Технологические процессы плодоовощной промышленности различают по физической сущности, конструктивному исполнению, способу управления и т. п. По этим признакам их можно разделить на следующие виды:
- процессы переработки различных материалов, происходящие в соответствии с законами материального и энергетического баланса;
- транспортные процессы;
- энергетические процессы: выработка, преобразование и передача различных видов энергии;
- процессы сбора, обработки и передачи информации. Другим квалификационным признаком технологических процессов, существенным для автоматизации, является агрегатное состояние вещества. По этому признаку определяются группы процессов с общими для них типовыми схемами автоматизации (например, системы управления потоками жидкостей, газов, твердых, сыпучих, волокнистых, пастообразных и сложных материалов).
Пользуясь квалификационными признаками, можно выделить следующие типовые технологические процессы:
- механические процессы: перемешивание, транспортировка, дозирование, измельчение, смешивание, сортирование, инспекция и т. п;
- гидродинамические процессы: перемешивание жидкостей, разделение газовых и жидких неоднородных смесей, перемешивание материалов;
- тепло- и массообменные и термодинамические процессы без изменения агрегатного состояния вещества: сжатие, разрежение, нагревание, охлаждение, фильтрование и т. п.;
- тепло-и массообменные (диффузионные) процессы с изменением агрегатного состояния вещества: разделение газовых смесей, экстрагирование, выпаривание, конденсация, дистилляция, сушка и т. п.;
- химические процессы: окисление, ароматизация, сульфитация, нейтрализация и т. п.;
- микробиологические процессы: приготовление и хранение питательной среды, брожение, стерилизация и т. п.
В некоторых аппаратах протекают однотипные технологические процессы, описываемые одними и теми же зависимостями между параметрами. Для одного типового процесса в наиболее распространенной конструкции аппарата может быть разработано решение по автоматизации. Такое решение носит название типового. В некоторых случаях в установках протекают процессы, подчиняющиеся различным законам, например перемешивание с изменением агрегатного состояния материала — кристаллизация сахара из растворов с перемешиванием и выпариванием.
Типовые технологические процессы, подчиняющиеся различным законам, в большинстве случаев описываются дифференциальными уравнениями в частных производных.
Выбор системы управления типовыми технологическими процессами основан на принципиальном упрощении их физической сущности. Такое упрощение, связанное с пренебрежением фактора распределенности параметров процесса и рассмотрением как объекта с сосредоточенными параметрами, как правило, вполне допустимо и дает положительные результаты.
Автоматизация того или иного технологического процесса может осуществляться различными способами путем использования разнообразных средств автоматики, различающихся свойствами, назначением, принципом действия, конструктивным оформлением, точностью, надежностью и другими показателями.
Автоматическое регулирование.
Автоматическое регулирование — это область автоматики, обеспечивающая в ходе какого-либо технологического процесса поддержание физических величин в заданных пределах или изменение их по заданному закону. Величины, которые во время работы технологических агрегатов необходимо поддерживать на заданном уровне или изменять по определенному закону, называются регулируемыми параметрами. Автоматическое регулирование основано на использовании двух принципов:
- регулирование по отклонению параметра от заданного значения;
- регулирование по причине, вызывающей отклонение параметра от заданных значений.
Преимущество имеет первый принцип, так как эффективных причин, вызывающих отклонение параметров, может оказаться несколько, поэтому потребуются дополнительные средства автоматизации и использование такого принципа может оказаться неэффективным.
На рис. 121 показана схема ручного регулирования температуры в подогревателе. Полупроводниковый термометр сопротивления ТС находится внутри прибора и включен в одно из плеч схемы моста М.
В одну из диагоналей схемы включен источник электрической энергии, а в другую — чувствительный показывающий прибор ПП со шкалой, проградуированной в градусах температуры. При отклонении температуры от заданной изменится сопротивление термометра ТС, нарушится равновесие моста, отклонится стрелка показывающего прибора и рабочий, регулируя степень открытия клапана К, будет изменять доступ пара в нагревательную камеру до тех пор, пока не восстановится показание прибора. На рис. 122 показана схема системы автоматического регулирования для этого же процесса.
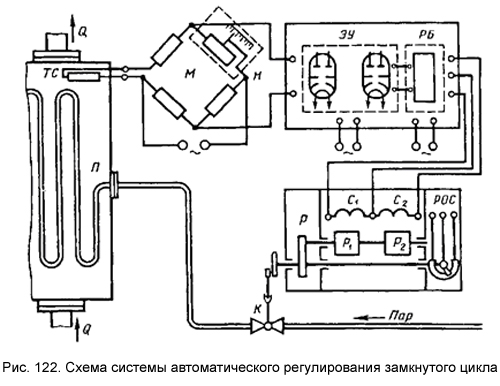
В данном случае мост М питается переменным током. Роль человека выполняют электронный усилитель ЭУ с релейным блоком РБ и блок из двух электродвигателей с редуктором Р и реостатом обратной связи РОС.
