
Принцип действия всех поршневых насосов аналогичен описанному, но при этом конструктивное выполнение клапанной коробки может быть различным. В качестве клапанов могут быть использованы обрезиненные шары.
Производительность поршневого насоса (м3/ч) — величина постоянная и практически не зависящая от напора, определяется по формуле
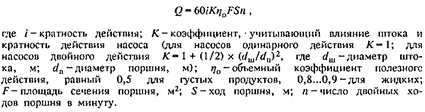
Основным требованием при работе поршневого насоса является необходимость свободного выхода нагнетаемой жидкости через патрубок 72.
Винтовой насос. Этот насос применяется для перекачивания сусла, сокоматериалов, пюре, сиропов.
С увеличением напора производительность их уменьшается незначительно, а коэффициент полезного действия остается сравнительно высоким и изменяется мало.
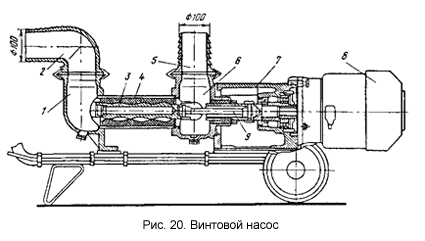
Рабочая часть насоса (рис. 20) состоит из камеры всасывания 1 с патрубком 2, однозаходного винта 3, вращающегося в неподвижной резиновой обойме 4 со стальным кожухом, и камеры нагнетания 6 с патрубком 5. Внутренняя полость обоймы представляет собой двухзаходную винтовую поверхность, шаг которой в два раза больше шага винта. Обойма установлена между камерами 7 и 6, прикреплена стяжными шпильками. Вращение от электродвигателя S передается рабочему винту 3 через карданный вал 9 в корпусе 7. При вращении винта между его поверхностью и обоймой образуются свободные полости, куда засасывается перекачиваемая жидкость и перемещается вдоль оси винта в камеру нагнетания.
Камеры всасывания и нагнетатия соединены между собой двумя трубками с проходным краном. Производительность насоса зависит от величины открытия крана.
Производительность винтовых насосов

Центробежный насос. Такой насос используется для перекачивания пульпы, соков и невязких сиропов. На рис. 21 показан насос для перекачивания дробленой или протертой томатной массы или томатного сока при температуре не более 80 °С и кинематической вязкости продукта до 20 • 10-6 м2/с, а также сходных с ними по вязкости и химической активности других пищевых продуктов.
Насос имеет литое лопастное колесо 3, которое получает вращение через наконечник 13, насаженный на вал электродвигателя 6, установленного на чугунной опоре 9. Сверху лопастное колесо закрыто крышкой 4, штампованный корпус которой снабжен входным 1 и выходным 5 патрубками. К патрубкам накидными гайками 2 крепятся ниппели 10 для присоединения насоса, крышка которого крепится при помощи зажимного кольца 8. Поворотом ручки 7 осуществляется зажим, а резиновое кольцо 12 обеспечивает герметичность соединения. Для предохранения подшипника электродвигателя от возможного попадания продукта на наконечнике установлен ограничитель 11.
Продукт подается по входному патрубку в полость насоса. При вращении рабочего колеса продукт центробежной силой отбрасывается к выходному патрубку, откуда по трубопроводам поступает на дальнейшую обработку.
Производительность центробежного насоса (м3/с) зависит от относительной скорости протекания жидкости по каналам рабочего колеса, а также от ширины и диаметра рабочего колеса:
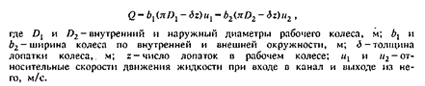
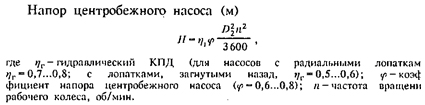
Производительность центробежного насоса при постоянной условной скорости рабочего колеса регулируется изменением степени открытия напорной задвижки. При этом допускается полное закрытие ее при работающем насосе.
Другим способом регулирования производительности является изменение частоты вращения центробежного колеса посредством электромагнитной муфты или использования тиристорного электродвигателя.
Шестеренчатый насос. Для перекачивания вязких продуктов (масел в горячем и холодном состоянии, сиропов, концентрированных соков и т. п.) применяются шестеренчатые насосы.
Конструктивная схема такого насоса представлена на рис. 22. Сцепляющиеся зубчатые колеса 7 и 2 помещены с малым зазором в корпусе 3. Одно из колес (ведущее) снабжено валиком, выходящим из корпуса через уплотняющий сальник и соединенным с приводом; другое колесо (ведомое) является холостым.
При вращении колес в направлении, указанном стрелками, жидкость поступает из полости всасывания 4 во впадины между зубьями и перемещается в напорную полость 5, здесь при сцеплении происходит выдавливание жидкости из впадин. Зубчатые колеса таких насосов обычно выполняют одинаковых размеров.
Производительность (м/ч) зубчатого насоса, состоящего из двух колес разного размера,
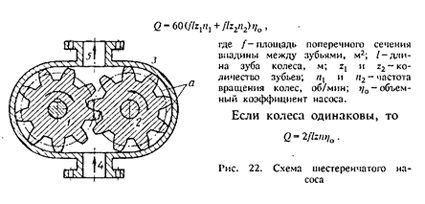
Объемный коэффициент η0 насоса учитывает перенос жидкости в пространствах а впадин (см. рис. 22) обратно в полость всасывания и принимается равным 0,7-0,9.
Зубчатые колеса обладают реверсивностью, т. е. при изменении направления вращения шестерен они изменяют направление потока в трубопроводах, присоединенных к насосу.
Производительность насоса можно регулировать изменением частоты вращения зубчатых колес или созданием специального перепускного трубопровода с регулирующим краном для возврата части нагнетаемого продукта во всасывающую полость.
Сравнительная оценка насосов.
Центробежные насосы по сравнению с другими насосами имеют следующие преимущества:
- простота и компактность конструкции, небольшие линейные размеры и масса при большой производительности;
- непосредственный привод от электродвигателя, что повышает КПД;
- небольшая стоимость изготовления, монтажа, ремонта и эксплуатации;
- простота регулирования производительности и напора, позволяющая выгодно применять их при работе с фильтрами;
- непрерывная и плавная подача жидкости;
- широта применения, так как этими насосами можно перекачивать жидкости со взвесями.
Недостатками центробежных насосов являются:
- залив перед пуском их жидкостью;
- низкий КПД при небольшой производительности;
- резкое понижение КПД при перекачивании вязких жидкостей.
Поршневые насосы имеют высокий КПД и обладают способностью самовсасывания.
Эти насосы имеют ряд недостатков:
- громоздкие размеры;
- наличие лекоизнашивающихся деталей (клапанов);
- неравномерность подачи продукта
- возможность нарушения трубопроводов или самого насоса при перекрытии свободного выхода продукта.
Винтовые насосы имеют преимущества поршневых и цетробежных насосов, однако сравнительно быстрый износ резины обойм является их недостатком.
Машины для мойки сырья.
Поступающие на переработку плоды и овощи подвергаются мойке для удаления остатков земли, ядохимикатов. Для переработки различных видов растительного сырья необходимо использовать в консервных цехах различные типы моечных машин.
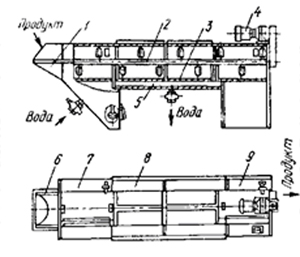
Рис. 23. Лопастная моечная машина.
Лопастные моечные машины. Эти машины применяют для мойки сильно загрязненных корнеплодов (свеклы, картофеля, моркови и т. п.).
Лопастная моечная машина А9-КЛА/1 (рис. 23) используется в поточно-механизированных технологических линиях по производству овощных закусочных консервов, где необходима предварительная мойка корнеплодов.
Техническая характеристика моечной машины А9-КЛА/1
|
Производительность, кг/ч |
не менее 3000 |
Установленная мощность, кВт |
не более 3,0 |
Расход воды, м/ч |
3,0 |
Частота вращения лопастного вала, с-1 |
0,41 |
Габариты, мм |
4635x1060x1915 |
Масса, кг |
не более 1100 |
Машина А9-КЛА/1 (см. рис. 23) состоит из станины 7, лопастного вала 2, барабана J, привода 4, поддона 5. В опоре станины со стороны загрузки находится люк для слива воды и грязи при мойке машины.
Продукт загружается в бункер 6 и из него лопастью вала 2 перегружается в отсек 7 предварительной мойки, где он перемешивается лопастями и посредством взаимного трения очищается от грязи. Частицы грязи оседают на дно и периодически выводятся из машины через сливной люк. Конструкция машины предусматривает возможность сухой очистки корнеплодов от грязи, для чего необходимо открыть полностью сливной люк, а подачу воды в отсек первичной мойки ограничить до 0,2 м3/ч.
Лопастной вал проходит через все три отсека станины 7, осуществляет перемешивание и перемещение продукта, а также выгрузку его через разгрузочное окно.
Барабан J, представляющий собой перфорированную в нижней части обечайку, расположен в отсеке 8 основной мойки. Через отверстия в нижней части барабана частицы песка и грязи оседают на дно ванны. Барабан закреплен двумя фиксаторами, которые необходимо отпускать при санитарной обработке для возможности его поворота.
В отсеке ополаскивания 9 осуществляется окончательная мойка продукта.
Вода в машину подается через коллектор с запорным вентилем. Уровень воды в ванне поддерживается переливным патрубком.
Производительность лопастных моечных машин (кг/ч) рассчитывается по формуле, которая применима для шнековых транспортеров,
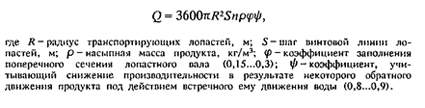
Барабанные моечные машины. Принцип вращающегося сетчатого барабана с транспортирующим шнеком, помещенного в ванну с водой, применяется для мойки твердых растительных продуктов (корнеплодов, яблок, груш и т. п.).
Барабанная моечная машина (рис. 24) состоит из станины 3 с ваннами, барабана 2, привода 7, лотка 4, душевого устройства 5, электрооборудования, включающего магнитный пускатель, пульт управления, предохранитель с плавкой вставкой, выключатель и трансформатор.
Овощи непрерывно загружаются в машину через загрузочный лоток, из которого они попадают в ванну предварительной мойки, затем перебрасываются во вторую ванну, где подвергаются вторичной мойке, затем ковшом перемещаются в третью ванну, в которой ополаскиваются под душем. Промытые овощи выгружаются в лоток и подаются на следующую технологическую операцию.
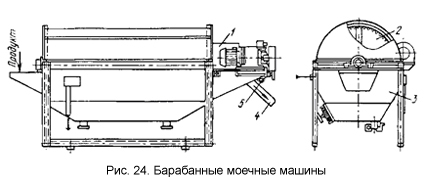
Техническая характеристика барабанной моечной машины А9-КМ-2 |
Производительность техническая, кг, не менее
по яблокам
моркови |
4000
3000
|
Установленная мощность, кВт |
1,1
|
Частота вращения барабана, с-1, не более
при мойке яблок
моркови |
1,9
1,2
|
Расход воды, м3/ч |
2±0,1 |
Давление воды в магистрали, МПа
|
0,2-0,3 |
Снижение бактериальной обсемененности продукта после мойки (при исходной 3 •106 и более), число раз |
не менее 10 |
Габариты, мм
|
3390x1270x1600 |
Масса, кг |
не более 810 |
Вентиляторные моечные машины. Они широко распространены на консервных заводах. Вентиляторными эти машины называются потому, что вода в отмоечной части подвергается турбулизации воздухом от вентилятора.
Моечная машина Т1-КУМ-5 (рис. 25) предназначена для мойки овощей и фруктов (кроме корнеплодов, листовых и бахчевых культур).
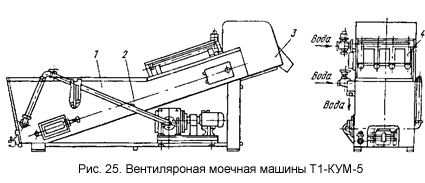
Техническая характеристика моечной машины Т1-КУМ-5 |
Производительность техническая (по помидорам), т/ч |
5,0
|
Потребляемая электроэнергия, кВт *ч |
4,1
|
Расход воды, м3/ч |
5,0
|
Снижение бактериальной загрязненности после мойки
(при исходной 3 *106), число раз |
не менее 10 |
Габариты, мм
|
3805x1285x1790 |
Масса, кг
|
910 |
Продукт, предназначенный для мойки, загружается в моечное пространство ванны, заполненной водой, где интенсивно моется в результате барботажа посредством сжатого воздуха.
Из моечного пространства ванны 7 вымытый продукт выносится наклонным транспортером 2, на верхней части которого (перед выгрузкой) ополаскивается водой из душевого устройства 4. Выгружается продукт через лоток 3.
Первоначально ванна заполняется через душевое устройство и патрубок, установленный на боковой стенке ее. В процессе работы пополнение водой осуществляется через душевое устройство. Грязная вода сливается через боковые прорези в стенке ванны.
Производительность вентиляторной моечной машины (кг/ч) можно определить по общей формуле для производительности ленточных транспортеров:

Достоинство вентиляторной моечной машины заключается в том, что интенсивное движение потоков воды в ванне приводит к удалению грязи с плодов в результате их трения между собой. Недостатком является необходимость интенсивного ополаскивания вымытого в ванне сырья вследствие того, что из-за пузырьков воздуха на поверхности воды образуется слой грязной пены и при выходе из воды чистые плоды загрязняются.
Давление чистой воды в душевом устройстве должно быть не менее 0,3-0,4 МПа.
Щеточные моечные машины. Эти машины используют для мойки огурцов, баклажанов, кабачков и других овощей с твердой кожурой.
Машина Т1-КУМ-3 (рис. 26) состоит из ванны 7, щеточных барабанов 4, регулируемого поддона J, элеватора 6, транспортера 8 с роликами 9, душевых коллекторов 5 и 10, привода 7 и электрооборудования.
Щеточные барабаны смонтированы в верхней части ванны. Каждый барабан состоит из двух блоков, которые соединены стяжками и собраны из щеток с капроновым волокном и щеток с резиновыми пальцами.
Регулируемый поддон расположен под щеточными барабанами й представляет собой раму 2 на эксцентрика. В передней части ванны на поддоне имеется металлическая решетка-камнесборник.
Элеватор, установленный в конце ванны, представляет собой вертикальный цепной транспортер с закрепленными на цепях лотками. Роликовый транспортер, расположенный за элеватором, состоит из двух параллельных ветвей с пальцами, на которых вращаются ролики 9.
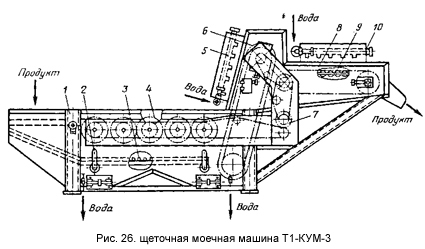
Душевые коллекторы установлены под элеватором и над роликовым транспортером.
Загруженный в переднюю часть ванны продукт попадает на наклонный камнесборник, откуда подается под вращающиеся щеточные барабаны. Зона загрузки служит также для предварительного замачивания продукта и отделения от него всплывших органических примесей.
Поступающие под вращающиеся барабаны плоды перемещаются вдоль поддона к элеватору, одновременно очищаясь от грязи. В зависимости от размеров плодов расстояние между щеточными барабанами можно изменять в пределах 50 мм. Попадая на элеватор, плоды омываются струями воды из коллектора.
С элеватора плоды подаются на роликовый транспортер, на котором вследствие вращения роликов они поворачиваются и вторично смываются струями воды.
Вымытый продукт выгружается через разгрузочный лоток. Производительность (кг/ч) щеточно-моечных машин

Вибрационные моечные машины. В некоторых моечных машинах для транспортирования сырья используется колебательное движение решетчатого полотна, на котором оно находится. Такие машины называются вибрационными моечными.
Машина А9-КМ2-Ц предназначена для мойки и ополаскивания мелкоплодных фруктов и овощей, ягод и бобовых культур. Машина может применяться для охлаждения этих продуктов после их тепловой обработки.
Техническая характеристика машины А9-КМ2-Ц |
Производительность техническая, кг/ч |
4000
|
Потребляемая электроэнергия, кВт *ч |
0,75
|
Расход воды, м3/ч
|
3,0
|
Снижение бактериальной обсемененности после мойки при исходной 3 •106, число раз |
не менее 10
|
Габариты, мм |
2000х682х1700
|
Масса, кг |
320
|
Основным рабочим органом машины является вибрационная рама, которая может осуществлять возвратно-поступательное движение. Вибрационная рама имеет решетчатое полотно, изготовленное из прутков, расположенных перпендикулярно направлению движения продукта.
Решетчатое полотно (сито) состоит из участков, имеющих угол наклона 3° в сторону движения продукта и чередующихся с участками, имеющими подъем от 6 до 15° к горизонту. Такое чередование участков на пути прохождения продукта способствует полному отделению отработавшей воды на каждом участке. Конструкция позволяет менять углы наклона участков полотна и фиксировать их в заданном положении.
Вибратор представляет собой инерционный колебатель, состоящий из двух маховиков, расположенных на двух параллельных валах, соединенных между собой зубчатой передачей. Душевое устройство — это коллектор, снабженный специальными насадками, обеспечивающими создание конического водяного душа.
Через разгрузочный лоток вымытое сырье передается на следующую технологическую операцию.
Производительность вибрационных моечных машин рассчитывается по формулам, применяемым для вибрационных транспортеров. Из описания конструкции моечной машины видно, что плоды во время мойки передвигаются по склону вниз (3°) и по склону вверх (6- 15°), поэтому этот механизм следует рассчитывать на условия движения плодов вверх под действием инерционных сил.
Ориентировочная производительность моечной машины (кг/ч)
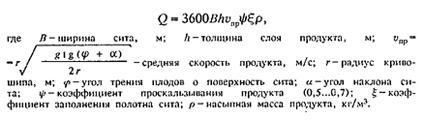
Оборудование для мойки стеклянной тары.
Стеклянная тара перед поступлением в производственный цех проходит следующие операции: подготовку к мойке, мойку, дезинфекцию, шпарку. Основным процессом является мойка стеклянной тары. Технологический процесс обработки в современных моечных машинах примерно одинаков.
Эффективность работы машины для мойки стеклянных банок, предназначенных для фасования пищевых продуктов, оценивается прежде всего полнотой удаления загрязнений как с внутренней, так и с наружной поверхности, а также снижением микробиальной обсемененности внутренней поверхности их.
В настоящее время почти все моечные машины для стеклянной тары относятся к отмочно-шприцевальному типу. В этих машинах тара погружается в различные моющие растворы, а затем подвергается многократному шприцеванию. Наиболее распространены многорядные конвейерные машины, обеспечивающие высокую производительность при сравнительно малых габаритах.