Каждый из электродвигателей состоит из короткозамкнутых роторов Р1 и Р2, сидящих на общем валу, и статоров С1 и С2, закрепленных в корпусе блока. Выходной вал может вращаться в двух направлениях в зависимости от того, какой из статоров окажется под током. При этом от вала через редуктор Р и эксцентриковый механизм соответственно открывается или закрывается клапан К на впуск пара в нагревательную камеру подогревателя П.
Когда температура продукта соответствует заданной, мост М находится в равновесном состоянии, на вход усилителя ЭУ напряжение не подается и вал электродвигателей неподвижен. При отклонении температуры от заданной на входных зажимах электронного усилителя появится напряжение, фаза (направление) которого зависит от направления нарушения равновесия моста (т. е. от повышения или понижения температуры подогревателя). При изменении знака нарушения равновесия на обратный фаза напряжения меняется на 180°. В результате этого выходной вал редуктора Р получает угловое перемещение в ту или другую сторону в зависимости от того, какой из статоров включен под напряжением блоком РБ. Клапан К перемещается в соответствующем направлении, чем и поддерживается температура нагревателя на данном уровне.
Описанная система работает по принципу использования отклонения параметра от заданного значения. Она представляет собой замкнутую цепь звеньев: подогреватель П — термометр ТС — усилитель ЭУ с блоком РБ — блок двух электродвигателей — подогреватель П. Регулирование параметра системой осуществляется по замкнутому циклу, и системы такого вида называются системами автоматического регулирования замкнутого цикла.
На рис. 123 показана другая система автоматического регулирования. Например, в котле 1 требуется регулировать температурный режим в соответствии с технологией концентрирования (уваривания) виноградного сусла. Тепловой режим в; котле может отклоняться от заданного вследствие изменения количества сусла и пара, поступающих в котел, и количества продукции, удаляемой из котла. Очевидно, система автоматического регулирования должна иметь такие звенья, которые своим действием влияли бы на эти возмущающие воздействия так, чтобы технологический процесс протекал по заданной программе.
Изменение расходов сусла, пара и готовой продукции осуществляется с помощью регулирующих клапанов 11, 12 и 13 с мембранными пневмоприводами. Камеры над мембранами регулирующих клапанов питаются сжатым воздухом от нижних камер воздухораспределительных коробок 3, 5 и 8. В верхних камерах этих коробок поддерживается постоянное давление воздуха, поступающего от компрессора. Давление в нижних камерах регулируется путем изменения степени открытия воздушных клапанов, управляемых кулачками 2, 4 и 7. Они приводятся во вращение с заданной и постоянной угловой скоростью через вал 6 и редуктор 9 от электродвигателя 10. Так как кулачки имеют специальный профиль, то давление сжатого воздуха над мембранами регулирующих клапанов 11, 12 и 13 изменяется по заданной программе.
Описанная система основана на использовании второго принципа автоматического регулирования — регулирования по возмущающему воздействию (по поступлению пара, сусла и выходу готового продукта). Система представляет собой три не зависящие одна от другой разомкнутые цепи звеньев. Параметр регулируется каждой цепью по разомкнутому циклу. Поэтому системы такого вида называются системами автоматического регулирования разомкнутого цикла.
Звенья систем автоматического регулирования.
Основными звеньями системы автоматического регулирования (САР) являются: объект регулирования, датчики, управляющее устройство, усилитель, исполнительный механизм, обратная связь, автоматический регулятор.
Объекты регулирования. Обычно под объектом автоматизации понимается совокупность технологического оборудования, в котором необходимо поддерживать заданные параметры технологического процесса, например вакуум-выпарной аппарат — необходимо поддерживать требуемое разрежение или концентрацию продукта; или обжарочная цепь — необходимо поддерживать постоянную температуру масла и др.
Датчики. Они являются одним из основных звеньев САР. Это звено находится под непосредственным воздействием измеряемой регулируемой величины и имеет назначение — преобразовать ее в другую величину, удобную для использования управляющим устройством системы.
Существует много разнообразных конструкций датчиков. При автоматизации процессов консервирования значительное распространение получили электрические датчики, преобразующие неэлектрические величины в электрические.