По технологическому назначению различают бутылкомоечные и банкомоечные машины для мелкой тары (от 0,2 до 1,0 л) и для крупной тары (от 3 до 10 л).
Машина СП-72. Она предназначена для мойки стеклянных банок вместимостью 500, 650, 800 и 1000 см3, поступающих со стекольных заводов или возвращенных потребителем. При заказе машины указывается вместимость банок, которые она должна обрабатывать.
Техническая характеристика моечной машины СП-72 |
Производительность, банок в час |
600
|
Длительность кинематического цикла, с
|
9,4 |
Продолжительность пребывания банок в машине, мин
|
12,4 |
Расход водопроводной воды при давлении 0,15 МПа, м3/ч
пара, кг/ч |
15
800
|
Давление пара, МПа
поступающего в машину
при отпаривании банок на выходе машины
в системе шприцевания
|
0,3-0,25
0,02-0,05
0,01-0,25
|
Температура, °С
поступающей в машину водопроводной воды, не менее
оборотной воды в ванне
подогретой водопроводной воды
щелочного раствора
в первой ванне
во второй ванне |
10
60-95
60-95
45-50
80-85
|
Жесткость воды, мг•экв/л, не более |
3,5
|
Количество моющего раствора, м3
в первой щелочной ванне
во второй щелочной ванне
в ванне оборотной воды |
2
3,8
3.2
|
Установленная мощность электродвигателей, кВт
|
19,2 |
Габариты, мм
|
6420x3450x2450 |
Масса, кг
без моющего раствора и банок
с моющим раствором и банками |
13500
20900
|
Машина СП-2 (рис. 27) по принципу действия является цепной отмочно-прицевальной с ритмично-рерывистым движением основного конвейера с банконосителями.
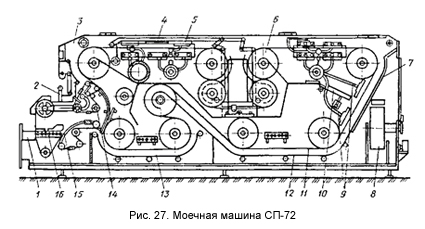
Загрузка банок с подводящего конвейера в машину, все операции мойки и выгрузка их на отводящий конвейер происходят автоматически.
Банки поступают на конвейер загрузки 7, затем на аккумулятор 76, по мере заполнения которого распределяются на шестнадцать ручьев и подаются к столу механизма загрузки 75. Планка-толкатель механизма загрузки захватывает снизу шестнадцать банок, по трубчатым направляющим подходит к банконосителям 77, находящимся в это время на высоте, и заталкивает банки в гнезда носителей. Далее банки поступают в ванну для предварительной отмочки и во вторую ванну для окончательной отмочки. Затем банки шприцуются через трубы 9 и ополаскиваются моющим раствором с лотка 10.
При повороте носителей на звездочке 6 натяжного вала на горизонтальную плоскость выливается моющая жидкость, находящаяся в банках. Носители подводят банки в зону щелочного шприцевания, где производится шприцевание внутренней полости банок в четырех позициях и наружное ополаскивание щелочным раствором из труб 5 и короба 4. Затем носители с банками погружаются в третью ванну (верхнюю) с горячей оборотной водой, где осуществляется отмочка.
Во время остановки носителей в банки с горячей водой вводятся сопла, через которые внутрь банок подается пар. В результате барботажа острым паром интенсифицируется процесс мойки. Далее носители поступают в зону шприцевания оборотной водой. Шприцевание внутренней поверхности банок происходит на четырех позициях, а наружное ополаскивание — на двух позициях. Затем осуществляется внутреннее и наружное ополаскивание подогретой водопроводной водой при температуре 60-95° С и окончательная обработка паром. После ошпаривания банки по направляющей доступают к механизму выгрузки 14 и дальше конвейером 2 выгрузки подводятся к месту розлива продукта.
В задней части корпуса 3 имеется отсек 8 для сбора этикеток. Для удержания банок в кассете имеются направляющие 7, 72, 13.
Машина СП-70. Она предназначена для мойки стеклянных банок вместимостью 2000 и 3000 см3.
Техническая характеристика машины СП-70 |
Производительность, банок в час |
1200
|
Длительность кинематического цикла, с
|
17,54 |
Продолжительность пребывания банок в машине, мин
|
18 |
Расход водопроводной воды при давлении 0,15 МПа, м3/ч
пара, кг/ч |
8
700
|
Давление пара, МПа:
поступающего в машину
при ошпаривании банок
в системе шприцевания
|
0,3-0,5
0,02-0,05
0,1-0,2
|
Жесткость воды, мг •экв/л, не более
|
3,5 |
Температура, °С, не менее
водопроводной воды
воды при шприцевании |
10
60-95
|
Моющего раствора
в первой ванне
во второй ванне |
40-45
80-85
|
Количество моющего раствора, м3 ,
в первой ванне
во второй ванне |
2
4
|
Установленная мощность электродвигателей, кВт |
18,6
|
Габариты, мм
|
7150x2700x2470 |
Масса, кг
без моющего раствора и банок
с моющим раствором и банками |
8940
14250
|
Машина СП-70 (рис. 28) является цепной отмочно-шприцевальной машиной.
Банки поступают на конвейер загрузки 76, который подает их на аккумулятор 75, по мере заполнения его банки разделяются на семь ручьев и подаются к столу 14 механизма загрузки. Планка-толкатель механизма загрузки захватывает семь банок, подводит к носителям 8 и заталкивает банки в их гнезда, а затем в первую отмочную ванну.
На петле перехода из первой ванны во вторую раствор из банок сливается обратно в ванну, а банки погружаются в моющий раствор второй ванны для окончательной отмочки.
После отмочки во второй ванне носители с банками, наполненными моющим раствором, движутся вверх по наклонной направляющей, где дважды шприцуются через трубы 5 и 9 и ополаскиваются моющим раствором, стекающим с лотка 11.
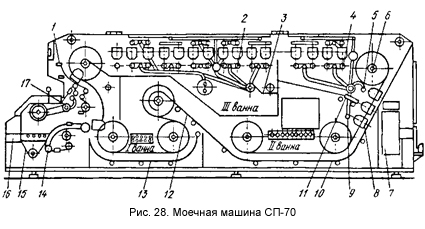
При повороте носителей на звездочке 6 натяжного вала на горизонтальную плоскость моющая жидкость, находящаяся в банках, сливается, и носители подходят в зону 4 щелочного шприцевания. Здесь происходит шприцевание внутренней полости банок в четырех позициях и наружное ополаскивание в двух позициях через шприцевые трубы и два дырчатых корыта. Далее носители поступают в зону 2 шприцевания оборотной водой.
Шприцевание внутренней поверхности происходит на восьми позициях, а наружное — на четырех. В ванночку 3 стекает вода с большим содержанием щелочи.
Далее осуществляются внутреннее шприцевание и наружное ополаскивание банок водопроводной водой температурой 60-95° С и окончательная обработка паром.
Вымытые банки по направляющей 1 подаются к механизму выгрузки 77, а затем на конвейер выгрузки. В задней части корпуса имеется отсёк 7 для сбора этикеток. Для удержания банок в носителях в отмочных ваннах установлены направляющие 10, 12 и 13. Аккумулятор представляет собой стол-рольганг.
Машина СП-60М. Она предназначена для мойки стеклянных банок вместимостью 500, 650, 800 и 1000 см3.
Техническая характеристика машины СП-60М |
Производительность, банок/ч |
3000
|
Длительность кинематического цикла, с |
12
|
Продолжительность пребывания банок в машине |
13,4
|
Количество моющего раствора в отмочной ванне,м3 |
2,4
|
Расход воды при давлении 0,15 МПа, м3/ч |
7,1
|
Давление пара, МПа |
0,4-0.5 |
Жесткость воды, мг•экв/л, не более |
3,5
|
Температура воды, °С |
5-50
|
Давление раствора в системе, МПа
водяного шприцевания
щелочного шприцевания |
0,15-0,25
0,1-0,15
|
Установленная мощность электродвигателей, кВТ |
18
|
Габариты, мм
|
6400x2700x2400 |
Масса, кг
без моющего раствора и банок
с моющим раствором и банками |
8500
13000
|
Машина СП-60М (рис. 29) представляет собой закрытый сварной корпус, в нижней части которого расположены две отмочные ванны для моющего раствора и воды, а в верхней части — ванна для оборотной воды.
Банки подводятся к машине и отводятся от нее пластинчатыми конвейерами 8. Банки с конвейера загрузки подаются на аккумулятор 10 и стол загрузки, затем планками механизма загрузки 77 — в гнезда носителей 5. Носители основного конвейера 6 с банками входят в первую водяную отмочную ванну 72, температура воды в которой 40-45° С. На петле перехода из первой ванны во вторую вода из банок выливается в первую ванну, а банки погружаются в моющий раствор второй ванны 13 при температуре 80-85° С. В дальнейшем носители с банками движутся вверх по наклонной направляющей 7 и дважды обрабатываются моющим раствором в шприцевальной системе 3.
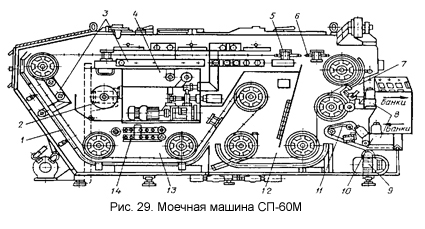
Выйдя на верхний прямой участок ванны 4, банки подвергаются внутреннему шприцеванию в трех позициях и наружному в двух позициях оборотной водой температурой 40-45° С. Затем банки по два раза шприцуются внутри и снаружи чистой водой температурой 50-55° С. При дальнейшем движении носителей остатки воды стекают с внутренней и наружной поверхности банок.
Для подогрева моющего раствора во второй отмочной ванне установлены подогреватели 14. Вода в первой отмочной ванне подогревается путем подачи оборотной воды из верхней ванны через вентиль, а в период подогрева — путем барботирования паром. Чистая горячая вода для шприцевания банок подогревается барботированием пара непосредственно в воду в специальной ванне.
Механизм 2 удаления этикеток представляет собой вращающийся сетчатый барабан, внутри которого размещен лоток сбора этикеток. Привод вала барабана осуществляется от электродвигателя. Механизм 7 выгрузки банок служит для выталкивания вымытых банок на конвейер. На электродвигателе 9 привода машины установлено реле контроля скорости, позволяющее почти мгновенно остановить электродвигатель.
Технологический расчет моечной машины. Теоретическая производительность моющих машин с ритмично-прерывистым движением носителей (банок в час)

Техническая производительность Qтехн меньше теоретической Qтеор так как при этом должны учитываться коэффициент заполнения носителей φ1 коэффициент использования кинематического цикла φ2, коэффициент точности поддержания скорости цепного транспортера φ3 и т. п.
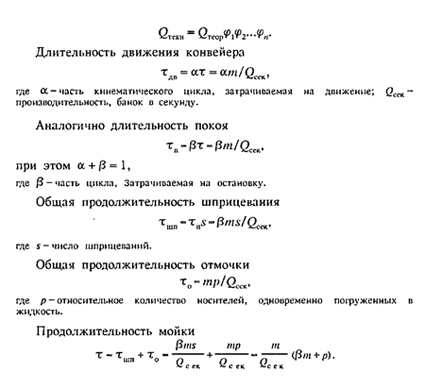
Тепловой расчет моечной машины. При составлении теплового баланса моечной машины учитывается:
Q1 — тепло, вносимое стеклянной тарой, Q1 = QceкGс1t1
Q2 — тепло, вносимое водопроводной водой, Q2 = wt2
Q3 — тепло, вносимое паром, Q3 = Di;
Q4 — тепло, уносимое стеклянной тарой, Q4 = QcекGс1t3
Q5 — тепло, уносимое водой в канализацию, Q5 = wt1
Q6 — тепло, уносимое конденсатом, Q6 = DtK;
Q7 — тепло, теряемое в окружающую среду, Q7 = Fα(t5 — t6);
где (Qсек — производительность машины, банок/с; G— масса одной, банки, кг; c1 — теплоемкость стекла, кДж/(кг*°С); t1— температура поступающей в машину стеклотары, °С; w— количество свежей воды, поступающей в машину, л/с; t2 ~ температура свежей воды, °С; D— количество пара, необходимое для нормальной работы машины, кг/с; t3— теплосодержание греющего пара, кДж/кг; tK— температура конденсата, °С; температура стеклотары при выходе из машины, °С; t4 — температура сливаемой в канализацию воды, °С; F— поверхность теплоизлучения корпуса моечной машины, м2; α — коэффициент теплоотдачи, Вг/(м2 • С); t5 — средняя температура корпуса , моечной машины; t6— средняя температура воздуха в помещении, °С.
Тепловой баланс выразится уравнением
Q1 + Q2 + Q3 = Q4 + Q5 + Q6 + Q7.
Решая это уравнение теплового баланса, получим расход пара (кг/с)

Расчет моечной машины на прочность. Рассчитывают машину так же, как транспортер, прерывистое движение которого осуществляется храповым механизмом.
Рассматривая цепной транспортер с одной ведущей звездочкой и с несколькими направляющими зубчатыми колесами, рассчитывают необходимое тяговое усилие. По этому значению определяется потребная мощность привода.
При расчете цепного транспортера вводится специальный коэффициент, учитывающий условия работы (температурные колебания воды и моечных растворов, пары щелочи и т. п.)
Оборудование для инспектирования, сортирования и калибрования плодов и овощей.
Для обеспечения требований к готовой консервированной продукции необходимо направить на технологическую линию сырье, соответствующее стандартам технологической инструкции. На консервных заводах имеются устройства и машины для инспекции кондиционной и отбраковки некондиционной продукции. Это оборудование может быть использовано и как транспортное средство.
Инспекционные и сортировочные конвейеры. По конструкции они практически не отличаются от ленточных конвейеров. Подаваемый медленно движущейся лентой инспектируемый продукт, расположенный в один слой, осматривают рабочие, стоящие по обе стороны конвейера. Некондиционное сырье снимают и сбрасывают через лотки на отводящий конвейер или в специальные контейнеры либо ящики.
Недостатком ленточных конвейеров является недоступность осмотра нижней части продукта, лежащего на ленте. Для устранения этого разработаны инспекционные конвейеры с роликовым транспортным полотном. При движении его ролики, лежащие на резиновых опорах — полочках, вращаются и поворачивают плоды, находящиеся на них в один слой. Благодаря вращению плодов шарообразной или близкой к цилиндру формы можно осмотреть всю поверхность.
Ширина и длина инспекционного конвейера зависит от его производительности и наоборот.
При двустороннем обслуживании длина конвейера (м)
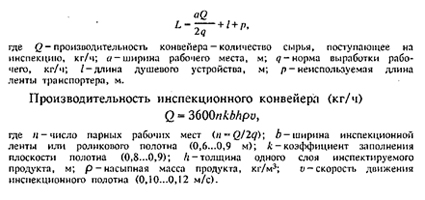
Инспекция сырья может быть совмещена с сортировкой его по степени зрелости, цвету и т. д. Производительность сортировочных конвейеров рассчитывают с учетом нормы выработки рабочего на этой операции. На основании этого определяют количество парных мест пс = Q/2qc. Скорость движения сортировочного полотна принимается такой же, как и для инспекции.
Конвейер А9-КТФ состоит из каркаса, приводной и натяжной станций, роликовой опоры, ленты, шарового катка, домкрата, лотка, сборника и электрооборудования, включающего в себя двигатель, переключатели, пост управления, трансформатор.
Техническая характеристика конвейера А9-КТФ |
Производительность, т/ч |
3,0
|
Скорость движения ленты, м/с |
0,1; 0,18
|
Высота ленты над уровнем пола, м |
0,8-0,9
|
Ширина ленты, мм |
800
|
Высота, мм
загрузки
разгрузки |
1000-1100
600-700
|
Установленная мощность, кВт |
0,75
|
Габариты, мм |
5500х1400х1100 |
Масса, кг |
850
|
Специальные продольные планки разделяют ленту по направлению движения на три зоны. Из боковых зон одну из фракций инспектируемого продукта при сортировке перекладывают в среднюю зону. При использовании конвейера только в качестве инспекционного планки можно снимать. При этом лоток для разгрузки демонтируют. При работе конвейер устанавливают на четырех домкратах, при помощи которых можно регулировать высоту ленты над уровнем пола. Режим работы — непрерывный.
Конвейер ленточный сортировочный А9-К1-1.10,0 и его модификация предназначены для разделения плодоовощного сырья по степени зрелости, цвету, пятнистости, ожогам и отбраковки некондиционных продуктов.
В зависимости от производительности, габаритов и массы конвейеры имеют несколько модификаций (табл. 3).
Техническая характеристика конвейеров типа А9-К1 |
Показатели |
А9-К1-1.5,0 |
A9-K 1-0.5,0 |
А9-К1-1.10,0 |
А9-К1-0.10,0 |
Производительность, т/ч |
5
|
5
|
10
|
10
|
Габариты, мм
длина
ширина
высота |
6790
1190
2100
|
4940
1190
1200
|
7790
1390
2100
|
7500
1400
1200
|
Масса, кг |
1050
|
850
|
1150
|
1050
|
Конвейер состоит из станины, приводной и натяжной станций, загрузочного устройства, рабочего полотна, перегрузочного устройства, карманов, привода, электрооборудования и элеватора с ополаскивающим устройством.
Сырье поступает в загрузочное устройство, где регулируемая заслонка обеспечивает равномерное распределение продукта по всей ширине рабочего полотна. Бортами оно разделено на три части, в центральную направляется отсортированный продукт. Между местами обслуживания имеются карманы, в которых отсортированный для переработки продукт может накапливаться или сразу перегружаться в контейнер.
Конвейер роликовый сортировочный А9-К2-1.10,0 предназначен для разделения плодоовощного сырья по степени зрелости, цвету, пятнистости, ожогу и отбраковки некондиционных продуктов. В зависимости от производительности, габаритов и массы конвейеры имеют несколько модификаций.
Техническая характеристика конвейра А9-К2-1.10,0
|
Скорость движения рабочего полотна, м/с |
0,15
|
Высота рабочего полотна над уровнем пола, мм
|
900 |
Ширина рабочего полотна, мм
|
1000
|
Высота, мм
загрузки
разгрузки
|
1100
1600
1650
|
Потребляемая электроэнергия, кВт*ч
|
1,1
|
Расход воды на ополаскивание 1 т сырья, м3/ч
|
1,0
|
Конвейер состоит из станины, приводной и натяжной станций, загрузочного устройства, рабочего полотна, перегрузочного устройства, карманов, привода, электрооборудования и элеватора с ополаскивающим устройством.
Конвейер инспекционный роликовый А9-КТ2-0 предназначен для инспекции и ополаскивания овощей и фруктов.