Датчики-преобразователи, которые преобразуют выходной сигнал измерительного элемента в активное или реактивное емкостное или реактивное индуктивное сопротивление, называются параметрическими датчиками, а в электродвижущую систему — генераторными датчиками. Наряду с электрическими довольно широкое применение получили пневматические датчики, которые преобразуют величину отклонения регулируемого параметра от заданного значения в выходной сигнал в виде давления сжатого воздуха.
Параметрические датчики в зависимости от природы электрического сопротивления, получаемого на их выходе в процессе преобразования входной величины, разделяются на три группы: датчики активного сопротивления, индуктивные и емкостные. Весьма распространенными датчиками активного сопротивления являются электрические термометры сопротивления, имеющие обмотку из тонкой металлической проволоки, изменяющей свое сопротивление в зависимости от температуры. К электрическим термометрам сопротивления относятся также термометры (полупроводниковые сопротивления). Эти датчики в несколько раз чувствительнее металлических. Отдельную группу датчиков активного сопротивления составляют тензометры, применяемые для измерения деформаций растяжения и сжатия. Сопротивление проволоки или пластинки тензодатчика изменяется в зависимости от нагрузки: при деформации растяжения сопротивления пропорционально увеличивается, а при сжатии — уменьшается.
Индуктивные датчики — устройства, в которых перемещение сердечника осуществляется за счет изменения индуктивного реактивного сопротивления.
Емкостные датчики представляют собой в большинстве случаев плоские и реже цилиндрические конденсаторы. В них преобразование входной величины в емкостное реактивное сопротивление происходит путем изменения расстояния между электродами, площади электродов и уровня электрической среды.
Генераторные датчики — это термопары, тахогенёраторы и др.
Термопара представляет собой два электрода из разных металлов, скрученных и сваренных на одном конце. Электроды изолированы друг от друга и помещены в защитный чехол. При различной температуре концов термопары в ее электрической системе появляется ток, пропорциональный изменению температуры.
Тахогенераторы используются при регулировании скорости вращения валов, и по устройству и принципу действия тахогенераторы представляют собой небольшие генераторы постоянного и переменного тока.
Пневматические датчики предназначены для измерения перепада давлений (расхода), уровня, давления жидких, парообразных и газообразных средств в пневматических системах автоматического регулирования. Основным рабочим органом такого датчика является сопло с заслонкой. Перемещением заслонки перед соплом изменяется давление сжатого воздуха в системе.
Управляющие устройства САР. К ним относятся электрические мосты, электрические и неэлектрические реле. Сигнал, поступивший на пульт управляющего устройства через усилитель, может изменяться и преобразовываться в выходную величину плавно (в мостах) или скачкообразно (в реле). Конструктивные изменения этих звеньев могут быть весьма разнообразными.
Исполнительные механизмы. Они являются составным звеном регулятора непрямого действия и управляют перемещением регулирующего органа под воздействием сигнала, полученного непосредственно или через усилитель от управляющего устройства. Так как сигнал может быть электрическим, гидравлическим или пневматическим, исполнительные механизмы могут быть электрическими, гидравлическими или пневматическими.
Электрические механизмы бывают позиционного и пропорционального регулирования.
Гидравлические механизмы выполняют функцию преобразования разности давлений рабочей мощности в механические перемещения регулирующего органа.
Пневматические механизмы предназначены для преобразования управляющего сигнала (давления сжатого воздуха) регулятора в механические перемещения регулирующего органа с помощью мембранного или поршневого привода. Мембранный привод имеет линейную характеристику, т. е. зависимость между давлением воздуха и перемещением штока привода линейна. Исполнительные механизмы с поршневым пневмоприводом сложнее в изготовлении, но они используются тогда, когда необходимы большие перемещения регулирующего органа (до 0,3 м).
Автоматический регулятор. Он состоит не менее чем из трех элементов: чувствительного (датчика), регулирующего (исполнительного механизма) и элемента связи между ними.
Регуляторы можно разделить на следующие основные типы: двухпозиционные, астатические, статические (пропорциональные), изодромные.
Двухпозиционные регуляторы имеют регулирующий орган, который может занимать только два положения: полное открытие или закрытие прохода жидкости, пара, воздуха, а также включение или выключение электрической цепи.
Астатическим называют регулятор, регулирующий орган которого перемещается в одном направлении при отклонении регулируемого параметра. Это происходит до тех пор, пока регулируемый параметр не будет иметь заданное значение.
Статические регуляторы имеют регулирующий орган, который изменяет свое положение таким образом, что каждому значению регулируемого параметра соответствует только одно определенное положение регулирующего органа.