Техническая характеристика конвейера А9-КТ2-0 |
Производительность (по томатам), т/ч |
3
|
Расход воды (при давлении 0,2-0,3 МПа), м3/ч |
3
|
Скорость движения транспортерного полотна, м/с |
0,12
|
Ширина транспортерного полотна, мм |
550
|
Установленная мощность, кВт |
0,6
|
Габариты, мм
|
4250x1212x1700 |
Масса, кг |
570
|
Конвейер А9-КТ2-0 (рис. 30) состоит из каркаса 3, транспортного полотна 7, загрузочного бункера 2, карманов 4, привода 5 и душевого устройства 6. На каркасе укреплены подшипники ведущего и натяжного валов со звездочками. Звездочки несут на себе тяговую цепь с транспортерным полотном, выполненным из дюралюминиевых роликов диаметром 70 мм.
При движении полотна ролики перекатываются по резиновым направляющим, заставляя поворачиваться находящийся на них продукт, что обеспечивает лучшие условия инспекции.
На полотно продукт поступает через загрузочный бункер, снабжённый заслонкой, регулирующей толщину слоя продукта. Для удаления отходов по длине конвейера с обеих сторон расположены специальные карманы.
Продукт, прошедший инспекцию, ополаскивается водой из душевого устройства, установленного над наклонной частью конвейера. Выгружается продукт через регулируемый по высоте лоток.
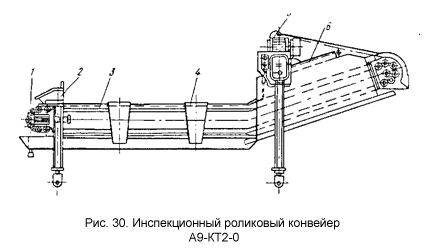
Калибровочные машины. Их используют для сортировки плодов по размеру. Схемы калибрующих устройств показаны на рис. 31.
Тросовое калибрующее устройство (рис. 31, а) состоит из двух непрерывно/движущихся расходящихся тросов 1. Плод 2 находится на тросах до тех пор, пока расстояние l между ними будет меньше диаметра плода. Когда расстояние между тросами l1 станет больше диаметра плода d, последний падает в соответствующий отсек приемного бункера. Аналогичный принцип действия имеют и другие калибрующие устройства: валково-ленточное (рис. 3, б), где рабочими органами являются ленточный конвейер 1 и ступенчатый вал 2; с двумя ступенчатыми валами (рис. 31, в); с коническими валами (рис. 31, г); со шнеками (рис. 31, д).
На рис. 31, с показано калибрующее устройство, в котором плоды самоцентрируются. Подаваемые ленточным конвейером 1 плоды поступают на вращающийся конический диск 2. Плоды самоцентрируются, скатываются вниз к щиткам 3, положение которых в зависимости or размеров плодов можно регулировать винтом 4. Таких устройств вокруг диска пять. Таким образом можно калибровать исходное сырье на пять фракций. Откалиброванное сырье отводится желобами 5, которых также пять. Частоту вращения диска можно изменять путем перемещения ролика 6.
Производительность калибровочной машины (кг/ч)
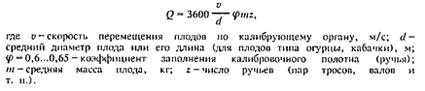
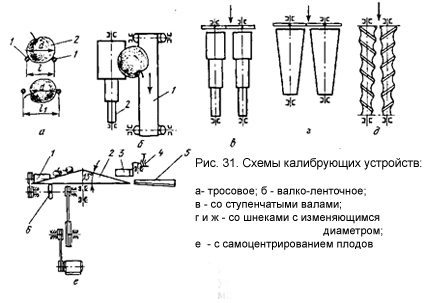
Сварная станина 10 машины изготовлена из стального проката и установлена на четырех колесах. Загрузочный бункер 4 расположен над пятью узкими наклонными ленточными конвейерами 3, снабженными скребками 5. Вращающиеся сбрасыватели 2 подают продукт в калибрующую головку 1. Здесь расположено пять пар ступенчатых валиков 7, вращающихся навстречу друг другу. Комплект, состоящий из ступенчатых и шнековых валиков разных размеров, позволяет калибровать плоды и овощи, различные по форме и величине. Калибрующая головка укреплена на станине 10 при помощи кронштейна 6.
В сборник 8 плоды выпадают из калибровочной головки. При этом, чем больше расстояние между загрузочным бункером и плодами, тем большего размера плоды находятся в сборниках, так как большая щель расположена под ними.
Ленточный конвейер 9 установлен под разгрузочными бункерами. По мере заполнения одного из них его разгружают на ленточный конвейер и подают на следующую операцию плоды одного размера.
Привод машины состоит из электродвигателя с червячным редуктором и цепных передач, вращающих ступенчатые валики или шнеки. На заводах имеются машины дискового типа, у которых расходящаяся щель свернута в окружность.
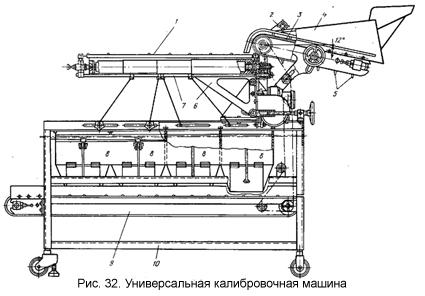
Оборудование для измельчения плодов и овощей в производстве соков.
После мойки и инспекции плоды и овощи направляют на линии производства соков. Эти линии могут выпускаться машиностроительными заводами как комплектами, так и в виде разрозненного оборудования. Первой операцией воздействия на растительную ткань при производстве соков является измельчение.
Расчет процесса измельчения. Механическое измельчение сырья основано на приложении внешних сил, превышающих молекулярные силы сцепления.
При дроблении происходит деформация продукта. В соответствии с теорией упругости абсолютная работа деформации (кДж)

Работа деформации тела до разрушения, отнесенная к единице объема, H = A/V для данного материала является постоянной величиной, характеризующей его структурно-механические свойства. Экспериментально установлено, что для дробления одного килограмма томатов следует затратить энергии 0,8-1,0 кДж, для 1 кг яблок — 1,25-1,5 кДж. По известным механическим характеристикам раздробляемого продукта рассчитывают необходимые окружные скорости дробилок ударного действия и мощность привода.
Определяющим показателем дробления является размер частиц измельченного материала, т. е. дисперсность системы. Реальные системы не только полидисперсны, но и могут состоять из частиц самой разнообразной формы: сферической, кубической, пластинчатой и т. д. При неправильной форме частиц оказывается возможным вести расчет по эквивалентному радиусу или ребру, т. е. по радиусу или ребру того шара или кубика, который по объему или массе равен действительной частице.
В практике при грубом дроблении за размер частицы принимают диаметр отверстий сита, через которое частицы исследуемого материала еще могут проходить. Также широко применяют методы определения размера частиц по скорости отстаивания. В связи с этим за эквивалентный радиус принимают также радиус тех сферических частиц, которые имеют одинаковые с рассматриваемыми частицами произвольной формы скорости отстаивания.
Вследствие того что в понятие эквивалентного размера в различных случаях вкладывают неодинаковый смысл, необходимо каждый раз пояснять, что имеется в виду — эквивалентные частицы по объему, массе или же частицы, обладающие одинаковым «гидравлическим значением», т. е. движущиеся с равными скоростями при отстаивании в спокойно стоящих сосудах.
Для практических целей разработаны простые и удобные для производственного использования приемы определения средней дисперсности смесей, позволяющие обойтись без кропотливого непосредственного подсчета числа частиц отдельных размерных классов. Для некоторых продуктов при консервировании пользуются ситовым анализом. В этом случае при помощи решетных классификаторов разделяют пробу материала на размерные фракции.
Решетный классификатор представляет собой прибор с набором расположенных один над другим сит с различными в каждом сите, но одинаковыми в каждом из них отверстиями. После просеивания образца измельченного продукта определяют массу остатка на дне классификатора и на каждом из сит. По этим данным легко вычисляют средневзвешенный диаметр (мм):
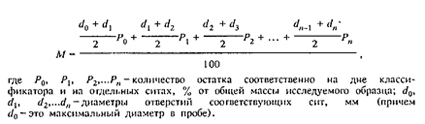
Если каким-либо способом определен гранулометрический состав смеси, то среднее значение степени дисперсности проще всего подсчитать, найдя средневзвешенную кубическую величину по формуле

Средняя степень дисперсности (по радиусу) равна обратной величине радиуса rср.
Степень измельчения плодов имеет решающее значение в процессах получения соков (продолжительность, выход сока, содержание взвешенных частиц и т. д.). Наличие большого количества мелких частиц затрудняет очистку от мякоти. Поэтому дробление необходимо провести таким образом, чтобы полученная дробленная смесь (мезга) имела оптимальный гранулометрический состав в зависимости от метода получения сока.
Дробилки. Грубое измельчение растительного сырья производится на дисковых и ножевых дробилках.
В дисковых дробилках рабочим органом является горизонтальный диск с ножами. Частоту вращения диска рассчитывают в зависимости от продолжительности падения измельчаемого продукта с высоты h. Известно, что путь свободно падающего тела в безвоздушном пространстве
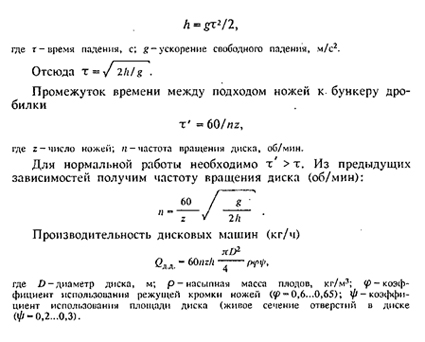
Вальцовые (одно- или двухбарабанные) машины применяют для измельчения винограда с гребнями и ягод.
Производительность вальцовых дробилок (кг/ч) рассчитывают, исходя из объема сплошной ленты материала толщиной δ, движущейся с окружной скоростью, равной окружной скорости поверхности валка,
Ножевые дробилки имеют рабочий орган, представляющий собой массивный барабан, на поверхности которого установлены ножи. Производительность ножевых дробилок (кг/ч) определяется объемом продукта, захватываемого рабочими органами за один оборот барабана,
Дробилка Д1-7,5 предназначена для измельчения овощей и плодов без косточек в линиях по производству натуральных и купажированных соков из яблок, груш, айвы, моркови, свеклы, а также в линиях по переработке тыквы на пюре.
Техническая характеристика дробилки Д1— 7,5 |
Производительность техническая, кг/ч
по яблокам
по моркови |
7500
2500
|
Содержание дробленых частиц (по яблокам),%
размером 3-8 мм, не менее
размером до 2 мм и 8-10 мм, не более |
80
20 |
Потребляемая электроэнергия, кВт•ч |
7,5
|
Частота вращения ротора, с-1
|
24,2
|
Габариты, мм |
810х485х920
|
Масса, кг, не более |
260
|
Дробилка состоит из корпуса, привода, ротора и режущего устройства. Корпус представляет собой жесткую коробчатую конструкцию, на которой монтируются все остальные узлы. В верхней части корпуса имеется загрузочный бункер.
Режущее устройство изготовляется двух типов: ножевое и терочное. Ножи пилообразной формы укрепляются в специальных обоймах, имеющих щели для удаления срезанного продукта, и предназначены для тонкого измельчения. Сменным плоским ножом можно измельчать продукт на пластины.
Режущее устройство ножевого типа используется для дробления твердых продуктов (моркови и т. п.), а режущее устройство терочного типа — для дробления мягких сортов яблок.
На валу ротора размещены подающий винт и четыре рабочих бича.
Сырье поступает в дробилку через бункер и подающим винтом, закрепленным на валу ротора, забрасывается в рабочую полость. Здесь оно подхватывается бичами ротора, центробежной силой прижимается к режущему устройству и продвигается через ножи или терочную поверхность. Измельчаясь, продукт свободно выпадает через щели устройства или терку вниз.
Дробилки Д2-7,5 и Д2-15 предназначены для измельчения томатов с одновременным отделением семян, сохраняющих свойства всхожести. После переналадки машины можно дробить томаты без включения семяотделителя.
Дробилки Д2-7,5 (рис. 33) и Д2-15 конструктивно одинаковы, различаются лишь производительностью, мощностью привода и массой (табл. 4).
Техническая характеристика дробилок |
Показатели
|
Д2-7,5
|
Д2-15 |
Производительность, кг/ч
|
7500
|
15000 |
Размеры дробленых частиц, мм, не более |
20
|
20
|
Выход семян, % к их содержанию в сырье |
50
|
50
|
Количество дробленых семян, %, не более |
20
|
20
|
Потребляемая электроэнергия, кВт•ч |
3
|
5,2
|
Частота вращения, с-1
валков мялки
шнека
бичевого вала |
1,5
4,5
15,6
|
4,5
6,75
23,7
|
Габариты, мм
|
1850x500x2050 |
Масса, кг, не более |
545
|
552
|
Все основные узлы собраны на общей станине 4. Лопастные валы мялки, шнек и ножевое устройство сепаратора имеют общий привод и смонтированы в своих корпусах. Протирочная машина выполнена как самостоятельная с индивидуальным приводом.
При работе дробилки в режиме измельчения (без отделения семян) необходимо снять сборник сепаратора и заглушить окно в плоской части корпуса, используя резьбовые отверстия, расположенные по контуру окна. При этом нужно отключить двигатель протирочной машины.
При работе дробилки осуществляются следующие операции:
- раздавливание поступающих через прямоугольный патрубок
-
подготовленных томатов в мялке 1 между восьмилопастными валками, имеющими взаимовстречное вращение;
-
отжимание шнеком с переменным шагом жидкой фазы с семенами в корпусе сепаратора 2 и дробление мякоти с кожурой в ножевом устройстве сепаратора;
-
протирание жидкой фазы с семенами в протирочной машине 3 с целью отделения семян, которые бичами продвигаются в торец протирочного барабана и выводятся из машины. Дробилка для яблок типа 361 предназначена для измельчения плодов на частицы размером 3-4 мм.
Техническая характеристика дробилки типа 361 |
Производительность, кг/ч
|
5000 |
Установленная мощность, кВт
|
13 |
Габариты, мм
|
1350x650x485 |
Масса, кг
|
385 |
В цилиндрическом корпусе установлен вал с лопастями, образующими винтовую линию. На этом же валу имеется трехлопастная звезда-ротор. К корпусу прикреплен ножедержатель с ножами. Между корпусом и ножедержателем имеются профильные карманы для удаления дробленой массы.
Из бункера, прикрепленного к корпусу дробилки, яблоки попадают на лопасти вала и перемещаются к трехлопастной звезде-ротору. Ножами яблоки дробятся на мелкие кусочки и через профильные карманы подаются на следующую операцию.
Дробилка ДДС-5 предназначена для дробления семечковых плодов. Применяется на предприятиях различной мощности.
Техническая характеристика дробилки ДДС-5 |
Производительность, т/ч |
5
|
Диаметр рабочей камеры, мм
|
450
|
Длина рабочей камеры, мм |
400
|
Частота вращения измельчающего диска, мин-1 |
1500
|
Установленная мощность, кВт |
4
|
Габариты, мм |
726х650х1014 |
Масса, кг |
400
|
Дробилка ДДС-5 состоит из корпуса, рабочего органа, привода. Вал электродвигателя соединен с валом дробилки упругой втулочно-пальцевой муфтой.
Рабочим органом служит диск, оснащенный шестью ножами-гребенками с режущей частью длинной 160 мм. Вал машины вращается в двух шариковых подшипниках. Корпус сбоку имеет загрузочный люк.
Продукт загружается в люк корпуса и подается на вращающийся диск, измельчается ножами на частицы размером не менее 3,5 и не более 10 мм. Измельченный продукт через отверстия в диске и нижнюю открытую часть корпуса удаляется из дробилки. Если дробилка установлена над прессом, то продукт поступает непосредственно в его бункер.
Дробилка А9-КИФ с семяотделителем предназначена для дробления томатов с одновременным отделением семян, сохраняющих всхожесть.
Техническая характеристика дробилки А9-КИФ |
Производительность техническая, кг/ч |
3000
|
Расход пара, кг/ч |
30
|
Давление пара, МПа |
0,2
|
Диаметр, мм, не более
валков мялки
шнека сепаратора
протирочного барабана |
215
270
220
|
Частота вращения, с-1
валков мялки
шнека
бичевого вала |
0,88
4,5
15,3
|
Мощность двигателя мялки и сепаратора, кВт
|
2,2
|
Мощность двигателя протирочной машины, кВт |
0,75
|
Габариты, мм |
1520х540х1340
|
Масса, кг |
550
|
Дробилка А9-КИФ (рис. 34) состоит из протирочной машины 1, сепаратора 4, площадки 3 для электродвигателя 6 и электрооборудбвания. Все узлы смонтированы на станине 2.
Сепаратор имеет литой корпус из нержавеющей стали, представляет собой цилиндрическую горизонтальную шнековую камеру с продольными рифлениями внутри. С одного конца шнековая камера открыта и имеет крышку, с другого конца находится горловина прямоугольного сечения с приемным окном вверху. В горловине смонтированы два лопастных валка для раздавливания перерабатываемых плодов. Валки расположены в одной горизонтальной плоскости и вращаются навстречу один другому. Вдоль шнековой камеры размещен шнек с переменным шагом, приводимый во вращение через клиноременную передачу 5 от электродвигателя 6.
Протирочная машина состоит из цилиндрического корпуса с передней и задней торцевыми крышками и сборника в виде наклонного лотка, размещенного вдоль корпуса внизу. Внутри корпуса установлен протирочный барабан. В протирочном барабане имеется бичевой вал.
При работе дробилки осуществляются следующие операции:
- раздавливание поступивших помидоров между двумя лопастными валками;
- отжимание жидкой фазы с семенами в шнековой камере и дробление кожуры с остатками мякоти в ножевом аппарате сепаратора;
- протирание жидкой фазы с целью— отделения семян.
Оборудование для отделения сока.
Полученная после дробления плодов и ягод мезга поступает на стекатели или прессы для отделения сока.Шнековые стекатели. В производстве соков в основном используются стекатели шнекового типа. Их производительность (кг/ч) рассчитывают по формуле, применяемой для шнековых транспортеров,
Широко применяют шнековые стекатели ВССШ-10 и ВССШ-20, которые являются машинами непрерывного действия (рис. 35).
Шнековый стекатель ВССШ-20 состоит и бункера 3 с перфорированными боковыми стенками, вставленными в металлический кожух. В бункере установлена вертикальная сетчатая перегородка 6. Под бункером расположен корпус стекателя 17 в форме корыта с перфорированными стенками, переходящими в перфорированный цилиндр 9. По оси корпуса и цилиндра установлен шнек 7.
На винтах шнека, расположенных под бункером, укреплены рыхлители 76. В цилиндре установлена звездочка 6, препятствующая вращению мезги совместно со шнеком. В выходном отверстии цилиндра помещается запорный конус 10, образующий со стенками цилиндра кольцевой зазор для выхода мезги. Корпус стекателя заключен в кожух 15, который служит и сборником сусла. Стекатель имеет люк 16 для чистки внутренней полости его после работы. Сусло стекает в нижнюю часть кожуха 15 и через патрубок 19 выводится из машины.
Запорный корпус вместе с гидроцилиндрами 17 и рычагами 12 является составной частью регулятора давления, обеспечивающего отделение сока.