Изодромные регуляторы обладают свойствами астатических и статических регуляторов. Регулирующий орган изодромных регуляторов может занимать любое положение в пределах своего поля, поддерживая регулируемый параметр на заданном значении.
По способу действия регуляторы бывают прямого и непрямого действия. У регуляторов прямого действия измерительный элет мент (мембрана, поплавок и т. п.) воздействует непосредственно на изменение положения регулирующего органа за счет энергии, получаемой от объекта регулирования. У регуляторов непрямого действия регулирующее воздействие передается регулируемому параметру от измерительного элемента или датчика через специальные устройства (усилитель, исполнительный механизм и пр.), действующие от постороннего источника энергии.
На рис. 124 показаны системы непрерывного регулирования.
Статический регулятор прямого действия (рис. 124, а) предназначен для поддержания постоянного давления в объекте регулирования У. Это давление подводится в камеру над мембраной 3 по импульсной трубке 2. Мембрана жестко связана с клапаном 6 при помощи штока 5 и уравновешивается снизу усилием пружины 4. Предположим, что режим работы регулятора
установившийся, при этом нагрузка Qy на объект постоянна и давление Ру
соответствует заданному значению [графики P = f(t) и P = f(Q) на рис.
124, бив].
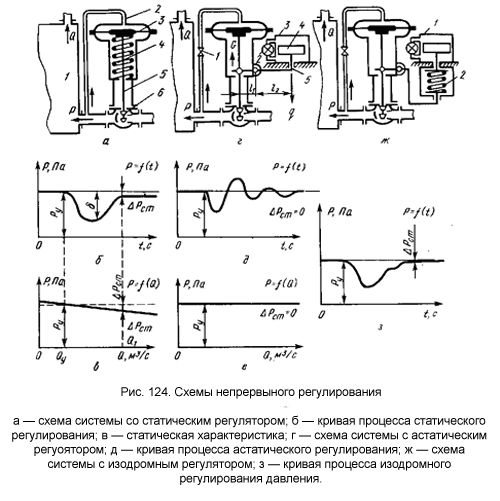
Допустим, нагрузка увеличилась и приняла значение В связи с этим давление Р объекта уменьшится по сравнению с заданным. Мембрана усилием пружины прогнется вверх и увеличит открытие клапана. Давление будет восстанавливаться, но разжатая пружина развивает меньшее усилие по сравнению с прежним, и поэтому для уравновешивания усилия пружины и для нового установившегося состояния объекта понадобится давление, также несколько меньшее заданного. Разность между заданным давлением и фактическим после приведения регулятора в установившееся положение называется статической ошибкой (ΔР, а разность значений в момент работы регулятора в неустановившемся состоянии (значение δ) называется динамической ошибкой.
Регулятор по своему принципу не может работать без статической ошибки, он применяется в тех случаях, когда ведение технологического процесса допускает такие ошибки. Чем больше отклонение нагрузок от величины Qy, тем больше статическая ошибка. Эти регуляторы обеспечивают надежное регулирование и имеют простую конструкцию.
Существенным недостатком рассмотренной САР является наличие статической ошибки. Это вызвано жесткой зависимостью положения регулирующего органа от отклонения регулируемого параметра или наличием пружины.
На рис. 124, г показана схема той же САР, но с конструктивно измененным статическим регулятором: вместо пружины применен рычаг 5 с грузом 4.
В данном случае состояние равновесия мембраны выразится уравнением
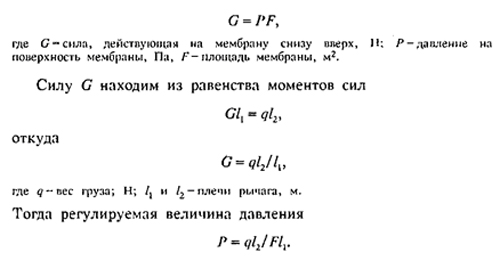
Но величины l2, l1, q и F всегда постоянны при работе регулятора. В связи с этим при любой нагрузке Q на объект давление Р будет регулироваться без статической ошибки. Это свойство регулятора показано на рис. 124, с приведенной регулировочной характеристикой Р = f(Q) = const.
Такие автоматические регуляторы, работающие без статической ошибки, называются астатическими, но они имеют следующий основной недостаток: в переходном процессе наблюдается плохая устойчивость регулирования, при резком изменении давления над мембраной регулирующий орган не будет перемещаться плавно.
Под действием сил инерции груз будет занимать крайние положения вместе с клапаном. Возникает многократное перерегулирование, что видно на приведенном графике Р = f(t) на рис. 124, д. Для частичного исправления этого недостатка используют приспособление для уменьшения скорости перемещения регулирующего органа. В данном случае (см. рис. 124, г) на импульсной трубке установлен дроссель 1 и имеется гидравлический демпфер 3 с обводным каналом и игольчатым клапаном 2.