Вращение шнека осуществляется от электродвигателя 7 через зубчатую и клиноременную передачи.
В приемный бункер мезга подается насосом. Уровень мезги в бункере поддерживается автоматическим устройством, регулирующим работу насоса для мезги, для чего в бункере установлены датчики 4 и 5. Через сетчатые стенки бункера сусло стекает в его нижнюю часть и отводится из машины через патрубок 2.
Сусло из камеры сжатия собирается в поддоне 13 и выводится из машины через патрубок 14.
Техническая характеристика стекателей типа ВССШ приведена в табл. 5.
Техническая характеристика стекателей |
Показатели
|
ВССШ-10
|
ВССШ-20 |
Производительность, т/ч |
10
|
20
|
Выход сусла, л/ч |
500-550
|
Шнеки
количество
шаг, м
частота вращения, об/мин
|
2
0,28
2,5
|
1
0,15
2,5
|
Габариты, мм
|
4400x1940x2250
|
3800x1800x2700 |
Масса, кг
|
1808
|
1500 |
Прессы. После отделения сусла на стекателях мезга направляется на прессование для полного отделения сока. Прессованию подвергается и мезга сразу же после измельчения плодов и ягод.
В соковом производстве работают прессы различной конструкции. В начале развития промышленности применяли винтовые шнеки с ручным приводом, затем их заменили гидравлическими, которые частично используют и сейчас. В настоящее время внедряются непрерывнодействующие ленточные и шнековые прессы.
Прессы периодического действия. К ним относятся гидравлические прессы.
П а к-п ресс гидравлический 2П-41 предназначен для получения фруктово-ягодных соков без мякоти.
Техническая характеристика пресса типа 2П— 41 |
Производительность (по яблокам), т/ч
|
1,35
|
Максимальное давление
при прессовании, т
в гидросистеме, МПа
|
125
20±10% |
Удельное давление, МПа
|
1,7
|
Максимальный ход плунжера, мм
|
750
|
Габариты, мм
|
3839x1479x3035 |
Масса, кг
|
3660 |
Пресс 2П-41 состоит из станины, гидроцилиндра, поворотного стола, гидропривода и электрооборудования.
Основным узлом пресса является гидроцилиндр, который предназначен для создания давления, необходимого для прессования продукта. Гидроцилиндр, крепящийся к нижней раме станины, состоит из цилиндра и плунжера.
Поворотный стол служит для подачи поддонов на плиту плунжера цилиндра. Он представляет собой раму с двумя поддонами, опирающуюся посредством роликов на неподвижное кольцо. Для предохранения от опрокидывания поворотного стола с грузом четыре ролика опираются на нижнюю и четыре ролика — на верхнюю части кольца.
Гидропривод, представляющий собой отдельный агрегат, служит для подачи масла под давлением в гидроцилиндр.
Пакет, состоящий из деревянных рамок с дробленой массой, обернутый дренажной тканью, собирается на поддоне одной стороны поворотного стола. Затем стол поворачивается на 180° так, чтобы поддон с заполненным пакетом установился над плитой плунжера. После этого эксцентриковым механизмом полностью или частично перекрывается дроссель гидропривода. Нажатием кнопки «Пуск» включается гидронасос, в результате чего плунжер с пакетом и поддоном поднимается под верхнюю плиту пресса.
В процессе прессования предусмотрены три выдержки до 5 мин каждая, при этом электродвигатель автоматически останавливается при заданных давлениях, а затем снова автоматически включается.
По достижении максимального давления и после заданной выдержки в конце прессования электромагнит автоматически открывает дроссель на слив с одновременным включением электродвигателя.
Плунжер с поддоном опускается вниз, в результате чего поддон устанавливается на поворотный стол. После этого поворотный стол поворачивается на 180° для проведения следующего цикла.
Во время прессования на другом поддоне поворотного стола формируется пакет.
Пресс РОК— 200 является самым распространенным гидравлическим прессом.
Техническая характеристика пресса РОК— 200 |
Производительность, т/ч
|
3,3 |
Максимальное давление
при прессовании, т
в гидросистеме, МПа
|
210
18,6
|
Удельное давление на мезгу, МПа
|
2,45 |
Габариты, мм
|
4345x3900x3057 |
Масса, кг
|
15000 |
Пресс имеет карусель с тремя платформами. На одной из них, располагаемой под дробилкой, формируются пакеты. Применение трех платформ позволяет одновременно проводить прессование, выгрузку и загрузку мезги. Угол поворота фиксируется специальным устройством.
Платформа, загруженная пакетами с дробленой массой, устанавливается под плитой и поднимается к ней плунжером, находящимся в гидроцилиндре. Сок при прессовании собирается в поддоне и сливается в сборник. По окончании прессования плунжер опускается и стол поворачивается на 120°. Спрессованные пакеты разбираются.
На прессе установлены пружинный и электроконтактный манометры, позволяющие контролировать и регулировать давление в гидроцилиндре.
Производительность пакетных гидравлических прессов (т/ч)
В случае совмещения операций загрузки, прессования и выгрузки продолжительность цикла определяется максимальной продолжительностью отдельной операции, к которой прибавляется время, необходимое для поворота стола.
Прессы непрерывного действия. Непрерывное прессование может быть осуществлено шнековыми или ленточными прессами.
Шнековый пресс РЗ-ВПЦ2 (рис. 36) предназначен для отжима яблочного сока. Он состоит из подвижного шнека 1, перфорированных цилиндров 2 и 7, транспортирующего шнека 3, кожуха 4, зеерного (щелевого) цилиндра 5, прессующего шнека 6, питателя 9, электродвигателей 8 и 10.
Техническая характеристика пресса РЗ-ВПЦ2 |
Производительность, т/ч |
2,0-8,0 |
Наибольшая частота вращения шнека, с-1
|
0,066 |
Габариты, мм
|
6700x830x2700 |
Масса, кг
|
3100 |
Подвижной шнек 1 имеет уменьшающийся книзу шаг витков и образует зону предварительного прессования, под которой расположена первая секция сборника сока. Мезга подается в пресс через питатель 9. Зона окончательного прессования состоит из двух участков, соответствующих двум соосным шнекам. Транспортирующий шнек 3 находится в горизонтальном перфорированном цилиндре 7. Прессующий шнек 6 установлен в зеерном (щелевом) цилиндре 5. Направление витков шнеков противоположное. Разъемный зеерный цилиндр набран из отдельных полистирольных пластин с приливами, что обеспечивает образование продольных щелей шириной 0,8 мм в начале цилиндра и 0,4 мм в конце. Под цилиндром находится сборник сока.
Пресс ВПНД-10 предназначен для отжима сока из виноградной мезги.
Техническая характеристика пресса ВПНД-10 |
Производительность, т/ч |
10
|
Мощность электродвигателя, кВт |
10
|
Габариты, мм |
4270х920х1272
|
Масса, кг |
2770
|
На сварной раме смонтированы: перфорированный цилиндр с бандажами, приемный литой бункер, редуктир, электродвигатель, запорный корпус. Внутри перфорированного цилиндра расположены транспортирующий и прессующий шнеки.
Прессующий шнек имеет переменный диаметр и шаг витка. К выходу в прессующую камеру диаметр основания шнека увеличивается, а шаг уменьшается, что приводит к уменьшению объема прессуемой массы и увеличению давления.
Производительность шнековых прессов (кг/ч)
Ленточные прессы ПЛ-2,5 и ПЛ-5,0 имеют в качестве рабочего органа фильтрующее полотно, складывающееся вертикально вдоль оси пресса. Прижатие обоих полотнищ осуществляется прижимными роликами и плитами. Дробленые яблоки подаются в складки ленты, образующиеся при вертикальном поступательном движении полотна. Мезга прессуется при одновременном движении полотна и прижимных плит, а необходимое прессующее усилие обеспечивается прижимными роликами и специальными пружинами.
После прессования полотно специальными направляющими раскладывается и отпрессованная мезга поступает на транспортер, а полотно очищается специальным устройством и промывается водой. Техническая характеристика прессов дана в табл.
Техническая характеристика ленточных прессов |
Показатели
|
ПЛ— 2,5
|
ПЛ— 5,0 |
Производительность, т/ч
|
2,5
|
5,0 |
Установленная мощность, кВт
|
4,65
|
6,6 |
Скорость движения полотна, м/мин |
0,55-2,57
|
Выход сока, % |
70-75
|
Габариты, мм
|
7800x2060x2250
|
11000x2500x3000 |
Масса, кг
|
9200
|
13000 |
Оборудование для осветления сокоматериалов.
Плодово-ягодные соки, полученные на прессах различной конструкции, представляют собой мутную полидисперсную систему, состоящую из коллоидных веществ, грубых и тонкодисперсных частиц. Для осветления используют отстойники, центрифуги, сепараторы, фильтры.
Отстойники и сепараторы. Эффективность процесса осаждения частиц из неоднородной системы под действием силы тяжести определяется той постоянной скоростью, которую имеют эти частицы при установившемся движении через некоторый промежуток времени. Как указывалось ранее, для технологических расчетов в гетерогенных (неоднородных) системах форма диспергированных частиц условно принимается сферической. Шарообразная частица радиусом r (м), оседая под действием силы с ускорением g (м/с5), испытывает на себе движущую силу
Сила F2 противодействует силе F1.
По мере увеличения скорости движения частицы сила F2 возрастает. В определенный момент силы F1 и F2 сравниваются и скорость осаждения частицы становится постоянной.
Приравнивая значения сил F1 и F2 и определяя из этого выражения значения скорости при свободном оседании, получим
При выводе этого уравнения принималось, что частица имеет форму шара, для частиц иной формы скорость будет меньше, поэтому в формулу вводится коэффициент φ = 0,43-0,77. Производительность отстойного резервуара (м3/с)
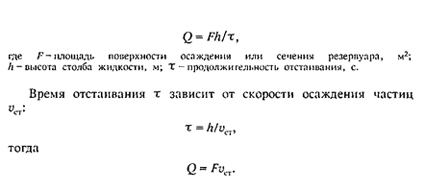
Высота слоя осадка у дна осадительного резервуара учитывается при расчете производительности и продолжительности отстаивания. Подсчет продолжительности оседания органических частиц на глубину 2 см в виноградном соке в зависимости от их размеров дал следующие результаты: для частиц с r = 10-3 см τ = 2,29 с; при r = 10-4 см τ = 3,82 ч; при r =10-5 см τ = 16 дней; при r =10-6 см τ = 4 года; при r =10-7 см τ = 436 лет. Следовательно, методом отстаивания практически можно освободить сок от частиц размером не менее 10-4, иначе для более мелких частиц потребуется длительное время и сок может забродить. Поэтому для очистки сока от мелких частиц используются сепараторы, центрифуги и фильтры.
При расчете проточных отстойников необходимо, чтобы время нахождения осветляемого материала в аппарате было больше, чем время полного осаждения частиц требуемого размера.
С целью интенсификации процесса осаждения в практике применяются также методы, обеспечивающие укрупнение частиц и снижение вязкости дисперсионной среды. Для этого сокоматериалы обрабатывают бентонитом, желатином, ферментными препаратами и т. д.
Отстаивание в консервном производстве применяется для грубой очистки свежеотжатых сокоматериалов. Для ускорения очистки соков применяют центрифугирование.
Некоторые положения о кинетике процесса осаждения в поле сил тяжести справедливы и для центрифугирования. Для этого процесса движущая сила определяется центробежной силой.
Процесс осветления соков в центрифугах протекает в три этапа: образование осадка, уплотнение его и удаление из пор осадка жидкости, удерживаемой капиллярными силами. В центрифугах различных систем могут протекать все три этапа, а также процесс может прекратиться на первом или втором этапе.
При отстойном центрифугировании наблюдается отличие от процесса осаждения. Это объясняется прежде всею не тем, что сила земного притяжения заменена центробежной силой, а тем, что в этом случае ускорение является переменной величиной и зависит от расстояния, на котором находится частица от оси вращения барабана центрифуги. Еще более усложняется процесс очистки при тонкослойном центрифугировании, когда частица движется в сужающемся радиальном потоке, где на процесс разделения влияет также скорость потока, которая является переменной величиной.
Основоположником технологических расчетов жидкостных сепараторов и центрифуг Г. И. Бремером (1928 г.) предложена формула для расчета рабочего процесса жидкостного сепаратора, из которой следует, что расчетной величиной в технологическом процессе центрифуг является разделяемость смеси, т. е. размер предельно малой, еще сепарируемой частицы дисперсной фазы, а не процентное содержание дисперсной фазы в фугате. Этим была доказана несостоятельность всех технологических расчетов полного удаления всей твердой фазы методом центрифугирования.
В расчетах центрифугальных процессов оперируют понятием фактора разделения Fr, являющегося отношением ускорения центробежной силы к ускорению силы тяжести.
При значениях Fr до 3500 центрифугальные осветлители называются центрифугами, свыше 3500 — суперцентрифугами, к которым относятся также сепараторы.
Теоретическая производительность сепаратора (м3/с)
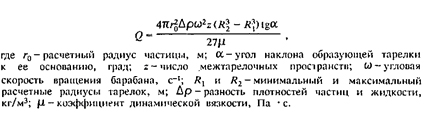
По этой формуле не получают завышенные результаты, поэтому в нее вводится поправочный коэффициент β = 0,2-0,7. Он учитывает неравномерность потоков жидкости в межтарелочном пространстве, отклонение действительной фазы взвешенных частиц от шарообразной, неравномерность плотности частицы.
Основными узлами сепаратора (рис. 37) являются плавающая верхняя опора 3 вертикального вала, барабан 6, приемник шлама 3, гидроузел 4, приемно-отводящее устройство 7, крышка 8, подъемник, пульт управления.
Станина 1 представляет собой чугунную отливку, на которой смонтированы все части сепаратора; внутри станины расположены приводной механизм и масляная ванна с люком для осмотра зубчатой пары и крышкой, на которой монтируется тахометр.
Горизонтальный вал 2 служит для передачи вращения от электродвигателя вертикальному валу 10 через центробежную муфту и зубчатую передачу.
На вертикальном валу крепится барабан, являющийся основным рабочим узлом сепаратора. В нем происходит очистка соков от механических примесей.
Гидроузел служит для регулирования подачи буферной воды в соответствующую полость барабана.
Приемник шлама предназначен для отвода осадка, выбрасываемого из барабана, а также для размещения ванны 9.
Сепаратор относится к типу полузакрытых с предварительным сливом межтарелочной жидкости и периодической центробежной выгрузкой осадка.
Сепаратор имеет автоматическое и ручное управление циклами работы.
При работе в автоматическом режиме продукт и буферная вода подается через электромагнитные вентили, команда на которые поступает с пульта управления прибором согласно настройке командоаппарата по циклограмме.
При достижении барабаном сепаратора номинального числа оборотов по сигналу командоаппарата открывается вентиль подачи буферной воды в камеру под поршень, которая заполняет ее. Создавшимся давлением поршень прижимается к крышке барабана, перекрывая щели и обеспечивая герметичность. Продукт поступает в сепаратор и одновременно очищенный сок выводится из него в производственные коммуникации. На установившемся режиме сепарирование продолжается до заполнения осадком шламового пространства барабана. Затем по команде прибора вентили закрываются. Подача и отвод продукта прекращаются. Поршень опускается, и накопившийся в шламовом пространстве осадок под действием центробежной силы выбрасывается из барабана в
приемник шлама. На этом заканчивается один полный автоматический цикл.
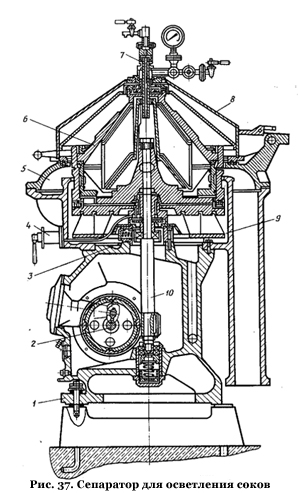
При ручном управлении вентили закрывают и открывают вручную и сам процесс осуществляется так же, как и в автоматическом режиме.
Фильтры. Фильтрование — процесс, заключающийся в разделении суспензии при прохождении ее через пористую перегородку.
Производительность фильтра определяется количеством отфильтрованной жидкости, прошедшей через единицу поверхности фильтрующей перегородки в единицу времени.
Производительность (м3/м2) по фильтрату на 1 м2 фильтрующей поверхности определяется по следующим формулам: при постоянной разности давлений и переменной скорости фильтрования
Фильтры пластинчатые (фильтр— прессы) типов П2-ВФЕ, В9-ВФС/423-56, В9-ВФС/423-53 и Т1-ФВВ-15 (табл. 7) предназначены для окончательной фильтрации натуральных соков, напитков, сиропов.
Пластинчатый фильтр составляется из квадратных металлических плит, каждая из которых представляет собой рамку, покрытую с двух сторон выступающими ребрами. Плиты делятся на четные и нечетные: четные имеют по два фасонных прилива с круглыми отверстиями с правой стороны, нечетные — с левой. В собранном виде плиты и помещенные между ними фильтрующие элементы сжимаются винтом. Приливы плит плотно прижимаются один к другому, и отверстия в них образуют каналы. Вставленные фильтрующие пластины делят пространство между двумя плитами на две камеры: четные камеры соединяются с каналами четных плит, а нечетные камеры — с каналами нечетных плит.
Техническая характеристика пластинчатых фильтров |
Показатели
|
В9-ВФС/423-56 |
В9-ВФС/
423-53
|
П2-ВФЕ
|
Т1-ФВВ-15 |
Площадь поверхности
фильтрации, м2
|
6
|
19,5
|
20,5
|
33,0 |
Производительность, л/ч
|
3000
|
9000
|
9500
|
15000 |
Максимальное давление
фильтрации, МПа
|
0,25
|
0,50 |
Установленная мощность
электродвигателя, кВт
|
4,0
|
5,5 |
9,7 |
Габариты, мм |
1730
660
1175 |
2900
960
1230 |
2950
1690
1240 |
3350
970
1520 |
Масса, кг
|
400 |
1250 |
1600 |
1894 |
По четным каналам подается мутный сок на фильтрацию, из канала он поступает в четные камеры между пластинами и проходит под давлением через фильтрующую пластину, попадает в нечетные камеры, откуда — в канал нечетных камер и по нему выводится из фильтра. Фильтрующие пластины имеют квадратную форму размером 600x600 мм и толщиной 1,2-2,0 мм.
Протирочные машины и гомогенизаторы.
Для получения тонкоизмельченных пюреобразных продуктов применяют протирочные машины и гомогенизаторы.
Протирочные машины. Для производства соков с мякотью используются пюреобразные продукты, полученные из мезги на протирочных машинах. Принцип работы протирочных машин основан на таком силовом воздействии на обрабатываемый продукт, при котором он, прижимаясь к перфорированной поверхности, теряет жидкую фазу с тонкоизмельченной мякотью, проходящую через отверстия в сите. Твердая же фаза (отходы) остается на сите внутри и выводится из машины.
На рис. 38 схематично показаны поперечный разрез протирочной машины и расположение бича 1 на ситчатом цилиндре 3. Вращение бичей осуществляется валом 2.
При допущении, что трение отсутствует, скорость перемещения частицы продукта вдоль бича (м/с)
Протирочная машина Т1-КПХ предназначена для протирания измельченных овощей, фруктов, ягод.
Техническая характеристика протирочной машины Т1-КПХ |
Производительность (по томатам), т/ч |
1
|
Частота вращения рабочего вала, об/мин |
800
|
Угол опережения бичей первой группы, град |
2
|
Пределы регулирования угла
опережения бичей второй группы, град |
0-6
|
Размеры ситчатого барабана, мм
длина
диаметр |
400
220
|
Диаметр отверстий в ситах, мм |
1,5; 1,2
|
Живое сечение сита, % |
26-27
|
Мощность электродвигателя, кВт |
1,1
|
Габариты, мм |
895х410х660
|
Масса (без подставки и электрошкафа), кг |
120
|
Машина Т1-КПХ состоит из корпуса, привода, бичевого вала с двумя группами бичей, подставки и электрошкафа.
На бичевом валу расположены шнек и пропеллер. Последний помимо перемещения сырья в ситчатый барабан под бичи служит также для его дробления.
Первая бичевая группа устанавливается на рабочем валу в зоне максимального выхода протертого продукта. Зазор между бичами и ситом и угол опережения бичей у этой группы регулируется при остановке машины.
Вторая бичевая группа размещается на рабочем валу в зоне протирания оставшейся части сырья. Поворот бичей на определенный угол происходит при перемещении специальной гильзы на валу его оси. При этом бичедержатели, эксцентриковыми пальцами входящие в наклонные лазы на валу, поворачиваются в расточках гильзы.
Сырье поступает в протирочную машину через бункер, подводится к рабочей поверхности (ситчатому полотну) с помощью шнека и пропеллера. Одновременно пропеллер, продавливая продукт через отверстия в специальном кольце, дробит его. В ситчатом барабане сырье подхватывается бичами. При этом силовое воздействие на сырье осуществляется центробежной силой, прижимающей его к поверхности барабана. Жидкая фаза проходит через отверстия сита, стекает в наклонный лоток и выводится из машины. Твердая фаза (отходы) выводится бичами из машины через отверстие в торцевой крышке.
Производительность машины и влажность отходов можно регулировать на ходу с помощью регулировочного винта, изменяя угол опережения бичей. При повышенной влажности отходов угол опережения нужно уменьшить. После поворота регулировочного винта установленное положение фиксируется с помощью специального стопора. В случае необходимости предотвратить аэрацию продукта в бункер подается пар через специальный штуцер.
Протирочная машина Т1-КП2У предназначена для протирания семечкового и косточкового сырья, для чего ротор имеет бичи двух типов.
Машина снабжена устройством для регулирования на ходу угла опережения бичей. Оно состоит из двух гильз-кулачков, одна из которых может смещаться на шпонке только вдоль вала и связана передачей с маховичком, вторая может поворачиваться вокруг своей оси. На этой гильзе находится корпус-отражатель для заброса мезги внутрь барабана и один из двух бичедержателей. Зазор между бичами и сеткой изменяется путем поворачивания ситчатого барабана при полной остановке вала ротора.
Техническая характеристика протирочной машины Т1-КП2У |
Производительность, т/ч
по семечковым плодам
косточковым плодам |
7,0
2,0
|
Диаметр отверстий сит, мм
для овощей, яблок
косточковых плодов |
1,5;1,2; 0,7-0,8
3,0; 5,0
|
Частота вращения ротора, об/мин
для семечковых плодов
косточковых плодов |
700
330; 410; 445
|
Угол опережения бичей, град |
До 1,5
|
Зазор между бичом и ситом, мм |
2,5
|
Габариты, мм |
1770х770х1115
|
Масса, кг |
508
|
Протирочная машина Т1-КП2Д представляет собой сдвоенный агрегат, предназначенный для двойного протирания томатной и фруктовой массы. Она состоит из корпуса, привода, верхнего и нижнего ситчатых барабанов, верхнего и нижнего роторов, шахты. Механизм регулирования угла опережения бичей аналогичен описанному для машины Т1-КП2У. Шахта расположена с торца машины и состоит из двух лотков для удаления отходов. Шахта крепится к корпусу при помощи петель.
Техническая характеристика протирочной машины Т1-КП2Д |
Производительность, т/ч
по томатам
моркови
яблокам |
3,5
2,0
3,25
|
Частота вращения ротора, об/мин |
790
|
Пределы регулирования угла
опережения бичей, град
для первой ступени
второй ступени |
±1,5
0-3
|
Зазор между бичами и ситом, мм |
1,5-4,0
|
Диаметр ситчатых барабанов, мм |
300
|
Длина ситчатых барабанов, мм |
835
|
Мощность привода, кВт |
5,5
|
Габариты, мм |
1535х612х1520
|
Масса, кг |
630
|
Протирочная машина Т1-КП2Т (рис. 39) состоит из соединенных вместе агрегатов для протирания 1,3 и 4, закрепленных на станине 6 со стойками 5. Агрегаты представляют собой барабаны, внутри которых вращается ротор с четырьмя бичами. Между двумя подшипниками основного подшипникового узла верхнего ротора помещен механизм регулирования угла опережения бичей на ходу. Роторы агрегатов 1 и 3 приводятся в движение от одного электродвигателя 7, агрегата 4 — от электродвигателя 2.
Отходы после протирания могут отводиться из каждого барабана отдельно, а при необходимости — собираться вместе.
Гомогенизаторы. Для получения стойкой тонкоизмельченной мякоти в соках протертую плодовую массу обрабатывают на гомогенизаторах.
Принцип работы гомогенизатора заключается в продавливании продукта через узкую щель между седлом и клапаном гомогенизирующей головки. Перед клапаном продукт имеет давление около 15-17 МПа, а после клапана — несколько больше атмосферного. При таком резком изменении давления происходит тонкое измельчение мякоти.
Гомогенизатор А1-01М предназначен для тонкого измельчения ткани при производстве продуктов детского питания, соков с мякотью и некоторых других продуктов. На корпусе гомогенизатора крепятся плунжерный блок и гомогенизирующая головка. В его монолитном корпусе имеются всасывающий и нагнетательный коллекторы, поперечные горизонтальные камеры для плунжеров и рабочие камеры. В рабочих камерах находятся карманы, седла и уплотнения. Клапаны попарно притерты к своим седлам, но при необходимости могут быть переставлены. Манжетные уплотнения плунжеров изготовляют из полипропилена, уплотнения седел — из капролона.
Тонкое измельчение мякоти осуществляется путем пропускания жидкости с большой скоростью через узкие кольцевые щели в насосах высокого давления. Жидкость, нагнетаемая плунжером под тарелку клапана, давит на тарелку и отодвигает клапан от седла, преодолевая сопротивление, создаваемое пружиной. При этом между клапаном и седлом образуется щель высотой от 0,05 до 2,5 мм, через которую жидкость проходит с большой скоростью и при этом гомогенизируется. Процесс повторяется на следующей ступени, после чего жидкость выводится из гомогенизирующей головки. Давление на первой ступени больше, чем на второй.
Гомогенизатор РЗ-КИК предназначен для тонкого измельчения мякоти в продуктах детского питания.
Роторно-пульсационный аппарат установлен на цапфах, закрепленных на станине, и соединен с электродвигателем втулочно — пальцевой муфтой. На линии подачи продукта в аппарат установлен фильтр для предотвращения попадания в него инородных тел. Это сетчатый, сменный элемент конической формы, находящийся в корпусе.
Роторно-пульсационный аппарат представляет собой корпус с размещенными в нем четырьмя неподвижными дисками — статорами, между которыми вращаются три диска — роторы, закрепленные на вертикальном валу. Продукт в аппарат подается через круглый патрубок в нижней части корпуса, сливается через патрубок прямоугольного сечения, расположенный над верхним статором.
При работе гомогенизатора смесь через фильтр поступает в аппарат и движется по каналам, образуемым отверстиями в статорах и роторах. При вращении последних многократно перекрываются каналы. Движение жидкости перекрывается несколько тысяч раз в секунду, в ней возникают значительные пульсации давления. В тонких щелях между роторами и статорами в условиях высоких напряжений сдвига и больших срезывающих усилий происходит обработка продукта. Такое одновременное воздействие обеспечивает высокую степень диспергирования.
Оборудование для очистки, резания, разделки и перемешивания сырья.
При производстве ряда консервов (компоты, джемы, обеденные консервы и т. п.) обязателен процесс отделения кожицы плодов и овощей. При этом удаляются несъедобные части плодов— семенные гнезда, косточки, семена, грубая кожица.
Машины для снятия кожуры с растительного сырья. Для очистки корнеплодов практически на всех консервных заводах используют машины периодического действия (рис. 40).
Машина представляет собой неподвижную чугунную рабочую камеру 3, внутренняя поверхность которой имеет чередующиеся выступы и впадины, препятствующие, совместному вращению корнеплодов с вращающимся диском 4. Поверхность диска покрыта абразивной массой с размерами зерен от 2 до 5 мм.
Периодическая загрузка продукта проводится при открытой крышке 2 и закрытой разгрузочной дверце 1, расположенной в нижней части лотка 11. Рабочий диск 4 приводится во вращение валом 5 от электродвигателя 9 через пару цилиндрических зубчатых шестерен 8 и 10. К нижней поверхности диска прикреплены скребки 6 для удаления снятой кожуры из машины через патрубок 13.
Для смывания разрушенной кожуры с продукта внутрь рабочей камеры под напором подается чистая водопроводная вода через форсунку 12. Для смазки вертикального вала машины имеется масленка 7. Все детали смонтированы на станине 14.
Центробежная сила, развиваемая в роторе машины (кг — м/с2),
При определении минимальной угловой скорости или частоты вращения диска исходят из необходимости перемещения корнеплодов от центра диска к периферии. Для этого необходимо следующее неравенство: С > Gf1.
На основании этого неравенства получим
Продолжительность загрузки обычно равна 25-30 с, выгрузки — 15 с. Эти значения подставляют в формулу расчета производительности.
Средняя продолжительность обработки корнеплодов 1-1,5 мин.
Низкая производительность очистительных машин периодического действия и необходимость ручных операций по их обслуживанию обусловили создание непрерывнодействующих машин.
Производительность таких машин (кг/ч)
Картофелечистка непрерывного действия КНА-600М имеет в качестве рабочего органа 20 валиков с абразивной поверхностью, составляющих с помощью перегородок четыре секции с волнообразной поверхностью.
Машина состоит из рамы, ванны, наружного каркаса, клиноременной передачи, душевого устройства, разгрузочного лотка, привода, загрузочного бункера.
Машина для очистки чеснока А9-КЧП предназначена для разделения головок его на дольки, очистив их от шелухи, и отвода ее в специальные сборники.
Основным рабочим органом машины является узел очистки, представляющий собой четыре вращающиеся рабочие камеры.
Рабочая камера — это цилиндр, открытый сверху и снизу. Он состоит из двух элементов: литого алюминиевого корпуса и внутренней фиксируемой нержавеющей сменной вставки, устанавливаемой по направляющему штифту, что обеспечивает совпадение отверстий для подачи сжатого воздуха в ней и в корпусе.
Сжатый воздух подается в рабочие камеры через сопла, позволяющие достичь звуковых и сверхзвуковых скоростей струи воздуха. Отсечка и подача сжатого воздуха в камеры производится цилиндрическим золотником на полом валу.
Устройство для отвода и сбора шелухи состоит из воздуховода и вентилятора.
Чеснок в головках по наклонному транспортеру подается в бункер, днище которого совершает колебательные движения и обеспечивает равномерное поступление продукта в питатель, а оттуда в дозаторы. При подаче чеснока в бункер машины вручную техническая производительность ее снижается до 30-35 кг/ч.
Техническая характеристика протирочной машины Т1— КП2Т |
Производительность (по томатам), т/ч |
10,0
|
Частота вращения ротора, об/мин |
800
|
Пределы регулирования угла опережения, град |
±1,5 |
Зазор между бичами и ситом, мм |
±2,5 |
Диаметр барабанов, мм |
388
|
Длина барабанов, мм |
856
|
Диаметр отверстий в сите, мм
если семяотделитель установлен
если семяотделитель отсутствует |
1,5; 0,8; 0,4
5,0; 1,5; 0,8
|
Мощность привода, кВт |
17
|
Габариты, мм |
2500х1715х2595
|
Масса, кг |
1500
|
Вращающиеся вместе с диском четыре дозатора, проходя периодически под питателем, пополняются двумя-четырьмя головками чеснока. После выхода из-под загрузочного отверстия камера перекрывается сверху диском, образуя замкнутую полость, в которую подается сжатый воздух. Сухие головки чеснока удовлетворительно очищаются при рабочем давлении сжатого воздуха в машине, равном примерно 2,5 • 10 -5 Па. Для увлажненного чеснока необходимо давление до 4-10 -5 Па. Далее очищенный чеснок попадает на инспекционный транспортер, затем цикл повторяется.
При скорости вращения ротора 5-6 об/мин цикл работы обеспечивается системой передачи и электрооборудованием, состоящим из электродвигателя, приводящего в движение камеры и дозаторы, электродвигателя вентилятора, двух постов управления и электрошкафа.
Агрегат для паротермической очистки овощей 2439к предназначен для снятия кожура с корнеплодов (картофеля, сельдерея, моркови) с помощью пара.
Машина состоит из питающего транспортера; двух роторных питателей, один из которых предназначен для загрузки сырья, второй — для выгрузки; винтового конвейера с паровой камерой; двух приводов — один для шнека, другой для иных механизмов. Агрегат имеет систему подачи пара и сброса конденсата, систему централизованной принудительной и ручной смазки.
Работа транспортера и приемного питателя синхронизированы во избежание повреждений сырья.
Обрабатываемый продукт подается транспортером в приемный роторный питатель, который, вращаясь с постоянной скоростью, подает продукт в винтовой конвейер. В нем продукт подвергается воздействию пара, интенсивно перемещается к выводному ротору. При этом происходит проварка продукта на глубину около 1 мм, что необходимо для последующего снятия кожуры после выгрузки его из машины и подачи на мойку.
Производительность рассчитывают по формуле для винтовых конвейеров.
Агрегат для паровой очистки картофеля А9-КЛШ/30 предназначен для паротермической очистки картофеля от кожуры. Может быть использован для очистки от кожуры моркови, свеклы и других корнеплодов.
Агрегат А9-КЛШ/30 (рис. 41) состоит из наклонного сдвоенного дозировочного конвейера 1, предназначенного для циклической подачи клубней картофеля поочередно в две автоклавные камеры 2 для паротермической очистки клубней картофеля от кожуры, снабженных затворами, управляемыми пневмоцилиндрами; непрерывнодействующего винтового конвейера 10 для перемещения обработанных паром клубней, выгружаемых из автоклавных камер, к разгрузочному конвейеру; непрерывнодействующего наклонного винтового конвейера 4 для выгрузки и подачи клубней на последующую обработку (сухую очистку); станины 9, на которой размещены все составные части аппарата; коммуникаций 3, 5 и 7 соответственно для пара, воды и сжатого воздуха; электрооборудования площадки обслуживания 6.
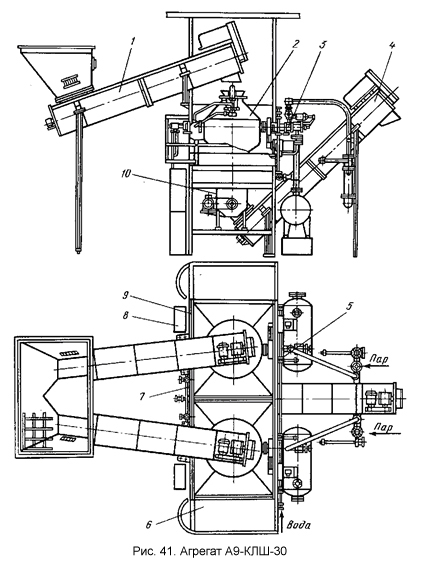
Вымытый картофель подается наклонным сдвоенным винтовым конвейером 1 в одну из автоклавных камер 2. В исходном положении перед загрузкой камера ориентирована загрузочной воронкой вертикально вверх, при этом затвор располагается в крайнем нижнем положении и обеспечивает свободный вход клубней картофеля во внутреннюю полость камеры.
После загрузки заданной порции картофеля затвор пневмо-цилиндром и рычажной системой перемещается в крайнее верхнее положение (к горловине камеры) и обеспечивает предварительную герметизацию камеры. Окончательная герметизация Головины камеры затвором осуществляется острым паром, подаваемым во внутреннюю полость, давлением 0,7-0,8 МПа. При этом камера получает вращательное движение. По истечении установленного времени происходит быстрый сброс пара, а затем открывается затвор и выгружается порция картофеля, обработанного паром. Технологический процесс циклично повторяется. Картофель двумя винтовыми конвейерами выводится из аппарата на последующую обработку.
Аппарат предусматривает работу двух автоклавных камер как в сблокированном режиме, так и автономно.
Производительность такого агрегата (кг/ч) рассчитывается так же, как у периодически действующих машин:
Аппарат А9-КЧЯ предназначен для очистки корнеплодов от кожуры насыщенным водяным паром на предприятиях малой и средней мощности.
Принцип работы аппарата А9-КЧЯ заключается в цикличной подаче корнеплодов в резервуар при различных режимах работы аппарата. В исходном положении перед загрузкой резервуар ориентирован загрузочной воронкой вертикально вверх, крышка находится в крайнем нижнем положении и обеспечивает свободный вход корнеплодов во внутреннюю полость резервуара. После загрузки заданной порции корнеплодов происходит герметизация резервуара в результате подачи во внутреннюю полость острого пара давлением 0,8 МПа. Одновременно резервуар получает вращательное движение. По истечении установленного времени происходит резкий сброс пара в расширитель, открытие крышки и выгрузка корнеплодов. Винтовым разгрузочным конвейером корнеплоды перемещаются из ванны на окончательную дочистку и последующую обработку.
Машины для удаления косточек, плодоножек, семенного гнезда и плодов. Машины для удаления косточек можно разделить на две группы: для легкоудаляемых и для трудноудаляемых косточек. Косточковыбивные машины применяются для обработки плодов с легкоудаляемыми косточками (вишни, сливы, абрикосов, некоторых сортов персиков), косточковырезные — для плодов с трудноудаляемыми косточками (некоторые сорта персиков и слив).
Рабочим органом косточковыбивных машин является возвратнодвижущийся пуансон. Косточки выбиваются в момент остановки пластины с матрицей, в ячейки которой уложены плоды. Матрицы могут крепиться к барабану или двум цепным транспортерам.
Производительность для этих машин (кг/ч)
На консервных заводах эксплуатируются венгерские машины для удаления косточек.
Машины типа 1-08-3 имеют полый цилиндрический барабан, опирающийся на ролики и имеющий лунки со сквозными отверстиями. Привод барабана обеспечивает его прерывистое вращение.