Астатические регуляторы обычно используются в объектах с малой скоростью изменения параметров.
Рычажно-демпферные устройства и пружины в рассмотренных регуляторах выполняют роль обратных связей, так как их действие направлено противоположно регулирующему воздействию. При введении рычажно-демпферного устройства (гибкой обратной связи) качество регулирования улучшается после переходного процесса и одновременно ухудшается в переходных процессах (см. рис. 124, д), при введении пружины (жесткой обратной связи) наблюдается обратное изменение свойств (см. рис. 124, б). Очевидно, для того чтобы сделать регулятор, лишенный этих недостатков, следует применять обратную связь из демпфера и пружины.
На рис. 124, ж показана схема САР с принятыми конструктивными изменениями регулятора. В данном случае при изменении нагрузки на объект и стремлении регулятора ликвидировать возмущающее воздействие в начале переходного процесса поршень демпфера 1 стремится сохранить состояние покоя и преобладающую роль в регулировании выполняет пружина 2, обеспечивая хорошее затухание колебаний, как в статическом регуляторе. В конце переходного периода, когда скорость процесса уменьшается, преобладающую роль играет гидравлический демпфер, работа которого направляется на удаление статической ошибки регулирования. Кривая процесса регулирования (рис. 124, з) наглядно показывает улучшение показателей работы регулятора, в котором совместились достоинства статического и астатического регулятора.
Примененное в этом случае устройство называется упругой обратной связью или изодромным устройством. Регуляторы, выполненные на этом принципе, называются изодромными регуляторами.
В практике применяются изодромные регуляторы, основанные на использовании самых различных принципов действия: медленного перетекания жидкости или воздуха из одного сосуда в другой (гидравлические изодромы); медленного охлаждения термопары, покрытой слоем изоляции (электротермические изодромы); разряда электрического конденсатора через активное сопротивление (электрические изодромы) и пр.
Автоматизация отдельных аппаратов консервного производства.
Автоматические поточные линии консервного производства оснащены многочисленными приборами и регуляторами, обеспечивающими необходимый контроль и регулирование технологических процессов. Ниже рассмотрены примеры автоматизации работы отдельных аппаратов консервного производства.
В паромасляной печи 7 (рис. 125) постоянная температура масла поддерживается с помощью автоматического регулятора температуры. Чувствительным элементом его является баллон 3 манометрического термометра, в котором повышение температуры измеряемой среды (масла) преобразовывается в повышение давления в системе, состоящей из термобаллона и капилляра 4, соединяющего термобаллон с регулятором 2. В последнем установлена изогнутая плоская пустотелая пружина; один конец ее соединен с капилляром, второй, отклоняемый при изменении давления, — с заслонкой сопла, в которое подается сжатый воздух после очистки в фильтре 6 и снижения давления в редукторе 7.
В зависимости от температуры масла регулятор 2 посылает командный импульс мембранному клапану 5, установленному на паропроводе, подающем пар в нагревательные элементы паромасляной печи.
Автоклав 15 периодического действия (рис. 126) оборудуется запорно-регулирующими клапанами 7, 2, 72, 13 и 14 нормально закрытого исполнения на магистралях подачи воды, пара, воздуха, слива и дренажа соответственно. Температура в автоклаве измеряется манометрическим газовым термометром 3 с
пневматическим выходным сигналом, давление — бесшкальным сильфонным
манометром 11 с пневматическим выходным сигналом. Температура и давление
в автоклаве регистрируются пневматическим вторичным прибором 10.
Программа изменения задания по температуре в автоклаве вырабатывается
программирующим устройством 6. Регулирование температуры по программе
осуществляется пропорциональными регуляторами 5 и 4, управляющими через
регулирующие клапаны 1 и 2 подачи воды и пара. Регуляторы 4 и 5 и
командно-программирующее устройство 6 оформлены в виде программного
регулятора ПРТ-2.