Плоды, попавшие в лунки, подводятся под пуансон, и в момент остановки движущийся вниз пуансон выдавливает косточки, которые, проходя через сквозное отверстие, падают в желоб внутри барабана и выводятся из машины шнеком.
Производительность машины 800-1200 кг/ч.
Машина С183/а представляет собой расположенный на опорах корпус, внутри которого движутся тяговые цепи с прикрепленными к ним носителями. Выемки на соседних носителях образуют полости, в которые помещаются плоды (например, персики).
При периодических остановках транспортирующего органа находящаяся в передней его части траверса опускается, при этом плод разрезается пополам и косточка удаляется. При переходе носителей через приводные звездочки половинки плодов выпадают на разгрузочный лоток.
Производительность до 1500 шт/ч.
Машина М8-КЗП производит отрыв плодоножки путем затягивания ее в зазор между двумя вращающимися навстречу один другому обрезиненными валиками (рис. 42). Валики 1 и 2 должны иметь такой диаметр, чтобы они не могли втянуть и раздробить плод 5. На каждый валик действуют силы, обусловленные как массой плода, так и силой, возникающей в момент отрыва плодоножки 4.
Равнодействующая вертикальная составляющая Rp, стремящаяся вытолкнуть плод, равна 2Psinα. Этому противодействует равнодействующая сил трения, направленная вниз,
Это условие выполняется тогда, когда диаметр валиков примерно равен диаметру плода.
Основными узлами машины для отрыва плодоножки М8-КЗП (рис. 43) являются тележка 1, рама 2, ворошитель и привод 3 рабочих валиков 4.
Сырье, подлежащее обработке, загружается в бункер. Благодаря наклону рамы плоды смещаются вдоль вращающихся с частотой 850 об/мин валиков диаметром 17 мм каждый. Плодоножки затягиваются между валиками, отрываются и падают в поддон. Для снижения коэффициента трения плоды сверху орошаются водой.
Машины для резания. Механическое измельчение можно осуществить резанием плодов и овощей.
Для расчета работы, затрачиваемой на разрезание продукта, используют экспериментальные данные по величине усилия Р, которое должно быть приложено к кромке длиной 1 см. Удельную работу разрезания W (кДж/см2) определяют как произведение усилия Р на путь l: W=Pl • 10— 4.
Особое значение при расчете резательных машин имеет коэффициент скольжения, определяемый из отношения β = v1/vn, где v1 и vn — соответственно касательная и нормальная составляющие движения ножа. Чем больше нормальная составляющая vn, тем меньше коэффициент скольжения, и в пределе vn = ∞, разрезание превращается в рубку. При vn = 0 коэффициент скольжения становится бесконечно большим и нож скользит в материале, не разрезая его. Это происходит в том случае, если нет подачи материала в машину. Коэффициент скольжения β для резательных машин обычно равен 10-50.
Отечественной промышленностью выпускаются резательные машины различных конструкций. Удаление несъедобной части (семенного гнезда) у яблок или груш осуществляется на полуавтоматических и автоматических машинах. На консервных заводах используются болгарские полуавтоматы. Рабочим органом является трубчатый нож с четырьмя перьями— ножами. Яблоко или грушу работница укладывает в лунку диска с вертикальной осью вращения так, чтобы ось плода размещалась вдоль оси трубчатого ножа.
Нажатием педали трубчатый нож опускается, вырезая сердцевину и разрезая плод на дольки. В дальнейшем диск поворачивается и перед работницей находится следующая лунка, куда укладывается очередной плод. Производительность до 100 плодов в минуту.
Машина РЗ-КРА для резки яблок осуществляет механическую ориентацию плодов, резку их на дольки и удаление сердцевины при производстве компотов. На каркасе 13 машины РЗ-КРА (рис. 44) закреплены ведущий вал 3 со звездочкой 15 и ведомый 14 наклонного цепного конвейера 2, рабочий орган которого образован из блоков роликов, и бункер 1 для приема плодов. На каркасе 12 закреплены валы — ведущий 7, ведомый 4 со звездочкой 76, привод 9, электрооборудование 5 и опоры 10. Валы 7 и 4 приводят в движение горизонтальный цепной конвейер, рабочий орган которого состоит из плит 17 с толкателями 18.
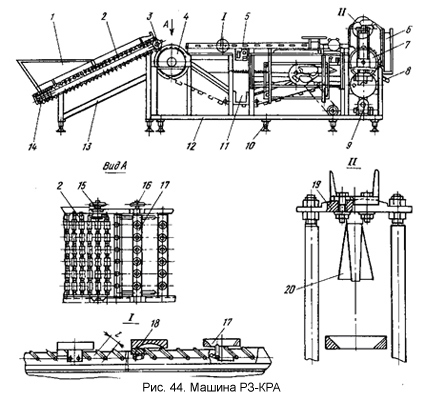
Плоды диаметром 55-75 мм и коэффициентом формы 0,7-1,1 засыпают в загрузочный бункер наклонного конвейера. При движении цепей его ролики приводят во вращение плоды. При этом они западают в пространство между соседними роликами и укладываются в ячейки плит горизонтального конвейера, где происходит их ориентация. Далее плоды проходят через подпружиненные двустворчатые ворота отсекателя. При этом ориентированный плод надежно удерживается держателем и фиксатором 19 и, преодолевая сопротивление подпружиненных ворот, проходит через них, а неориентированный плод не удерживается и, проваливается через зазор между плитами, скатывается по лотку 11.
Затем плоды поступают на операцию резания. При движении вниз ножи 20 входят в плоды не на полную их высоту, при обратном ходе плоды извлекаются из ячеек; при следующем рабочем ходе ножей сидящие на них плоды встречаются с плодами, уложенными в ячейках, и разрезаются. Дольки разрезанных плодов выносятся плитами конвейера и лотком 8, а сердцевина удаляется по лотку 6.
Машина А9-КАН предназначена для резания на дольки и удаления сердцевины яблок.
Яблоки из загрузочного бункера попадают в пространство между смежными роликами носителей и переносятся в гнезда носителей рабочего полотна. Яблоки размером до 55 мм проваливаются между роликами и по лотку выкатываются за пределы машины. Полотно машины транспортирует яблоки в зону резания. Работники, стоящие по обе стороны машины, вручную ориентируют яблоки в гнездах носителей, устанавливая их плодоножкой вверх или вниз.
Рабочее полотно от мальтийского креста получает прерывистое движение, при этом блок ножей движется возвратно-поступательно.
Движение рабочего полотна совпадает с движением блока ножей вблизи верхнего крайнего положения, а время движения рабочего полотна совпадает с временем опускания и подъема блока ножей в нижнем положении. При остановке яблока в зоне резания блок ножей опускается и разрезает его на дольки. Одновременно патроном-трубчатым ножом — вырезается сердцевина яблок и остается внутри ножа. Прижим для выравнивания плода препятствует застреванию долек между лезвиями во время подъема блока ножей. Сердцевина яблока проталкивается в трубку. При движении рабочего полотна дольки выпадают из гнезд и выводятся из машины.
Машина А9-КРВ «Р и т м» (рис. 45) предназначена для резки на кубики и столбики различных корнеплодов.
На сварной станине 1 установлен редуктор 10, к выходному фланцу которого крепится обойма 4 с барабаном 5 и режущими органами. Барабан насажен на выходной вал редуктора и представляет собой два стальных диска, между которыми установлены три лопасти 6. В нижней части обоймы укреплены неподвижный плоский нож 3 и гребенка 2 ножей продольного среза.
На выходной части первой ступени редуктора устанавливается угловая приставка, на вертикальный вал которой насажен ножевой диск 7 с ножами поперечного среза. К фланцу передней части обоймы приварен загрузочный бункер 5. В нижней части обоймы укреплен патрубок 9 для выгрузки нарезанного сырья.
В комплект запасных частей входит три сменные гребенки, ножи плоские, продольного и поперечного среза.
Продукт из бункера через отверстие во фланце поступает во вращающийся барабан, где ведется тремя лопастями и прижимается к стенкам обоймы под действием центробежных сил. Проходя над неподвижной режущей гребенкой, продукт надрезается в продольном направлении на глубину, равную высоте ножа. На ту же глубину, но в поперечном направлении продукт надрезается ножами, находящимися на диске. Надрезанный слой продукта срезается неподвижным плоским ножом, установленным на соответствующей высоте. Срезанные кубики падают в патрубок выгрузки.
При резке продукта на столбики достаточно снять ножевой лист. В этом случае продукт получит лишь продольный надрез гребенкой и срез слоя плоским ножом.
Машина А9-КИП (рис. 46) предназначена для резки овощей и фруктов на кубики, лапшу, ломтики и брусочки.
На сварной станине 15 установлен электродвигатель 13, при помощи клиноременной передачи сообщающий вращение приводному блоку, на вал которого насажен барабан 1, представляющий собой два диска с приваренными к ним четырьми лопастями 2. К неподвижной стойке 11 крепится неподвижный пластовый нож 5.
От шестерни приводного блока 12 получают вращение шпиндели поперечной и продольной резки, образующие режущий блок, который установлен на оси и легко может быть откинут из рабочего положения на стержень 10 для производства ремонтных или наладочных работ.
К центральному отверстию корпуса 14 барабана примыкает бункер 9, неподвижно укрепленный на станине. За шпинделем продольной резки на станине жестко смонтирован лоток 3 выгрузки.
Электрооборудование состоит из электродвигателя 13, магнитного пускателя ПМЕ-111, кнопочного поста управления ПКЕ-122-2У2, пакетного выключателя ПКВ-10-28-12, автоматического выключателя АЕ-2036, понижающего трансформатора ОСМ-0,063 и предохранителя ПРС-6УЗП.
Через ферромагнитный уловитель 8 и загрузочный бункер 9 сырье поступает во вращающийся барабан, увлекаемое лопастями и под действием центробежной силы прижимается к внутренней поверхности неподвижного корпуса. При прохождении сырья между декой 6 и пластовым ножом 5 происходит отрезание пласта от общей массы сырья. Толщина пласта регулируется изменением расстояния между подвижной декой и пластовым ножом посредством механизма 4. При дальнейшем перемещении пласт сырья попадает под ножи шпинделя поперечной резки, которые разрезают его на лапшу размером, определяемым конструкцией и частотой вращения шпинделя. Лапша, перемещаясь по поверхности держателя пластового ножа, попадает под дисковые ножи, в результате чего нарезается на кубики либо брусочки в зависимости от набора дисковых ножей в шпинделе продольной резки. Рабочее место обслуживающего персонала ограждено панелью 7.
Устройство А9-КЧГ предназначено для удаления кочерыг белокочанной и краснокочанной капусты в консервных цехах малой и средней мощности.
Устройство А9-КЧГ имеет сварной корпус; привод, включающий в себя двигатель, конический и червячный редукторы; механизм для поворота захватов на 120 ° с остановками. В верхней части вала расположен фланец, к которому прикреплены три захвата, расположенные под углом 120 Устройство имеет привод вращения и возвратно-поступательного (вверх-вниз) движения ножей.
Устройство работает следующим образом. На позиции загрузки оператор укладывает на нижний диск захвата кочан капусты кочерыгой вниз так, чтобы выступающая часть кочерыги вошла в отверстие диска, далее визуально при помощи зеркальной поверхности, расположенной под диском, ориентирует кочергу концентрично отверстию в диске. При повороте всей карусели захваты перемещают верхний и нижний диски навстречу друг другу и зажимают кочан сверху и снизу. Захват с зафиксированным кочаном, продолжая вращаться от позиции загрузки, повернувшись на 120 останавливается на позиции вырезки кочана, при этом ось кочерыги автоматически совмещается с осью ножа. Нож, приводимый, во вращение от редуктора, вырезает кочерыгу до тех пор, пока кулачок не опустит нож в исходное положение.
Стружка свободно падает в бункер под кочаном и вращающимся вместе в ножом ротором отбрасывается по лотку из машины.
После вырезки кочерыги захват поворачивается к позиции выгрузки. При движении в этом секторе диски разжимаются и свободно лежащий кочан на нижнем диске сбрасывается отражателем в лоток. При следующем движении зажим перемещается в позицию загрузки. В дальнейшем цикл повторяется.
Устройства для перемешивания. Устройства, применяемые в консервном производстве, имеют различные конструкции в зависимости от свойств перемешиваемых материалов. Наиболее . широко, используют пропеллерные и лопастные мешалки.
Пропеллерные мешалки характеризуются постоянно изменяющимся наклоном лопастей от 0° у оси вращения до 90 ° на конце лопасти. При вращении пропеллерной мешалки частицы жидкости отбрасываются во все стороны, что интенсифицирует процесс перемешивания. Это положительное свойство отличает пропеллерные мешалки от лопастных, имеющих лопасть с постоянным углом наклона ее поверхности к оси мешалки.
Лопастные мешалки обычно имеют частоту вращения 100-200 об/мин. Постоянный угол наклона лопасти приводит к образованию однонаправленного потока жидкости, что снижает эффективность перемешивания. Для исключения этого недостатка в сосуде устанавливают отражательные перегородки (волнорезы).
Тепловой аппарат с лопастной мешалкой показан на рис. 47. Привод расположен в верхней части аппарата. Он состоит из электродвигателя 1, клиноременной передачи 2 и червячного редуктора 3. На вертикальном валу 4 при помощи двух ступиц-втулок 6 укреплена якорная мешалка 5. Нижний конец вала закреплен в подшипнике 7, который опорами 8 прикреплен к днищу аппарата.
Экспериментально установлены зависимости для расчета необходимой мощности привода лопастных и пропеллерных мешалок (Вт):
- для турбулентного режима: N=230p-0,67μ1,67n1,33d1,66;
- для ламинарного режима: N= 0,84p0,95μ0,05n2,95d4,9;
где μ — вязкость жидкости Н*см/м2; n — частота вращения мешалки, с-1; d — диаметр мешалки, м; p — плотность перемешиваемой жидкости, кг/м3.
Мощность электродвигателя для привода мешалок принимается больше расчетной на 25% для лопастных мешалок и на 10-15% для пропеллерных. Для перемешивания густых масс используют фаршесмесители (рис. 48). Внутри полой чугунной станины 1 установлен электродвигатель 15, через зубчатую передачу 2 он приводит во вращение валы 5 z-образных лопастей. На этой же станине установлен электродвигатель 14, включением которого через два червячных редуктора 9 и 11 осуществляют опрокидывание корытообразной дежи 7 при опорожнении.
На станине установлены две тумбы 3 и 10, которые служат опорами для валов привода, лопастей и червячного редуктора 9. Дежа снабжена двустенной рубашкой 6 для подогрева продукта горячей водой. Дежа накрыта решеткой 4, которая своим весом включает контакт 8. Если крышка снята, контакт выключен и лопасти не могут быть включены. Магнитные пускатели размещены в ящиках 12 и 13. Частота вращения одной из лопастей на 10 об/мин больше, чем другой. Это обеспечивает интенсивность перемешивания.
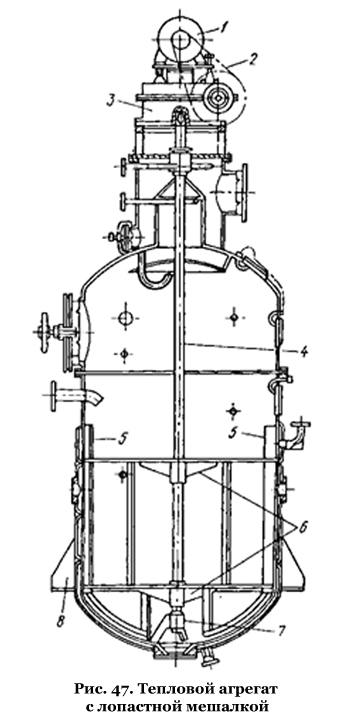
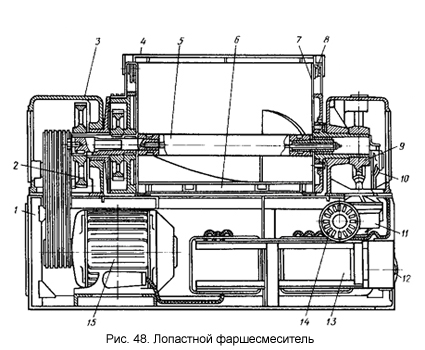
Производительность описанного фаршесмесителя (кг/ч) определяют по формуле, применяемой для аппаратов периодического действия,
Оборудование для фасования пищевых продуктов и укупоривания тары.
В консервной промышленности используют автоматы для фасования жидких, пюреобразных продуктов, а также продуктов, состоящих из двух компонентов (плоды в сиропе или зерно в заливе).
Различные физико-механические свойства продукта, разные требования к точности дозирования, а вследствие этого различная степень механизации и автоматизации обусловили создание фасовочных машин различных конструкций.
Производительность карусельного фасовочного автомата (шт/ч): Q=Mn, где M — число разливочных устройств автомата; n — частота вращений карусели автомата, мин-1.
Последовательность операций, выполняемых на карусельном автомате следующая:
- поступление порожней тары на нижний патрон карусели;
- подъем нижнего патрона или опускание фасовочного устройства;
- наполнение продуктом тары;
- опускание нижнего патрона или подъем фасовочного устройства;
- удаление наполненной тары.
Наполнительные и дозировочно-наполнительные автоматы. Для фасования гомогенных продуктов используются автоматы типа ДН. Примерная номенклатура продуктов, которые могут фасоваться в банки на наполнительных и дозировочно-наполнительных автоматах, приведена ниже.
Номенклатура продуктов для фасования на наполнительных автоматах типа ДН.
ДН1 — основные:
- сиропы для компотов;
- маринадные заливы;
- томатные заливы (до 12% сух. вещ-в);
- фруктовые, ягодные, овощные соки;
— дополнительные
- Соки с мякотью (фруктовые, ягодные и овощные);
- Растительные масла.
ДН2 — основные:
- фруктовые и овощные пюре (свыше 12% сух. вещ-в);
- растительные масла;
— дополнительные:
- фруктовые соусы
(до 23% сух. вещ-в);
- томатные соусы (до 23% сух. вещ-в);
- сгущенные молочные продукты;
- майонез;
- мясной паштет.
ДН3 — основные:
- фруктовые соусы (до 23% сух. вещ-в);
- томатные соусы (до 23% сух. вещ-в);
- сгущенные молочные продукты (молоко, кофе, какао);
- майонез;
- томатная паста и концентрированный томатный сок (до 40% сух. вещ-в);
- томатное пюре;
- овощная икра;
— дополнительные:
- повидло и джем в горячем состоянии, обладающие текучестью;
- мясной паштет.
Автомат наполнительный ДН1 предназначен для заполнения
свободного объема цилиндрических консервных банок жидкими пищевыми
продуктами вязкостью до 0,4 Н-с/м2. В соответствии с ГОСТом автоматы
выпускаются в следующих конструктивных исполнениях:
0 — для автономной эксплуатации, имеет собственный привод, транспортеры подачи и выдачи банок;
1 — для агрегатирования с закаточными машинами и не имеет собственного привода и транспортера выдачи банок;
2 — для автономной эксплуатации и имеет собственный привод, транспортеры
подачи и выдачи банок и изменяемое передаточное отношение шестерен.