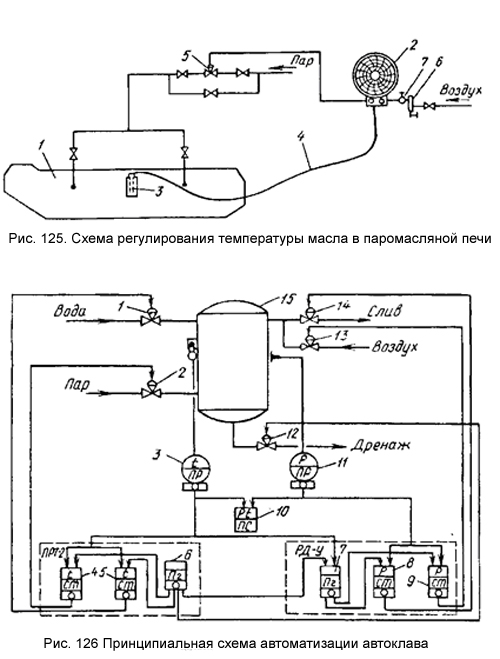
Программа изменения задания по давлению в автоклаве вырабатывается программирующим устройством 7. Регулирование давления в автоклаве осуществляется пропорциональными регуляторами 8 и 9, управляющими через регулирующие клапаны 12 и 13 верхним сливом воды и подачей воздуха. Регуляторы 8 и 9 и программирующее устройство 7 оформлены в виде программного регулятора РД-У.
Автоматический гидрорегулятор давления в прессовой камере шнекового пресса работает следующим образом (рис. 127). Плунжерный насос 2, приводом которого служит кулачковый механизм, установленный на валу 1, подает масло из резервуара 3 по маслопроводу 6 в систему регулятора. Величина давления в системе регулируется устройством 4 и проверяется по манометру 5. В
цилиндрах 7 давление передается на запорный конус 10 пресса с помощью
поршней 8 и штоков 9. Запорный конус насажен на трубу, внутри которой
проходит вал 1 пресса, и может перемещаться вдоль этого вала.
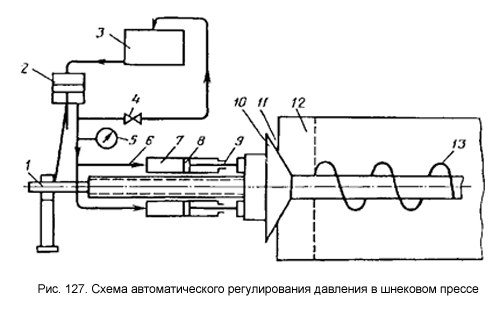
В исходном положении под давлением поршней 8 конус прижат к выходному отверстию пресса и зазор между ними закрыт. При работе пресса накопившиеся в камере сжатия выжимки давят на конус, преодолевают заданное ему сопротивление и отодвигают его. Образуется кольцевое отверстие 11, через которое выжимки шнеком 13 выносятся из прессовой камеры. Величина этого отверстия при установившемся режиме работы пресса задается заранее положением конуса на его оси и фиксируется гайкой.
При повышении давления в камере сжатия 12 выжимки отодвигают конус, при этом длина камеры как бы увеличивается, что снижает давление, выход выжимок возрастает и равновесие устанавливается на заданном давлении. Если же давление в камере сжатия падает, конус прижимается к стенкам цилиндра, уменьшается зазор и создается препятствие выходу выжимок. Продолжается это до тех пор, пока давление в камере уравновесит давление конуса. Таким образом гидрорегулятор поддерживает постоянную величину сжатия в камере пресса, что соответствует заданной величине влажности выходящих выжимок.
Автоматический стабилизатор потока продукта (рис. 128) используется в пастеризационных пластинчатых теплообменниках. Это создает благоприятные условия для работы автоматики, устраняет опасность нарушения температурных режимов в секциях аппарата при внезапном увеличении подачи.
В схеме пастеризационно-охладительной установки стабилизатор потока включен в линию нагнетательного трубопровода питательного насоса.
Продукт входит в стабилизатор снизу через штуцер 1 и проходит затем по кольцевому зазору между корпусом 2 и направляющей гильзой 3 до окна 4, через которое затем поступает в регулировочную камеру 5. Здесь поток продукта обтекает грибок 6, диаметр которого строго согласован с внутренним диаметром регулировочной камеры. Вследствие этого при нормальной подаче продукта по обе стороны грибка создается перепад
давлений, достаточный для поддержания всего узла гидродинамического
поплавка, состоящего из грибка, штока 7 и цилиндрического золотника 8, в
«плавающем» состоянии. При этом золотник частично прикрывает окно 4,
создавая дополнительное сопротивление движению жидкости.