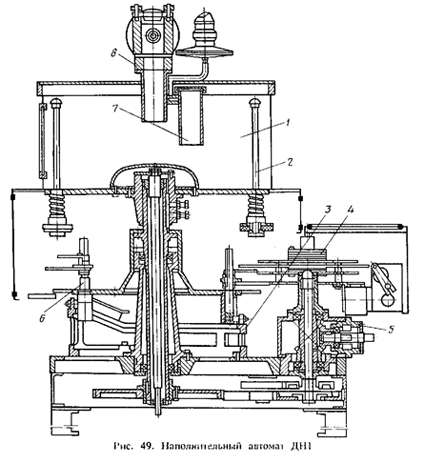
Обозначение типоразмера наполнительного автомата включает его
назначение, вместимость наполняемой тары, номинальную производительность
и конструктивное исполнение; например, ДН1-1-250-2 — обозначение
автомата, наполнительного для фасования жидких продуктов вязкостью до
0,4 Н-с/м2 в тару вместимостью до 1 дм3, производительностью 250
банок/мин и во втором конструктивном исполнении.
В отдельных заявочных ведомостях обозначение данного автомата ДН 1-1-250-2 в соответствии с ГОСТом указывается обозначением конструкторской
документации: Б4-КНП1-1.
Основными составными частями автомата ДН1 (рис. 49) являются станина,
дозирующее устройство 2, продуктовый бак 1, копир 3, продуктопровод 8,
регулятор подачи продукта 7, привод 5, электрооборудование.
Станина служит для установки всех узлов и деталей автомата. Механизм
приема 4 обеспечивает подачу банок на наполнение из неорганизованного
потока их либо с цехового конвейера (стеклянная и металлическая тара),
либо с течек (металлическая тара).
Пустые банки поступают на конвейер приемного устройства и подаются к
шнеку, который делит их по шагу и передает на приемную звезду, с которой
банки поступают на столики 6 карусели. При вращении карусели столики
вместе с банкой поднимаются по копиру и банка, упираясь в корпус патрона
дозирующего устройства, поднимает его. При этом продукт из бака
поступает в банку. При спускании банки прекращается подача продукта.
Наполненная банка передается на конвейер выдачи банок.
Автомат наполнительный ДН2 предназначен для объемного дозирования и
наполнения цилиндрических консервных банок пищевыми продуктами вязкостью
от 0,4 до 3,0 Н-см2.
Модификации конструктивного исполнения аналогичны автоматам типа ДН1.
Основными узлами автомата (рис. 50) являются станина 1, карусель 2 с
дозаторами, продуктовый бак, копир, продуктопровод, регулятор подачи
продукта, механизмы приема 3 и выдачи 4 банок, привод и
электрооборудование. Основной отличительной особенностью автоматов ДН2
от автоматов ДН1 является принудительная подача продукта в банку при
помощи поршней, движение которых управляется копиром.
Пустые банки поступают на конвейер приемного механизма и подаются к
шнеку, который делит их поток по шагу и передает на приемную звезду.
Звездой банки устанавливаются под дозаторы и, сохраняя свое положение
под ним, перемещаются при вращении карусели. При движении поршня копиром
вверх происходит подача продукта из бака в дозатор, при перемещении вниз доза
продукта поступает в банку. При отсутствии банки продукт поршнем
возвращается в бак.
Управление подачей продукта в банку осуществляется
клапаном, рычаг которого поворачивается наполняемой банкой.
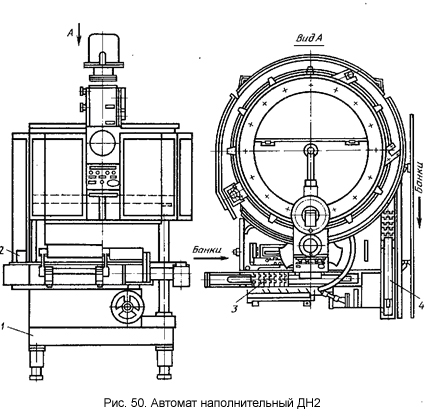
Наполненная банка выводной звездочкой передается на отводящий конвейер.
Автомат дозировочно-наполнительный ДН3 предназначен для объемного
дозирования и наполнения стеклянных и металлических банок пастообразными
пищевыми продуктами вязкостью от 3,0 до 8,0 Н • с/м2.
Модификации конструктивных исполнений автоматов ДН3 аналогичны таковым автоматов ДН1 и ДН2.
Основными составными частями автомата ДН3 являются: станина, дозирующее
устройство, продуктовый бак, копир, продуктопровод, регулятор подачи
продукта, регулировочный винт, механизм приема, привод и
электрооборудование.
Основным отличительным узлом данного типа наполнителей является дозатор.
Он предназначен для дозирования по объему и выдачи сформированной дозы в
банку. Доза продукта формируется при ходе поршня вниз. При этом
отверстие в днище бака открыто и продукт свободно попадает в
надпоршневое пространство. Поршень перемещается с помощью привода,
имеющего шток с роликом, который, обкатываясь по копиру, перемещает шток
вверх или вниз. Выдача дозы в банку происходит при ходе поршня вверх.
При этом клапан поворачивается блокировочным устройством. При отсутствии
банки блокировочное устройство не поворачивает клапан и продукт при
ходе поршня вверх возвращается обратно в бак.
Принцип работы автомата ДН3 такой же, как автомата ДН2.
Автомат дозировочно-наполнительный Б4-КДН-16 предназначен для
фасования зерна зеленого горошка и заливы в стеклянные и металлические
консервные банки.
Автомат Б4-КДН-16 представляет собой вертикально-ротационную машину
непрерывного действия и включает следующие основные узлы: карусель,
питающее устройство, станину, четыре опоры, бак, привод, блокировочные
устройства и электрооборудование.
Подача горошка к дозировочному устройству осуществляется из бункера. В
нижней части его имеется роликодержатель с роликом, который посредством
пружины прижимается к кулаку вытряхивания из бункера.
Внутри бака для заливы находится поплавок, перемещающийся по трубе. В
нижней части поплавка имеется планка с резиновым кольцом, служащим для
запирания трубы в верхнем положении поплавка. Для автоматического
включения и выключения подачи заливы в банку имеется клапан,
закрепленный на банке. Он состоит из системы рычагов, обеспечивающих с
помощью пружины запирание резиновым кольцом отверстия в корпусе для
подачи продукта в бункер, и электромагнита. Запирание отверстия подачи
продукта в бункер заливы осуществляется при отсутствии подпора банок на
входе в машину и при отсутствии заданного уровня заливы в баке.
Порожние банки по конвейеру поступают к шнеку механизма приема. Шнек
делит их поток по шагу и выдает на приемную звезду, которая
устанавливает их в гнезде центральной звезды карусели. Она перемещает
банки по столу-копиру. Горошек попадает в бункер и заполняет проходящие
под ним дозирующие стаканы. В это время выход из дозирующих стаканов
закрыт заслонками. Для лучшего заполнения дозирующих стаканов бункер
встряхивается.
При дальнейшем движении по столу-копиру банки поднимаются к заслонкам,
которые рычагом блокировки отводятся, открывая дозаторы, и продукт из
дозаторов высыпается в банки. Далее банки попадают в зону заполнения их
заливой. Количество поступающей в банку заливы регулируется вентилем в
зависимости от производительности машины и величины дозы. Из бака залива
через клапан поступает в бункер, установленный свободно на вращающемся
диске с дозаторами, а из бункера — через открытые дозаторы в банку.
При дальнейшем движении банки выдающей звездой перемещаются на выдающий
конвейер и далее на закаточную машину. Затем ролик поворачивает заслонку
и закрывает ею дозатор.
По конструктивным особенностям автомат Б4-КДН-16 выпускается в следующих модификациях:
I — с самостоятельным приводом без выдающего конвейера для доз320-570 см3;
II — с самостоятельным приводом с выдающим конвейером для доз 650- 1000 см3;
III — с самостоятельным приводом с выдающим конвейером для доз 320-570 см3;
IV — с самостоятельным приводом без выдающего конвейера для доз 650-1000 см3.
Автоматический наполнитель плодов типа 1527, (системы Вязовского)
предназначен для равномерной укладки сравнительно мелких (диаметром до
35 мм) плодов в стеклянные или металлические банки вместимостью 500-1000 см3.
Автомат типа 1527 (рис. 51) состоит из дозирующего барабана 1, пружины 2
для фиксации заслонок 5 и 13, мерных цилиндров 3 и 6, наклонных дисков
4, вертикального стержня 7, щупа 8 для банок, электродвигателя 9, стола
10, центрирующей звезды 11, хвостовика 19 с роликом, упора 18 для
регулирования отклонения стрелки 17. Над барабаном 1 расположен бункер, в котором имеется щетка 16 для сбрасывания в нижнюю часть бункера плодов, находящихся в верхней части наклонного бункера.
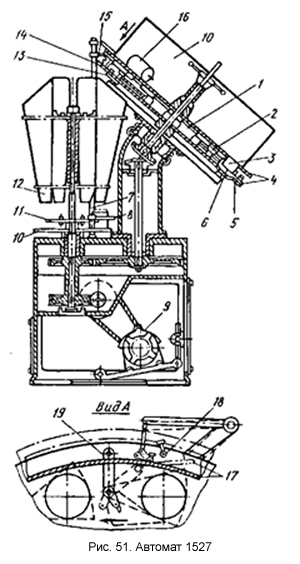
В нижней части наклонного барабана плоды заполняют телескопические
мерные стаканы и при дальнейшем вращении барабана поднимаются вверх, при
этом щетка сбрасывает лишние плоды из мерных стаканов.
Пустая банка, поступившая под одну из воронок 12, посредством щупа 8 и
связанного с ним механизма открывает заслонку, наполняется плодами из
мерного цилиндра через воронку. При дальнейшем движении барабана
заслонка возвращается в исходное положение. При отсутствии банки
заслонка не открывается. Вращение барабана и карусели с воронками
осуществляется синхронно. Наполненные плодами банки отводящим конвейером
подаются к автомату-наполнителю сиропом или заливой. Настройка
автомата на разные размеры банок осуществляется подъемом или опусканием
карусели с воронками по направляющей 14 тягой 15.
Машины для герметизации тары. Одним из основных требований при
производстве консервов является создание герметичной укупорки тары с
продуктом.
В настоящее время в мировой практике имеются различные способы
укупоривания стеклянных банок и повсеместно используется один способ
укупоривания металлических банок так называемым «двойным швом».
Банка (рис. 52), прижимаемая нижним патроном к верхнему патрону 2,
фиксируется таким образом, чтобы рабочая поверхность закаточного ролика 1
находилась против фланцев банки и крышки 3. Радиальное перемещение
закаточного ролика к вращающейся банке или вращение группы роликов в
радиальном направлении к банке обеспечивает подвивание фланцев банки и крышки.
Весь процесс герметизации происходит за две операции: первая — положение а, вторая — положения б и в. (На рис. 52 показаны корпус 4 банки и
закаточный ролик 5 второй операции). В консервной промышленности
используются стеклянные банки с номинальной вместимостью от 100 до 10
000 см3.
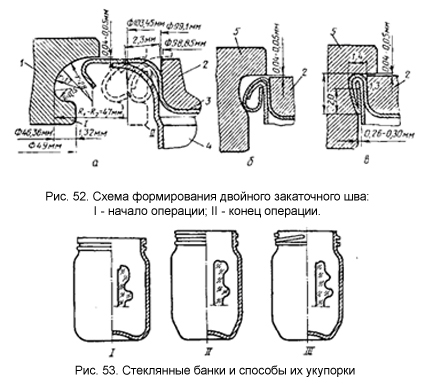
Венчики горловины банок в зависимости от способа укупорки изготовляются
различных типов:
I — обкатной, представляет собой широко распространенный в нашей стране способ
укупорки СКО (стеклянная консервная обкатная банка),
II — обжимной, довольно широко
распространенный в других странах тип укупорки Евро— кап,
III — резьбовой (рис. 53) —
Евро-твист или Твист-офф.
Для герметизации банок с продуктом применяют автоматические и
полуавтоматические закаточные (для металлических банок и стеклянных
банок I типа) и укупорочные (для стеклянных банок II и III типа) машины.
Закаточные машины для консервной промышленности выпускают следующих
типов:
- ЗК1 — автоматические для стеклянной тары;
- ЗК2 — автоматические вакуумные для стеклянной тары;
- ЗКЗ — автоматические для стеклянной тары для агрегатирования с наполнителем;
- ЗК4 — полуавтоматические для стеклянной тары;
- ЗК5 — автоматические для наполненной металлической и комбинированной тары;
- ЗК7 — автоматические для цилиндрической металлической тары для агрегатирования с наполнителем;ЗК8 — полуавтоматические для металлической и комбинированной тары.
Обозначение закаточной машины складывается из обозначения типа ее,
номинальной вместимости обрабатываемой тары в литрах и номинальной
производительности в банках в минуту. Например, типоразмер ЗК2-1-125
обозначает автоматическую вакуумную закаточную машину, предназначенную
для герметизации стеклянных банок вместимостью до 1 л,
производительностью 125 банок в минуту.
Номинальная производительность автоматических машин определяется по следующим формулам:
- для машин дискретного действия (однопозиционные) — Q=1/T, где Т — продолжительность обработки одной банки, мин;
- для машин непрерывного действия — Q=nz, где n — частота вращения ротора, мин-1 ; z — количество банок, выдаваемых машиной за один оборот ротора.
Величины Т и z определяют как средние результаты пятиминутного замера с учетом погрешности числа оборотов вала электродвигателя.
Номинальную производительность полуавтоматических машин следует определять как среднее за 1 мин количество закатанных банок наибольшей вместимостью в течение 1 ч.
Ниже рассматриваются конструкции отдельных закаточных машин, изучение которых даст представление о всех типах машин.
Закаточные машины ЗК1-1-125 и 3K1-3-63 (табл. 10) предназначены для закатывания стеклянной тары. По конструкторской документации машина ЗК1-1-125 производительностью 150 банок/мин имеет обозначение Б4-КЗК-109 и машина 3K1-3-63 производительностью 80 банок/мин — Б4-КЗК-110.
Техническая характеристика закаточных машин |
Показатели |
ЗК1-1-125 |
3K1-3-63 |
Производительность, банок/мин
номинальная
дополнительная |
125
80,100,160
|
63
40,50,80
|
Диапазон размеров
обрабатываемых банок, мм
диаметр
высота |
60-105
60-165
|
90-155
160-240
|
Установленная мощность
двигателя, кВт |
2,2
|
Габариты, мм
|
2350x1000x2060
|
2350x1060x2150 |
Масса, кг
|
1650
|
1760
|
Составными частями машины ЗК1-1-125 (рис. 54) являются станина, механизмы приема, подачи и закатывания банок, выбросная звездочка, плита с пультом управления, коробка скоростей 2 и электродвигатель 1.
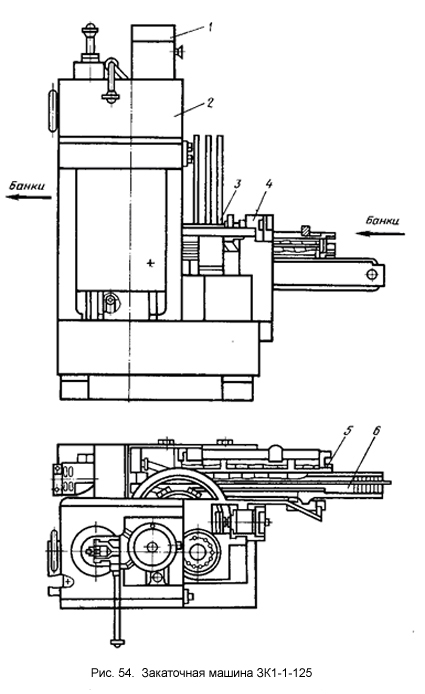
Механизм приема банок состоит из конвейера 6, шнека 5 и блокировочного механизма, который не выдает крышку при отсутствии банки. Механизм подачи предназначен для транспортирования с одновременной ориентацией относительно друг друга банок и крышек и подачи их на подвижной стол закаточного механизма, состоящего из подающей звезды, направляющей для крышек, магазина крышек 3 и маркиратора 4.
Закаточная карусель имеет четыре вращающихся шпинделя с закаточными узлами, каждый из которых состоит из оси, рычагов, закаточных и отжимных роликов.
Наполненные банки поступают из механизма приема. На конвейере при прохождении шнека банка отжимает рычаг блокировки, после чего магазин выдает крышку, которая маркируется, и банка звездой-носителем подается в закаточную карусель. Здесь на банку надевается крышка, банка с крышкой устанавливается в патрон закаточного механизма и закатывается.
Закатанная банка снимается с патрона и выдается из машины выбросной звездочкой.
Полуавтоматические закаточные машины 3K4-3-16 и ЗК4-10-12 (соответственно по конструкторской документации Б4-КЗК-77 и Б4-КЗК-77-01) предназначены для закатывания стеклянной тары вместимостью до 3,0 и 10,0 л; полуавтоматические закаточные машины ЗК8-5-16 и ЗК8-10-12 (соответственно по конструкторской документации Б4-КЗК-77-02 и B4-K3K-77-03) предназначены для закатывания металлической тары вместимостью до 5 и 10 л.
Полуавтоматическая одношпиндельная закаточная машина 3K4-3-16 (Б4-КЗК-77) имеет следующие основные узлы (рис. 55): станину, привод, включающий в себя клиноременную передачу 15, электродвигатель 16, закаточную головку, нижний патрон.
Закаточная головка, состоит из наружного вала-шестерни 14, кулака 13, отжимных роликов 12, полых валов 8 и 10, планшайбы 9, роликодержателя 11, закаточных роликов 7 верхнего патрона 6, выталкивателей 5 со штоком.
Нижний патрон служит для подъема, центрирования и прижатия банок к верхнему патрону и состоит из стола 4 на штоке 3, кулака 18, вала 17 и вилки 2.
При нажатии на педаль 19 включается однооборотная муфта, при этом закаточная головка совершает 11 оборотов. Банка с надетой на нее крышкой поднимается к закаточной головке и укупоривается. Нижний патрон с укупоренной банкой опускается, и после этого банку снимают вручную.
Автоматические закаточные машины ЗК5-1-250 и 3K5-5-63 представляют собой автоматы, предназначенные для закатывания, маркирования и счета наполненной цилиндрической металлической и комбинированной тары и выдачи ее на неподвижный стол.