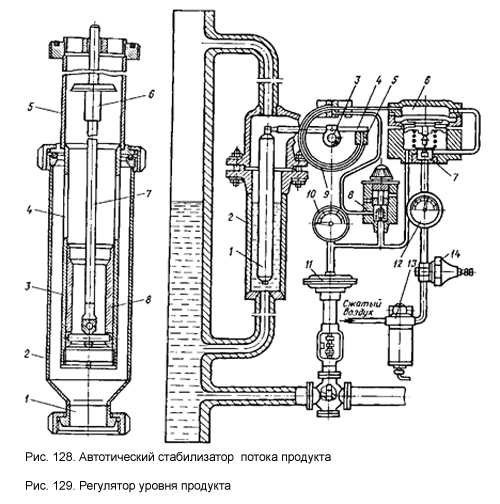
Стабилизатор потока автоматически выравнивает общее сопротивление нагнетательной линии центробежного насоса и поддерживает подачу насоса на постоянном, заранее установленном уровне.
Если поток продукта имеет тенденцию к увеличению, например, вследствие уменьшения гидравлического сопротивления аппарата или повышения напора продукта при входе в стабилизатор, грибок поднимается вверх и золотник уменьшает проходное сечение окна. При этом сопротивление стабилизатора автоматически увеличивается, компенсируя уменьшение сопротивления аппарата. При увеличении сопротивления аппарата перепад давлений по обе стороны грибка уменьшается и золотник опускается вниз, увеличивая проходное сечение окна и вновь выравнивая общее сопротивление нагнетательной линии.
Важное значение в системах автоматического управления процессами выпаривания имеют устройства, поддерживающие определенный заданный уровень продукта в аппарате. В случае снижения уровня продукта может произойти «оголение» нагревательной поверхности (змеевиков, паровой рубашки, пучка кипятильных трубок и т. п.), в результате чего образуется нагар. Это приводит к ухудшению качества продукции и снижению коэффициента теплопередачи.
Измерение уровня жидкости и автоматическая стабилизация необходимого его значения в аппаратах, работающих под давлением или разрежением, осуществляются с помощью камерных цилиндрических регуляторов уровня (рис. 129). Действие их основано на изменении веса цилиндрического стержня (буйка) в зависимости от глубины его погружения в среду, уровень которой измеряется или регулируется.
Поплавок 1 помещен в камере 2 и может перемещаться по вертикали. Перемещение поплавка передается пневматическому устройству регулятора через гибкую стальную трубку 3. Под действием веса поплавка гибкая трубка скручивается, в зависимости от степени погружения поплавка в жидкость изменяется усилие, действующее на эту трубку. При снижении уровня жидкости усилие, действующее на трубку, увеличивается в связи с уменьшением выталкивающей силы и гибкая трубка скручивается. При повышении уровня жидкости усилие уменьшается и гибкая трубка раскручивается на некоторый угол. Одновременно с трубкой поворачивается стержень заслонки 4.
Эта заслонка, связанная со свободным концом стержня, поворачивается вместе с ним, прикрывая или открывая отверстие сопла 5, через которое восходит струя воздуха. Это приводит к изменению давления воздуха в камере 6 и к изменению положения золотника 7, через который воздух подается к исполнительному мембранному клапану 77. Он установлен на линии подачи продукта в сосуд, в котором необходимо поддерживать определенный его уровень.
Воздух в наружную полость сопловой трубки 9 подводится через клапан 8. При увеличении давления воздуха трубка 9 раскручивается на некоторый угол и отводит сопло 5 от заслонки 4, что приводит к уменьшению давления воздуха в линии подачи его к исполнительному механизму. При уменьшении давления трубка скручивается и приближает сопло к заслонке, что приводит к увеличению давления воздуха в линии, где установлен клапан 17.
Давление воздуха, поступающего к регулятору и от регулятора к исполнительному механизму, контролируется манометрами 10 и 12. На линии для подвода сжатого воздуха установлены фильтр 13 и редуктор 14. Изменение давления воздуха в пневматической камере исполнительного механизма приводит к перемещению его золотника, в результате чего увеличивается или уменьшается подача продукта в выпарной аппарат, и вследствие этого уровень его стабилизируется.
Системы автоматического управления комплексными технологическими линиями.
В предыдущем разделе рассматривались отдельные приборы и регуляторы. Ниже описывается система автоматического управления процессом асептического консервирования, на примере которой рассмотрим, как эти приборы автоматически контролируют аппараты и управляют целым комплексом их.
Линии асептического консервирования для плодовых и томатных полуфабрикатов типов А9-КСИ и А9-КСК содержат следующие контуры контроля и регулирования (рис. 130):
- автоматическое регулирование температуры в пароконтактном теплообменнике II по пропорционально-интегральному закону на основе изменения количества пара, подаваемого в продукт;
автоматическую двухкаскадную стабилизацию давления в пароконтактном теплообменнике II, основанную на изменении проходного сечения регулирующего органа на выходе из теплообменника и стабилизации давления в камере стерилизации III;
-
автоматическую индикацию и регистрацию температуры в емкости предварительного резервирования I, пароконтактном теплообменнике II, камере стерилизации III, вакуум-охладителе IV, температуры воды в барометрическом конденсаторе, а также сигнализацию отклонения от заданного диапазона этих параметров;
-
автоматическое регулирование давления в камере стерилизации III по пропорциональному закону регулирования на основе изменения количества пара, выпускаемого в атмосферу из парового пространства камеры стерилизации;
-
автоматическое регулирование уровня продукта в камере стерилизации III, вакуум-охладителе IV по трехпозиционному закону, а также регулирование уровня воды в барометрическом конденсаторе;
-
световую сигнализацию на щите управления технологическим оборудованием нормальных и критических значений основных параметров и звуковую сигнализацию их критических значений;
-
световую и звуковую сигнализацию на щитах контроля блоков резервуаров критических значений давления в них и повышения уровня продукта до заданных значений;
-
дистанционное управление со щита всеми электрическими приводами: блокировки заполнения очередного резервуара при достижении в нем верхнего уровня, выключения насоса, подающего продукт в емкости предварительного разервирования по команде щита управления.
В резервуаре предварительного резервирования
I автоматический контроль за верхними предельным и рабочим уровнями
продукта осуществляется электронным сигнализатором уровня СУ1 с тремя
датчиками, за нижними уровнями — аналогичным прибором СУ2. В качестве
первичного преобразователя температуры в этом резервуаре служит
термометр сопротивления ТС1, подключенный к шеститочечному мосту ИН 1 с
регистрацией и трехпозиционным регулированием.
Автоматическая
стабилизация давления в пароконтактном теплообменнике II обеспечивается
в режиме стерилизации на основе стабилизации давления в последующем
аппарате — камере стерилизации III регулятором давления прямого
действия, а в режиме циркуляции — регулятором давления прямого действия,
установленным на трубопроводе циркуляции в резервуаре I.
Автоматическая
стабилизация температуры стерилизации в пароконтактном теплообменнике
осуществляется системой, состоящей из термометра сопротивления ТС2,
подключенного к мосту ИН2, с дистанционной передачей показаний. Выход
дистанционной передачи подключен к суммирующему входу пропорционально
интегральному регулятору УР5. К другому входу этого регулятора подключен
выход преобразователя давления МН8, установленного на трубопроводе
подачи пара к регулирующему клапану ИМ8 с исполнительным механизмом,
изменяющим по команде регулятора УР5 подачу пара в пароконтактный
теплообменник II.
Сигнальный контакт вторичного прибора ИН2
обеспечивает в автоматическом режиме (совместно с регулятором УР4)
управление клапанами П11, П12, П13, изменяющими направления потока
продукта из пароконтактного теплообменника.
Уровень продукта в камере
стерилизации поддерживается в диапазоне, определенном расположением
датчиков сигнализатора уровня СУ2. Этот сигнализатор управляет клапанами
П16 и П17 в автоматическом режиме. При отклонении давления в камере
стерилизации и в трубопроводе, соединяющем камеру стерилизации с
вакуум-охладителем, от заданного значения продукт направляется на
циркуляцию, а клапаны П16 и П17 закрываются. Давление контролируется
электроконтактными термометрами МН11 и МН12.
Температура в
вакуум-охладителе автоматически контролируется и регистрируется
вторичным прибором ИН1, первичный преобразователь которого ТС6
установлен ниже нижнего рабочего уровня. При повышении температуры в
вакуум-охладителе выше заданного предела регулятор УР4 дает команду на
циркуляцию путем открытия клапана П22 и закрытия клапана П24. В
вакуум-охладителе предусмотрены автоматический контроль и регулирование
уровня продукта в заданных пределах. Имеются две системы, в первичных
преобразователях которых используется гидростатический и
кондуктометрический принципы действия.
Сигнализация и автоматическая
стабилизация уровня воды в конденсаторе V осуществляется сигнализаторами
уровня СУ1 и СУ4, датчики которых расположены на верхнем и нижнем
рабочем и аварийном уровнях. Сигнализатор СУ4 управляет трехпозиционным
клапаном К7, который регулирует проход воды от откачивающего насоса Н3.
Для
контроля сигнализации и блокировки критических значений уровней и
давления в резервуарах VI на них устанавливаются электроконтактные
манометры и кондуктометрические преобразователи уровня.
Преимуществами
описанной системы автоматического управления являются комплексное
решение вопросов управления всеми режимами линии, большой объем
автоматизации, позволяющий эксплуатировать достаточно сложное
оборудование минимумом обслуживающего персонала.