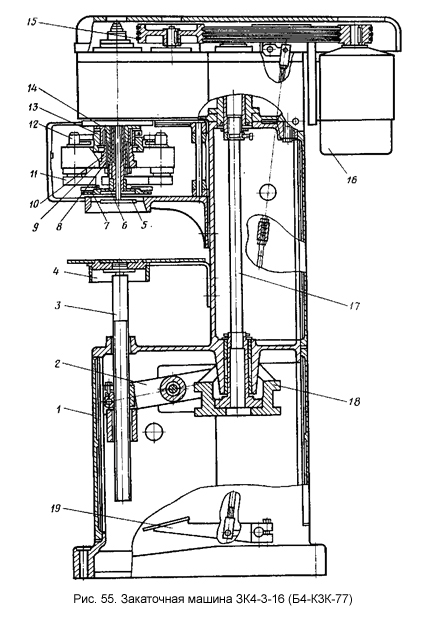
Составными частями машины ЗК5-1-250 являются станина, механизм приема, механизм подачи, закаточная карусель, выбросной механизм, пульт управления, коробка скоростей и электрооборудование.
Аналогичную конструкцию имеет закаточная машина 3K5-5-63, которая относится к семейству автоматов карусельного типа непрерывного действия.
Принцип работы закаточных машин ЗК5-1-250 и 3K5-5-63 одинаков и заключается в следующем. Наполненные банки поступают на механизм приема. На конвейере при прохождении зоны шнека банка отжимает рычаг блокировки, после чего механизм выдает крышку, которая маркируется, и в дальнейшем банка подается в закаточную карусель. В закаточной карусели на банку надевается крышка, собранная банка с крышкой устанавливается в патрон закаточного механизма и закатывается. Закатанная банка снимается с нижнего патрона и выбросной звездочкой выводится из машины.
Закаточные машины ЗК7-1-160-2 и ЗК7-1-250 (по конструкторской документации их обозначение Б4-КЗК-84, рис. 56) предназначены для маркировки крышек, укупорки под вакуумом и счета наполненных продуктом цилиндрических жестяных консервных банок. Они являются вертикальными роторными автоматами непрерывного действия.
На машинах выполняются следующие основные операции: прием банок, выдача крышек из магазина 7, маркировка крышек маркиратором подача банок и крышек к ротору предварительного закатывания (клинчеру), установка крышки на банку, установка банок в патрон клинчера, клинчерование (негерметичное соединение банки с крышкой), съем с патрона, передача банок от клинчера к вакуумирующему устройству, вакуумирование банок (первичное шлюзование), подача банок к закаточному ротору, установка банки в патрон, закатывание (герметичное соединение банки с крышкой), съем с патрона, вторичное шлюзование, съем банок, выдача банок выдающей звездой 3 на отводящий конвейер 2.
Машина состоит из станины У, механизма приема банок, механизма подачи, ротора, вакуум-системы с насосной установкой 9, закаточной карусели, привода (электродвигатель 5, клино-ременная передача 4, коробка скоростей 6), а также отводящего конвейера, электрооборудования.
Механизм приема обеспечивает прием банок и распределение их потока по шагу. Одновременно поворачивается рычаг блокировки механизма выдачи крышки.

Механизм подачи предназначен для транспортирования с одновременной ориентацией относительно друг друга банок и крышек ц подачи их на стол закаточного механизма. Механизм подачи имеет накопитель крышек. В корпусе магазина вращаются три отсекателя со шнеками, которые обеспечивают выдачу крышки для маркирования и закатывания.
Вакуумная система состоит из насосной установки, вакуум-камеры, вакуум-клапана, механизма шлюзования, контрольной и сигнальной аппаратуры.
Дозировочно-закаточные агрегаты Б4-КАД созданы для обеспечения синхронности работы наполнителей с закаточными машинами. Они предназначены для наполнения продуктами различной вязкости металлических, цилиндрических и стеклянных консервных банок и их закатывания.
Эти автоматы выпускаются трех модификаций: Б4-КАД-1; Б4-КАД-2; Б4-КАД-3, различающихся производительностью.
Описания отдельных машин агрегатов типа Б4-КАД приведены при рассмотрении конструкций дозировочно-наполнительных автоматов типа ДН и закаточных машин типа ЗК.
Особенностью этих агрегатов, является привод от одного электродвигателя, что обеспечивает синхронность движения банок от наполнительной карусели к закаточной.
На рис. 57 показан общий вид агрегата Б4-КАД-1 для случая, когда наполнительный автомат 2 (ДН 1-2-250-1) и закаточная машина 3 (ЗК8-1-250-02) объединены. Обе машины смонтированы на общей раме 1 и соединены между собой карданным валом 4.
Автомат укупорочный паровакуумный Б4-КУТ-1 предназначен для укупорки специальных консервных банок с венчиком II типа с одновременным заполнением подкрышечного пространства сухим паром с целью создания в банках разрежения.
Автомат Б4-КУТ-1 (рис. 58) состоит из следующих основных узлов: станины 1, механизма укупоривания 2, механизма подачи 7 с направляющей и магазином крышек 6, выбросной звезды, коробки скоростей 4, привода 5, пароперегревателя 5, пульта управления 3. Станина является базой, на которой смонтированы все механизмы.
Подаваемый конвейером 9 поток банок шнеком распределяется по шагу и приемной звездой направляется на карусель.
Перемещаясь по приемному механизму, банка воздействует на щуп и подает команду на включение однооборотной муфты (привода магазина крышек 6). Специальным механизмом крышка ориентируется над горловиной банки. При дальнейшем перемещении банки с крышкой в подкрышечное пространство и в банку из коллектора подается вначале насыщенный, а затем перегретый пар.
При переходе банки на поджимной стол карусели последний поднимается,
перемещая банку вверх к крышке. В это же время толкователь укупорочного
патрона опускается и в месте передачи банки со звезды на карусель
прижимает крышку к банке — происходит надевание крышки на банку.
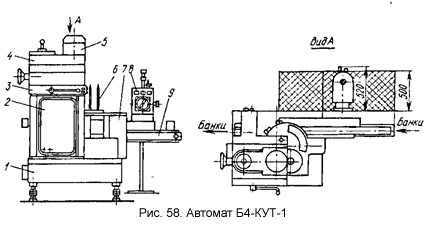
При дальнейшем подъеме поджимного стола банка с крышкой подводится к укупорочному патрону и вводится в его заходную часть. Тем же перемещением стол последовательно вводит банку с крышкой в укупорочную часть патрона — происходит укупоривание банки обжимом.
После этого подвижной стол с укупоренной банкой, сопровождаемой толкателем, опускается, банка снимается со стола выбросной звездой и по выбросному столику выводится из автомата.
Автомат укупорочный паровакуумный Б4-КУТ-2 предназначен для укупоривания специальных консервных банок с венчиком горловины III типа с одновременным заполнением подкрышечного пространства сухим паром с целью создания в банках разрежения.
Автомат Б4-КУТ-2 состоит из станины, на которой смонтированы все узлы машины: механизм приема банок, механизм подачи с механизмом поштучной выдачи крышек и направляющими этих крышек, укупорочный ротор и выбросная звезда с приводом.
Основным узлом является укупорочный ротор (рис. 59). Карусель 17 имеет центральный вал 10 с шестерней 16, через который передается вращение на ротор. Шпиндель 9 предназначен для передачи вращения на укупорочный патрон 7 через муфту 5 предельного момента.
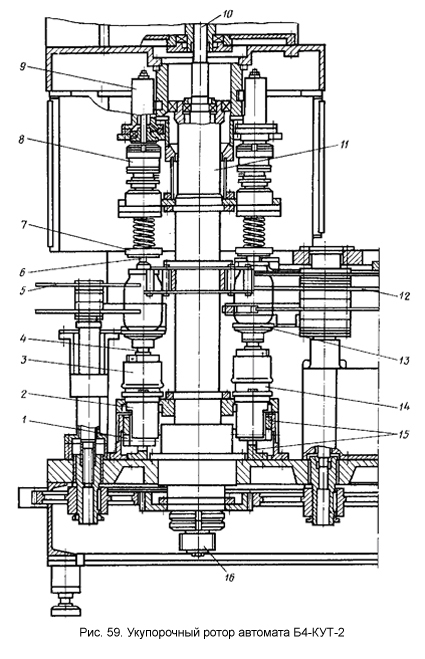
Укупорочный патрон представляет собой стакан с фланцем и шлицевым отверстием. Посредством шлицев патрону передается вращение. Выталкиватель 6 служит для удержания крышки при надевании ее на банку и для выталкивания укупоренной банки из патрона.
Поджимной стол состоит из штока 4 и ползуна 2, смонтированных в корпусе 14. Шток имеет в верхней части вращающийся в подшипниках фланец 13 с тарелкой.
На ползуне закреплена ось 1 с роликами, взаимодействующими с копирами 15, что обеспечивает возвратно— поступательное вертикальное перемещение поджимного стола 3.
Механизм подачи состоит из привода, направляющих для крышек, механизма подачи крышек, конвейера подачи крышек и вибробункера.
В корпусе механизма подачи размещены шестерни, передающие вращение звезде 12. Выбросная звезда 5 с приводом установлена на станине и предназначена для удаления укупоренных банок из машины.
Процесс работы автомата заключается в следующем.
Наполненные продуктом банки шнековым питателем распределяются по шагу и рычагом блокировки подают сигнал для выдачи крышки. Приемной звездой банка перемещается на поджимной стол укупорочного ротора с одновременной передачей на нее крышки. По пути перемещения банки и крышки из пространства между крышкой и верхним уровнем продукта в банке сухим паром вытесняется воздух. Кроме того, под крышку отдельно подается насыщенный пар для создания благоприятных условий завинчивания крышки на банку.
В месте перехода с подающей звезды в укупорочный ротор банка входит своим венчиком в крышку, при этом последняя оказывается зависшей на нижней магнитной плоскости выталкивателя.
В укупорочном роторе банка вместе с крышкой поднимается к патрону.
Сначала в укупорочном роторе крышка и банка вращаются одна относительно другой в сторону отвинчивания (происходит процесс центрирования), а затем эти относительные движения происходят в сторону завинчивания. Банка приводится во вращение неподвижными направляющими, крышка — укупорочным патроном, приводимым во вращение сначала внешней, а затем внутренней дугой. При завершении укупоривания банка удаляется из автомата выбросной звездой.
Этикетировочные машины. Наклеивание этикеток на консервные банки с готовой продукцией является одной из последних технологических операций.
Этикетировочные машины можно разделить на две основные группы: линейные и карусельные.
В машинах линейного типа банки в горизонтальном положении перемещаются поступательно, вращаясь вокруг своей оси. В карусельных машинах банки в вертикальном положении перемещаются по дуге окружности карусельного автомата.
Линейная этикетировочная машина КЭ-4 работает следующим образом (рис. 60).
По наклонному загрузочному лотку 1 банки скатываются к резиновому ролику 2, пропускающему их через равные интервалы времени к механизму перемещения 3, который представляет собой два бесконечных клиновых ремня, огибающих ведущие и ведомые шкивы. Ремни прокатывают банки над клеевым устройством 4 и 5.
В этикетировочных машинах этикетка охватывает весь корпус металлической банки с переходом одного конца этикетки на другой, поэтому она относительно прочно удерживается на корпусе.
Клей наносится на банку в виде двух полосок при помощи обрезиненных роликов 6, соприкасающихся с барабаном, вращающимся в клеевой ванне. Толщина слоя клея регулируется скребком, перемещаемым микрометрическим винтом.
В дальнейшем через полный оборот банка захватывает смазанными клеем местами этикетку из магазина 7. Далее банка наматывает этикетку на себя. Свободный конец этикетки, предварительно смазанный клеем из капельницы, расположенной поперек магазина, попадает уже на приклеенный конец этикетки. После этого банка прокатывается между ремнем механизма перемещения 3 и прокладкой 8 из губчатой резины. Этикетка разглаживается и плотно прижимается к корпусу банки. На отводящем лотке банка нажимает на педаль, рычажно связанную с шестеренчатым насосом, подающим порцию клея в капельницу.
По мере расхода этикеток магазин поднимается автоматически при прокатывании банок.
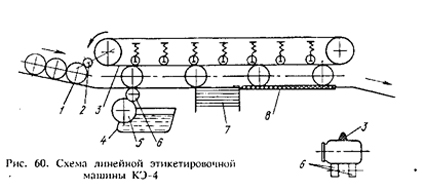
Скорость перемещения банок в машине равна половине линейной скорости транспортирующих клиновых ремней. На основании этого производительность (банок/ч) этикетировочной машины линейного типа с горизонтально перемещающимися банками определяется по формуле, справедливой для фрикционных транспортеров:
Этикетировочный автомат ВЭМ (рис. 61) предназначен для наклеивания этикеток на цилиндрическую часть бутылок, перемещаемых в вертикальном положении. Производительность автомата 3000-6000 бутылок в час. На этом автомате могут обрабатываться бутылки вместимостью от 0,25 до 0,8 л. Переход с одного размера бутылок на другой осуществляется путем смены транспортирующих механизмов на заводе. Обычно заводы приобретают несколько автоматов на разные виды бутылок, так как переоборудование автоматов в условиях консервного цеха сложно.
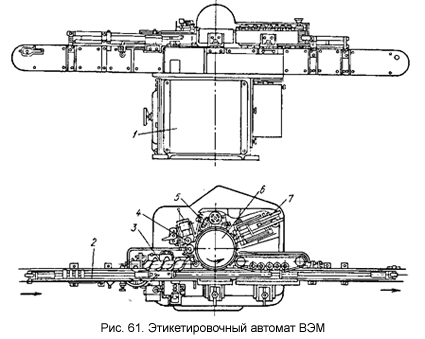
Этикетировочный автомат ВЭМ линейного типа наклеивает этикетки на бутылки методом накатки. В качестве переносчика этикеток служит вращающийся вакуумный барабан.
Внутри пустотелой литой станины установлены привод машины и вакуумный насос с индивидуальным электродвигателем. На станине У расположены: пластинчатый конвейер 2 для бутылок; шнековый распределитель потока 3; вакуумный барабан-этикетопередатчик 6 с шестью сегментами, в которых сделаны отверстия — присосы для этикеток; магазин этикеток 7 с механизмом качения, механизмом 5 для нанесения даты для этикетки; клеевой механизм 4; накатный конвейер.
Поступающие по конвейеру бутылки перемещаются шнеком по касательной к вакуумному барабану и по пути нажимают последовательно на щупы, отчего разрывается электрическая цепь одного, затем другого электромагнита блокировки «Нет бутылки — нет этикетки». При этом запирающий штырь электромагнита освобождается и под действием собственного веса отклоняется вниз, выключая привод этикетного механизма. От действия механизма магазин этикеток перемещается вперед, а закрепленный на его корпусе ролик нажимает на клапан золотника. При этом этикетка из магазина присасывается к сегменту вакуумного барабана.
При дальнейшем движении этикетки с барабаном на нее ставится дата и затем наносится клей. Если на сегменте отсутствует этикетка, то щуп опускается во впадины на сегменте и выключает механизм нанесения клея, что исключает загрязнение сегмента.
В момент соприкосновения этикетки с бутылкой клапан золотника соединяет вакуумное пространство с атмосферой, этикетка отделяется от сегмента и приклеивается к бутылке. После этого бутылка попадает в накатный конвейер, вращается вокруг своей оси и этикетка разглаживается.
Производительность этикетировочного автомата (бутылок/ч): Q=60nzφ, где n – частота вращения вакуумного барабана, об/мин; z – количество гнезд на транспортирующей звезде; φ – коэффициент использования теоретической производительности.
Карусельные этикетировочные машины применяют наряду с машинами линейного типа. Наиболее широко их используют для наклейки этикеток на бутылки с соком и напитками и на банки вместимостью 0,25-0,35 л. На рис. 62 показана типовая схема такой машины с колеблющимся этикетопередатчиком. Банки вводятся приемным конвейером 1. Звездой 2 они по одной подаются на карусель 4, где подхватываются толкателями 3 и перемещаются по дуге к этикето-передатчику 5, который к моменту подхода банки становится на пути ее
движения. Между пластинками этикетопередатчика находится этикетка 6,
приклеенная концами к передатчику. В момент подхода банки к этикетке
прижим 7, движущийся по копиру, прижимает центр этикетки к подошедшей
банке. В таком положении прижим удерживает этикетку на банке до тех пор,
пока специальные щетки либо ролики не прижмут концы этикетки, смазанные
клеем, к банке. Далее прижим отходит и банка звездочкой 8 передается на
отводящий конвейер 9. Освободившись от этикетки, этикетопередатчик 5
движется к магазину этикеток 10. По пути пластины этикетопередатчика
смазываются клеем при помощи вращающегося клеевого валика 11.
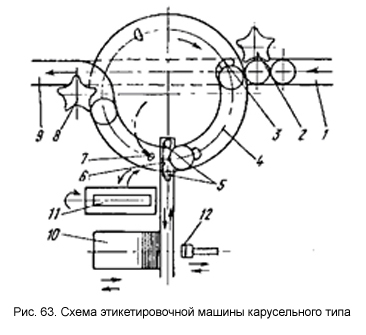
В крайнем положении напротив магазина этикеток передатчик останавливается, на его пластины наклеивается этикетка и наносятся дата и шифр на оборотную сторону с помощью механизма 72. Затем этикетопередатчик снова устанавливается на пути движения банок и описанный цикл повторяется.
Автомат этикетировочный Б4-КЭМ-2 из серии карусельных машин предназначен для наклеивания этикеток на цилиндрическую часть стеклянных банок, наполненных продуктом. Он входит в состав автоматизированных и автоматических линий по оформлению готовой продукции в стеклянной таре.
Автомат Б4-КЭМ-2 (рис. 63) состоит из нижней 2 и верхней 1 станин, конвейера 5, приемной и выбросной звезд, клеевого механизма 6, магазина этикеток 7, маркиратора плиты 3 и привода.
Банки, предназначенные для этикетирования, поступают на конвейер автомата, который подает их к шнеку. Шнек расставляет банки по шагу, после чего они поступают в приемную звезду, которая устанавливает их на столики вращающегося ротора. Патроны, опускаясь под действием кулака, зажимают и центрируют банки. Вращение их осуществляется от нижних столиков. Полоски клея наносятся на банку движущимися ремнями клеевого механизма.
При дальнейшем движении ротора банка, прокатываясь без скольжения по находящейся в магазине передней этикетке, наворачивает ее на себя. При этом наносится клей на задний конец этикетки. Затем банка без скольжения прокатывается по резиновой подушке обкатного устройства, происходят разглаживание и фиксация этикетки на банке.
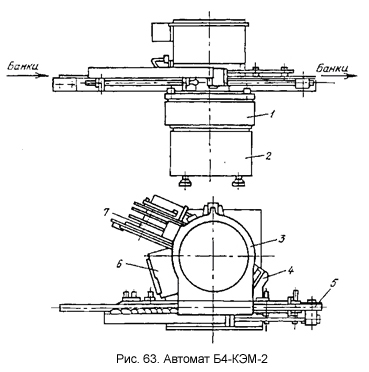
Далее банка подходит к маркиратору и на свободное белое поле этикетки наносятся маркировочные знаки. После этого банка освобождается от зажима и выбросной звездой передается на конвейер автомата. С него банка поступает на транспортные устройства линии.
Производительность карусельной этикетировочной машины рассчитывают так же, как и этикетировочного автомата. |